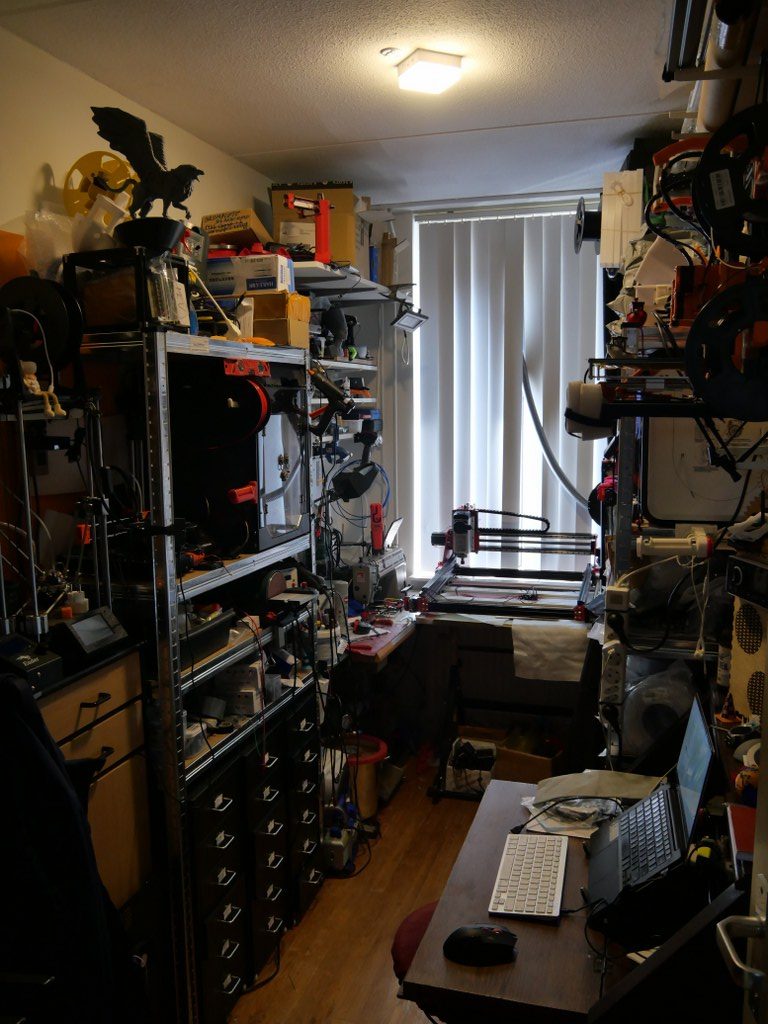
My mini shop
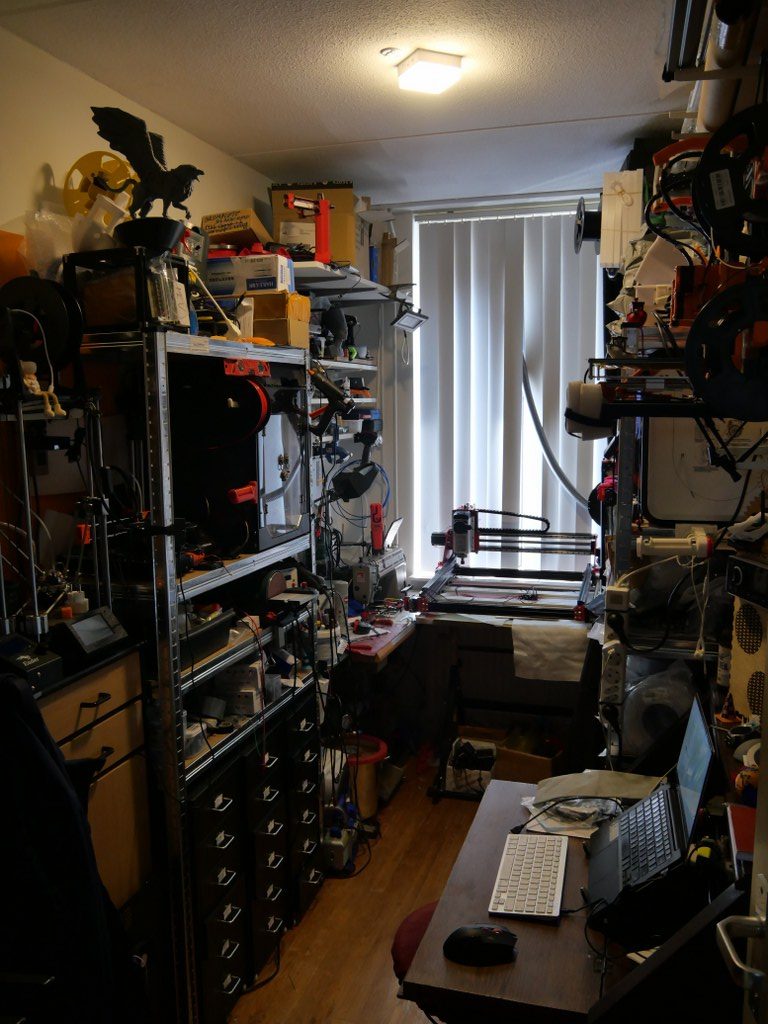
2021-05-11
I got the Mellow Fly 407 board in today, and it now works awesome!
I hooked the Mellow dedicated wifi unit to EXP 1 and EXP2 and to the serial TFT connection, programmed the microSDcard offline on the PC with the files from the proposed Github site and it all went great! (The little added user manual is very good, just follow the directions and it can’t go wrong!)
Burnt the board’s firmware first, then the firmware of the wifi esp module and after setting up the wifi with YAT via USB, I programmed the wifi settings. Then, with the Duet’s WDC PC-remote console via wifi, I uploaded the FLY 407 motherboard with all the latest available firmware: RRF3.4 beta and the latest wifi- and DWC versions.
Then, I removed the serial connection between the TFT connection on the motherboard and the wifi module and plugged in the BTT 2.4 inch TFT at the same serial port. Since there is only 1 tft port available, I use the same serial port as I used for programming the esp wifi module. I already put the RRF3 firmware on the TFT unit.
Well, the results are awesome! On the TFT after connecting you see the extruder step from 0 to 1-2-3-4 and back to 0 so this all works very nice!
I must be honest here: I also tried the Mellow 7 inch screen but this is not yet really working as well to me as the little BTT screen IMHO. The Fly screen is a lot bigger, though, and the Fly 7 inch TFT has great potential. I know that it will also take some getting used to the FLY’s TFT screen layouts. The access to the macro and gcode directory is nice, but since everything is placed differently than the PanelDue screens, it might just take some time to appreciate it more.
In mid-June 2020, I started using the Geeetech A30M desktop 3d printer.
The printer can print 2 colors mixed with 2 filament geared drive units on top of the frame and a fan for each feed to the combined hotend.
A few adjustments are needed on this printer if you really want to work well with it.
First of all, I had a lot of trouble with the standard noise from the 24 Volts fan under the bottom plate, which is supposed to provide cooling for the motherboard. This fan is always running at full power.
I put a controller in between with controls on the left side, through a drilled hole. I secured the controller with 2 tie-wraps through the cooling slots on the left side. The dial just comes through the case and you can hardly see it. Most motherboards I use don’t need a fan for cooling because they are placed freely in the open frame but the A30M has a closed case so a little air circulation is necessary. Plan is to add a thermostat control so the knob is no longer needed. Later. The controller is set to the position that there is a lot of air movement but without the whirring of the fan.
Second modification is the addition of a Geeetech 3d touch on the hotend. The bracket was included with the printer, suitable for both a thick inductive sensor and the 3d touch sensor. What’s nice is that the software (or firmware, if you will) as suitable from the factory for autoleveling. Do pay attention to the correct placement of the connectors, from the front view the brown and black wires should be mounted to the right.
The disadvantage is that the firmware from factory does not really work well with auto leveling. In the middle of the hotbed everything goes fine but with larger prints I noticed that the first layer was printed very differently, so everything kept coming loose. So now I work with manual leveling while automatic leveling is possible.
The hotbed is nice and big with a workable size of 320x320mm. The print height is 420mm.
The price was over 400 Euro, and the delivery was from Germany.
I recommend everyone to secure ALL and especially to include the block hook. My one was really not assembled properly. All threads were OK but all bolts were either too tight or not tight at all. I only found this out during the first test print. I stopped and checked everything. Pay special attention to the rollers of the hotbed. It is difficult to reach them but in my case the adjustment wheels were not set at all and did not rotate. The disadvantage of such a desktop printer is that you hardly have any space under the hotbed.
The vertical V-profiles were not mounted perpendicular to the upper profile. That is difficult to repair because everything is drilled through and bolted. I recommend installing corner stiffeners at the back in the top 2 corners. I have them on order and then they can go right on.
And… what some large printers have and the A30M does not: Additional stabilization rods to the front (or to the back, that is also possible) so that the vertical profiles cannot move. Now when you apply a little force there is about 2mm of play on it, despite the solid mounting to the desktop housing.
My experiences with CoreXY printers are excellent, so I chose a VORON for my home-built COREXY printer with a print size of 300x300x300 mm.
Developed from a large community, the VORON is one of the best and most reliable 3D printers. And this printer just looks really good!
Via AliExpress, Banggood, Reichelt, aluminiumopmaat.nl and plexiglas.nl I ordered all the stuff, according to the bill of materials I could download from the VORON site.
I printed the PETG parts on the Prusa mini at 0.15 fine.
The ABS parts (red and black) were printed on the Twotrees Sapphire plus. It took a lot of ‘tweeking’ before the ABS came out well but in the end I got a nice result!
Printed parts for the Voron 2.4 300In the end, rebuilding is not really self-building and it is more based on ordering and assembling than getting to work with the saw and drill yourself. Also the necessary 8(!) linear rails of 350mm, bearings, gears, belts, motors, electronics and so on have been ordered and the rest of the necessary stuff has been printed (25-8-2020).
For the control part I have chosen one PI Raspberry PI 4B 4GB and two pieces of SKR 1.4 turbo motherboards, according to the VORON recommendation.
Building the Voron 2.4 with the afterburner Beta1 hotend combination is illustrated by the following pictures.
Gantry ready:
Gantry of my Voron 2.4 300Housing and skirts underside with Z-motors yet without the gantry mounted:
Below: The 9 mm drive belts of the 4 Z-axes placed:
And the assembled base plate with the rails and controls, power supplies and so on (printer turned over):
We are still waiting for the bearings for the Alpha and Beta drives in the gantry. These bearings are used to make a tension roller per 2 pieces. I had originally bought idler bearings for this purpose, but the diameter of the collar of these bearings is just too large.
Too bad but then I have to work on the Raspberry PI4B in combination with 2 times SKR V1.4 turbo motherboards. The PI will make a new config.bin via Klipper for the SKR V1.4 motherboards so the PI can drive both SKR boards at the same time. On the main board will be Alpha and Beta and the extruder plus the extruder heater, on the other (Z) board the 4 Z-motors and bed heater. By itself a Duet with expansion board could have been an option too, but the Voron designers made it with the PI, Klipper and 2 SKR boards. And I try to stay as close to the design as possible . -)
Below: Threading the straps, no picture used. Just start somewhere and you’ll end up right. Oh yes, also changed the sensor in the config from NC to NO..
Below: In addition to the 24Volt 200 Watt hotbed nevertheless also added the 500 Watt 230V. With only the 24V version it took more than 20 minutes to get to 110 degrees Celsius…
Old:
And new— no PID run done yet..)
Below: The steel plate is placed on the sticky magnet sheet.
Below: First print…. I had to search for the Z offset adjustment and the extruder turned the wrong way around. Also the gantry leveling took some thought, you actually have to make the basic setting with a ruler, otherwise the leveling takes a long time. Nice is that a bed mesh leveling is not necessary anymore, but of course it can be done. You turn a home and because the nozzle always calibrates the Z on the mechanical Z endstop, and the gantry does all the leveling, you always have a good first layer. Unless the bed warps but with such a thick plate that seems almost impossible. Just to be sure, I did include a bed_mesh profile in the config.g. By the way I just used a 24 V aluminum hotbed as a base because my 8 mm 310×310 plate turned out to be a cut plate instead of sawn. And a cut sheet turns out to be non-flat on the cut sides by default, unfortunately. Flattening costs more than a new plate, maybe that will come sometime….
And with enclosure, camera and the TOP LED’s:
Afterword:
In practice, I fixed a few more minor flaws, including:
Extruder tuning. The donor extruder turned out not to pick up the filament properly.
First I tried to put a ring in between the left side of the shaft, but then the nylon gear on the right side of the shaft gets tight and the housing can’t be closed completely anymore….
I ended up using a spare set of dual drive extruder gears and swapping the set of gears. With that, the filament was properly aligned with the running path of the gears. See the picture how it was at first:
Hotend tuning
After the PID runs of hotend and heated bed, my chosen assembly of the custom ED6 heater block, the heatbreak pipe and the cooling element turned out not to fit together properly. The result was that when the filament was extracted, a thick piece was always stuck at the end. This was caused by the heatbreak pipe not fitting tightly on the nozzle. There should be no play between them. I completely demounted the filament and screwed the heatbreak pipe 2 turns less into the cooling element with red threadlocker. Let it harden for a day and then I assembled the rest. By the way, I also mounted the teflon version of the heatbreak pipe in stead of the titanium version. The tintanium version was to my experience a bit too stiff. Or my filament was too old or inferior. In any case, after the modification, everything works without problems.
Hotbed, TPU and ABS
To print TPU and ABS without brim or skirt without warping I bought a magnetic PEI steel plate with coarse profile. It really works perfectly. Both ABS at 110 degrees sticks nicely and TPU at room temperature sticks nicely too. And the removal is also without problems. Occasionally I spray a little hairspray on the plate but I don’t think that lacquer is really necessary at all. It is meant to make the removal easier.
Tension of the belts
I tried getting the belts at the same tension, this was not that easy. Finally I ended up with a mechanical way of measuring tension after putting 1 at my desired tension and comparing this as reference with the other to be compared belts. So, for the Alpha and Beta belts I first did a ‘good feeling’ setting and then I used my old trunk scale weight device to measure the tension when pulling the belt A. Then, I used the device to measure at the same place for B. And I repeated this for the 4 vertical belts.
Alignment
Aligning the machine is also a bit of a challenge…
You must assume that your frame is square and straight. You have to check this thoroughly. Both vertically, horizontally and diagonally. Then you can adjust the gantry. Loosen and remove the A and B belts. Or do the alignment BEFORE placing the belts.
Fix the horizontal position of the Gantry otherwise you can’t align at all. Place 4 equal distance blocks of about 10-15 cm under the sliders of the vertical linear rails on the lower 2020 profiles, in the 4 corners through which the gantry rests stably. I have placed position holders under all MGN9 vertical linear rails afterwards so that the rails cannot slide in the 20×20 V profile. If you use ‘regular’ 20×20 extrusion profile you don’t have a problem because there is enough ‘meat’ left for attaching your rail to the profile. With V-profile, the groove is a bit wider and it is very difficult to mount the rails neatly without tools in the groove. My frame is of V-rail profile and the gantry of plain 2020 profile.
The alignment of the gantry I started at the back. Loosening all screws a bit, including the screws of the convex connectors that hold the gantry to the linear rails. By the way, I see some builders placing these screws with multiple spring washers. I’m going to do that too…
At the rear of the gantry, push the gantry completely against the rear. There should be no gap between the XY joints and the frame. PS: Leave the endstops off for a while at this action!
While the gantry is sitting against the back, tighten the XY joints and the sliders of the X-axle as well. (the side of the endstops holder is temporarily secured with 2 screws)
Tighten the rear 2 gantry joints (with the convex surfaces) as well. This fixes the rear position at right angles.
Carefully slide the gantry forward. This should be possible without any effort. If not, check whether there is enough play (and if necessary loosen the screws) on the gantry joints at the front (with the convex surfaces). If you still don’t have a free run to the front, your frame is not good or your vertical rails are not seated properly. First check the correct positioning of your rails with your position tool (from the printed stock) and to be sure also unscrew the 4 screws on both front vertical rails. Try again if the sliding of the gantry goes smoothly. Still no good? Then reverse the procedure and start at the front. Try to set the gantry exactly level with the frame.
After adjusting: Test the alignment also halfway (vertically) and at the top!
As I experienced, from my 10+ 3d printers only the Prusa mini and the I3 Bear deliver adequate print quality. Even the Voron 2.4 CoreXY has problems if you look carefully at the printed results. Though all prerequisites were made to build a good printer, it was never really matching real good quality. So- in my search for the root cause of this somewhat disappointing discovery, I stumbled on some interesting stuff: The HevORT Advanced DIY 3D Printer project.
I found this website as a link from one of my fact finding searches for the cause of wobble in my linear rails that I am using for my Indymill CNC.
Obviously, the cheaper rolled linear screws with ball bearing nuts are not as good as the ones that are first cut on a lathe and are then grinded on a special machine. The better linear screws with ball bearings are specified into 10 categories from 1 to 10 where no.1 is most expensive and no.10 the least expensive. Quality is better with higher price. Prices are over 500 Dollars US for the better ones, but can mount up even higher.
If you look at the category of the rolled ball bearing screws, these take a lot of strain in the material due to the manufacturing process. The strain causes an unequal surface and therefore this can cause lateral wobble. When using these cheap linear ball bearing screws for 3d printers as Z-drives, the lateral problem can be solved by adding shifting plates as horizontal shift compensator.
On the net, a solution is given by using a couple of bearing balls (3) between magnets that are used as rolling plates on top and bottom. The shifting plate holders on top and bottom stay aligned with each other by mounting 2 magnets that attract each other on 2 sides of these plates. Please see the cutouts I took from the movie that is provided in the above mentioned link:
This can be implemented in the HevOrt BUT I feel that my Voron2.4 could really benefit also from this solution. Although the Voron is depending on the vertical linear rails for sliding up and down and a belt mechanism is making the motion happen, the mechanism that compensates for any wobble or different sizing of the frame is only a friction plate of (in my case) 2 PETG surfaces that slides on each other, 1 per vertical axle.
So, I will see what I can find or make to get the above anti-lateral wobble solution built and implemented in the Voron 2.4 asap and see what the result will be!
In 2020 I upgraded my Ender 3 with synchronised Z-axes and a new motherboard, the SKR Mini E3 V2.1.
The Ender 3 is very reliable and has been equipped with a direct drive bondtech extruder but still has the original hotend.
I chose the Ender3 to be the 3d printer on which I will attach the MMU2S. This also means that I will have to exchange the hotend/extruder combination with a Prusa Mk3S version.
Started this on May 4th, 2021. Only the printed parts were needed, all other parts were already available through sourcing form a.o. Ali. I printed everything in ABS, mostly red. For this I used 2 machines: The Twotrees Sapphire pro with enclosure for black ABS and the Voron 2.3 (300) for red ABS.
There is a firmware version for the SKR mini E3 V2.1 on Github that makes use of the MMU2S. I downloaded this version and uploaded it to the board via visual studio code maker, all works well in the test setup. Some tweaking was needed in configuration.h and in the advance config, since I am using the S-version of the MMU2 and the filament sensor was not standard ON. And- it appears that the communication port needs to change to the 2nd port. You can see it all at the Reddit page, the additional changes to the published config files are these (thnx to fixel112):
Excerpt from Configuration.h:
#define SERIAL_PORT -1
#define SERIAL_PORT_2 2 <————— This has been the issue. Uncomment that line.
#define BAUDRATE 250000
Excerpt: Configuration_adv.h
#if ENABLED(PRUSA_MMU2)
// Serial port used for communication with MMU2.
// For AVR enable the UART port used for the MMU. (e.g., mmuSerial)
// For 32-bit boards check your HAL for available serial ports. (e.g., Serial2)
//#define MMU2_SERIAL_PORT 2
#define MMU2_SERIAL MSerial2
//#define MMU2_RST_PIN 23
// Enable if the MMU2 has 12V stepper motors (MMU2 Firmware 1.0.2 and up)
//#define MMU2_MODE_12V
// G-code to execute when MMU2 F.I.N.D.A. probe detects filament runout
#define MMU2_FILAMENT_RUNOUT_SCRIPT “M600”
…
#define MMU2_DEBUG // Write debug info to serial output
#endif // PRUSA_MMU2
Next is to put everything physically on the Ender, and exchange the hotend/extruder. Then, the settings for the extrusion lengths will have to be determined. And- the buffer for the filament between the MMU2S and the filament spools has to be installed. As soon as I have it all properly installed, more pictures will follow!
I discovered that the dual display I now use for the Ender3 will only work for Marlin LCD and no longer for TFT, since the serial TFT pins will be used to drive the MMU2S unit. I exchanged the TFT/LCD unit with the original Ender3 LCD, I kept this in storage and tested it today with the Ender mini E3 V2.1 , it works very well!
The twotrees SKR Mini E3 V2.1 motherboard is really perfect for the combination with the MMU2S and the new filament sensor in the new hotend/extruder. The firmware has been updated to include the MMU2S and the AUX’s serial that was previously used for the TFT screen is now in use by the MMU! It all works!!!
Now the next thing was to get the new extruder, F.I.N.D.A. and the filament sensr to work properly.
That took some time and next on the agenda is the filament management.
I already decided to go with the original Prusa filament box with plates to hold the retracted filament for all 5 spools. The spools themselves will hang at the wall, behind the printer. I don’t have space for standing spoolholders. Underneath the spools the filament box with plates gets its place on the wall and from there the 5 PTFE tubes will run to the MMU!
Today I received my 5-in, 1-out hotend, non-mixing air cooled with 1 nozzle and 1 heater//temp sensor.
I will install it on my A30M with the Duet2wifi board+extension board (5-fold with plug-in drivers). The A30M already has independant Z-stepper motors.
The Duet2wifi has 5 stepper ports, and the expansion board also has 5 stepper ports. X,Y,2xZ, 5 Extruders is a total of 9 so this will indeed fit!
I will make new wiring for the 5 extruder steppers on top of the A30M frame with 5 bowden tubes to the hotend. Since the hotend is non-mixing, this will be a simple task to get into config.g. For the slicer- it will also be easy. Just add the extruders to a total of 5 pieces. Add the correct filaments/temps/ no offset so set offset X and Y to 0.. The work will primarily be in the tool changing files for T0-T5 where retraction- and extruding settings will be needed.
For the hotend, I have a new setup available that allows me to quickly change the nozzle.
This will make it possible to use this setup for all kind of applications.
recently (3-2021) I have been setting up my new 3d printerboard from Mellow, an STM32 board that is named FLY CDY V2. It is (almost) fully compatible with Duet2Wifi and also uses its wifi-based 3d printer management system DWC.
The config file I made for this setup is HERE
The FLY_CDY_V2 board comes completely empty so I added the firmware.bin in the /sys directory, after I had an empty SD card filled with the clean reprap directories and -files.
Next to the firmware.bin. also a board.txt is required to be available in /sys with some settings, with the following content:
//Config for fly-CDY
board = fly_cdyv2
led.neopixelPin = D.15;
//wifi pins
8266wifi.espDataReadyPin = E.10;
8266wifi.TfrReadyPin = E.12;
8266wifi.espResetPin = E.11;
8266wifi.serialRxTxPins = { D.9, D.8 };
heat.tempSensePins = { B.1 , A.3 , C.4 , D.14}; be aware that D.14 is not a temp pin but a heat pin, is this wrong??
stepper.numSmartDrivers = 6;
serial.aux.rxTxPins = {A.10, A.9};
This board.txt is already OK for 2209 drivers and for the use of the neopixels output.
In the pdf that is provided by Mellow on the Github page for the reprap STM32 boards, section FLY-CDYV2, everything is explained as to get wifi up and running, configure config.g et cetera.
In my config.g everything needed to work properly is already done, as is with my board.txt.
I made the config for a.o. a Cartesian printer with single X,Y,Z steppers and a triple hotend with 3 extruders, 1 heater and 3 nozzles.
Included is: Neopixels, BLTouch, 3 filament sensors on the X,Y- and Zmax inputs, active fans for hotend tool on fan1 and object on fan0
If so desired, sensorless homing is possible with the correct driver boards. In this version, 3 optical endstops have been used on inputs xmin, ymin and zmin.
Retraction is set OFF in this firmware by default, but may be swiched ON to make the triple hotend drip less (2 mm retract and -0.5 extrude without Z-hop), do experiment with these settings!
Please be aware that some pin names for the FLYCDYV2 board differ from the Duet’s naming convention like “bed” versus “bed-heater” et cetera.
Plus, some typical Duet2wifi extensions are NOT available like the GPIO bus.
The FLYCDYV2 has some interesting standard extra’s though, like the BLTouch connector with power, driver pins and Z probe pins, the Neopixel connector AND the 6 driver slots and 3 extruder heaters/sensors/fans!
It is quite simple to change this setup to a dual Z axis with independant Z-motors and either single extruder or a dual setup, single or dual nozzle, mixing or non-mixing.
Please see my complete ready-to-go config directory setups for this board HERE to get you started!
Also: Check my CNC Indymill running with the FLY-CDY-V2
Please donate $1 to my paypal account if you use (parts of) my developed materials so I can continue to share nice stuff for you to download
My most recent and probably last build from scratch is the dual carriage I3-based printer as shown in the below picture, in the building phase. This printer can be used either for 2 colors or for printing with soluble support PVA filament.
I decided to use sensorless homing for this build due to problems when using endstop switches. When using endstops, problems may come up because f.i. homing to the left means that the left tool will be parked against the endstop, should you use endstops. Same on the right hand side when the right hand tool is parked. I encountered difficulties that the driven sensor carriage in the middle can then get into an unknown state (or position) when both tools (carriages) are in the parked position.
If you home one of both Tools with sensorless homing, the status of the sensor carriage is always automatically known. So, since the XY position of the center (sensor) carriage is known you can always do a Z-homing at any given X-Y position and you can also do G32 and G29 without the need to carry T0 or T1 along. And- you can easlily reset an unknown status of the sensor carriage by homing it, either left or right.
Get my build plans and Configuration files for Duet2wifi HERE
The box at the left rear is for the Duet2wifi board. The 24V fan-regulated power supply is already positioned at the rear, right side.
The main challenge with this build was to get the settings perfect for the dual tools.
It took me 2 months before I got it to work perftectly for both PLA and/or Petg.
As with my previous dual color dual nozzle builds, the basics is very simple. Just define 2 tools with 2 heaters, 2 temp sensors, 2 fans et cetera.
I already envisioned the approch with the slicer(s): All offsets are done ONLY in firmware, NOT in the slicer! As far as the slicer(s) is/are concerned, the nozzles of Tool0 and 1 are at the same (X0/Y0) offset.
For the Duet, the only addition in the slicer is an M0 command as stop command for the printer. Define 2 nozzles of 1.75mm without any offset and you’re done in the slicer.
Then, you will need to set everything in your config.g at the tool section like XYZ offset and so on.
I decided to get T0 as reference, and set everything to 0 there. X=0, Y=0 and Z=0. Then, measure the differences at T1 versus T0 with calipers to start with and inport these values in the T1 toolsection in config.g.
Start a testprint and measure what to amend, take little steps and the metrics are done!
But- the hard part is- as I experienced- to get good prints without blobs and unexpected stringing, both incoming as outgoing (into and out of the printed object(s). Drying the filament also helps a lot!
In the end, I just took the same approach as with the tool settings: As little as possible retraction settings in the slicer and all except the basic print retractions are now in the configuration files that are called upon Tool changes tpre.g, tfree.g and tpost.g (for T0 and T1).
This means that you can play with retracting and extruding of filament length and speed directly at, during and after Tool changes. And- in my experience it is all affected by the type of filament you use and the temperature you are at with the hotend. Also, the fact whether you use a lower temperature during waiting has great impact.
In my experience, you should finetune the config settings for the mentioned settings per object and per type of filament.
Therefore, I decided to used this printer for only 1 goal and make the settings perfect to accomplish this goal. Right now, I have optimized this printer to print 1) PLA from 123print in the Netherlands, of a specific type and 2) PVA from the same supplier. This gives me the possibility to print complex objects with soluble supports and it works extremely well at doing this!
PM: I also added LED lights on top of the printer as an integrated feature. This makes use of a heater pin as GPIO (with a M42 P [pin] S[value intensity]) command), like the solenoids that I use to catch the carriages T0 and T1. To come from the 3.3V and max 1mA from the GPIO pin to the required 24Volts, I used small mosfet boards. All programming is done in the Duet’s config and macro files, view the below example of my stop.g file which is called from the slicer’s stop setting: M0.
; stop.g
; called when M0 (Stop) is run (e.g. when a print from SD card is cancelled)
; Also called by slicer end gcode by M0
;
M400 ; Finish move queue
M117 Cool down ; Update the LCD screen with “Cool down”
M83 ; Extruder relative mode
G1 E-2 ; Retract filament 2mm for both extruders !!
M106 S255 ; Fan at 100 to cool nozzle and bed
M104 S0 T0 ; Extruder T0 heater off
M104 S0 T1 ; Extruder T1 heater off
M140 S0 ; Bed heater off
G28 X ; Home X
M220 S100 ; Set speed factor back to 100% in case it was changed
M221 S100 ; Set extrusion factor back to 100% in case it was changed
M42 P4 S0 ; Magnet T0 off
M42 P5 S0 ; Magnet T1 off
M104 S41 T0 ; set extruder T0 to cool down
M104 S41 T1 ; set extruder T1 to cool down
;M568 R41:41 S41:41 ; set standby and active temperatures for tools 0 and 1 (or single M568 T0 R41 S41)
M116 ; wait for Tools actions as specified in above M568 instructions
G90 ; Absolute positioning
G1 Y200 ; to get objects removed easier, move bed forward
M106 P0 S0 ; Fan L object T0 off
M106 P2 S0 ; Fan R object T1 off
G28 X ; Home X
M84 ; Steppers off
M98 P/sys/ledflash.g; Perform execution of ledflash.g in specified directory
M42 P6 S0.008 ; Led light setting almost OFF
M117 Jantec=done! ; Update the LCD screen with “Jantec=done!”
G1 X5 Y5 ; Move to corner
M140 S{print_bed_temperature} ; Set bed temp
T1 ; Select extruder 1 (or 0 depending on how your printer is set up)
M104 S{print_temperature} ; Set extruder temp
M116; Wait for temperatures
Please donate $1 to my paypal account if you use (parts of) my developed materials so I can continue to share nice stuff for you to download
Above: Our Dual Bear I3 dual color 3d printer with independant carriages, this one does not run octopi and is remotely managed by Duet Web Control (DWC).
Above: The Voron 2.4, dimensions 300x300x220 mm
And the Twotrees Sapphire pro, our perfect printer for fast production, also on octopi.
And the multicolour completely rebuilt Geeetech A30M dual head printer with a new Duet2Wifi motherboard, dual Chimera heatblock and direct drive extruders. This one runs Duet with DWC instead of Octopi.