FREE DOWNLOAD CNC_FLYCDY_controller_box_V15b_20250609
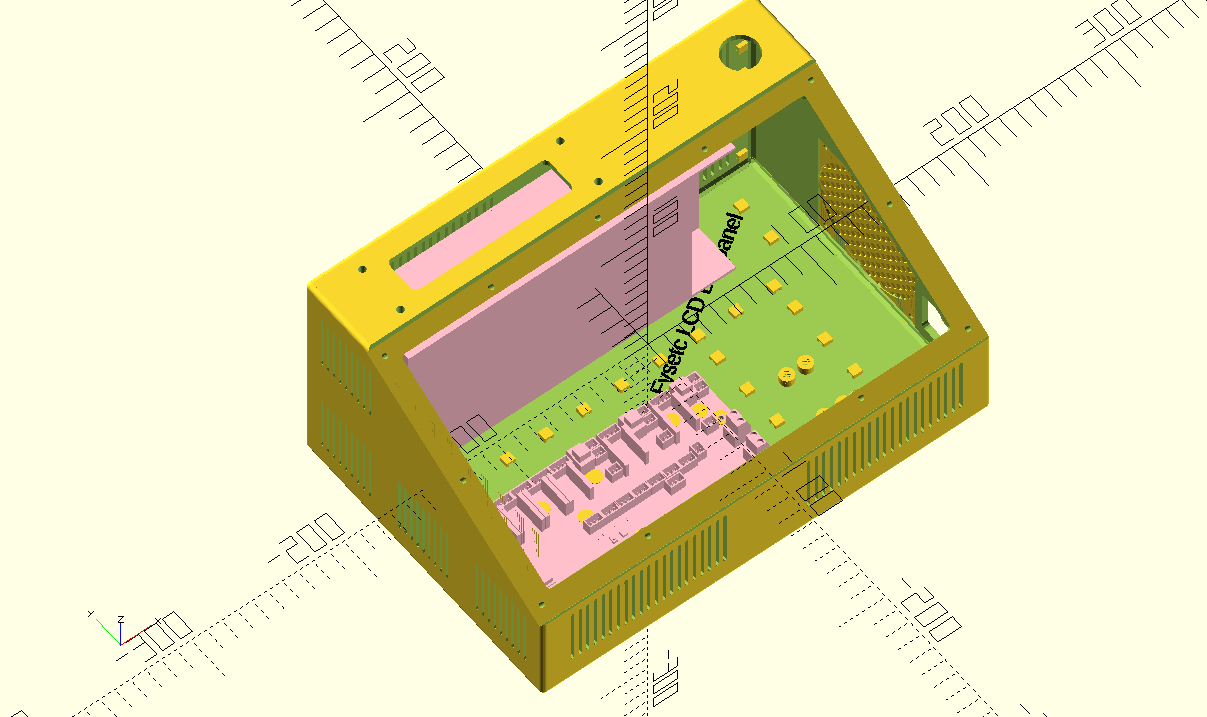
THE CNC CONTROL BOX
Download the CNC controller box design file via the above link in 1 piece which will take around a day or more to print.
The CNC box design is also available in 4 separate design STL parts that interlock very well and will have to be glued together. These STL downloads are available further below.
Please donate $1 to my paypal account if you use (parts of) my original designs so you can enjoy my hobby even more !
The box is also available for DUET3 HERE
THE TILTED TOP PANEL:
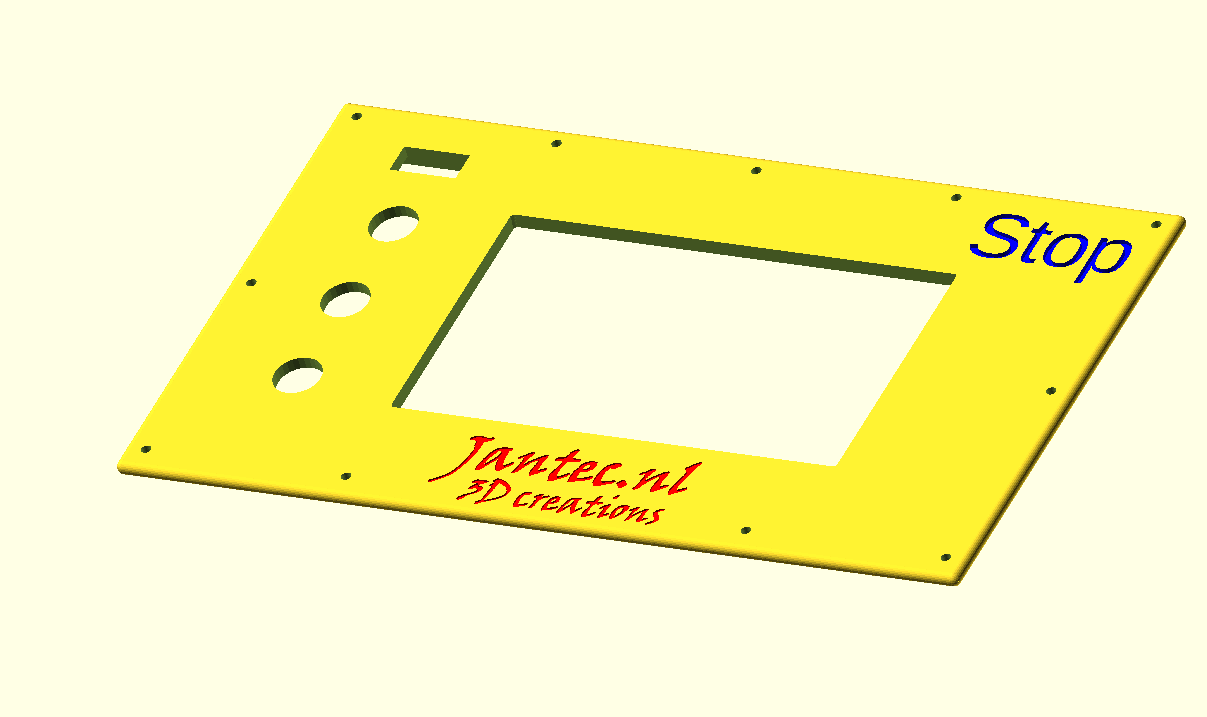

FREE DOWNLOAD_top_panel_V15b_20250609
The tilted top panel is available for downloading just above this text and houses a FysetC Duepanel 7 inch LCD module that interconnects to the FlyCDY2 or 3 ( and also to the Duet3, obviously).
The box and panel also include holes for a 24-pins multiconnector on top, a panic button on top, an 80mm fan unit, a filtered power inlet unit (in my case, for 230V Europe standard) and 3 button holes on the tilted panel, as well as a small hole for a voltage reading unit. Any other required holes can best be done after printing. Just with normal tools, by using painters tape first to cause minimal collateral damage to the case.
All parts that can be screwed on or-in, can utilize M3 threaded inserts at the mounting points inside. The holes are supporting these. This is not done for thePSU (obviously, the M4 mounting bolts run through the case). The fan is mounted with M3 bolts from the outside through the case and secured with nuts against the fan’s body.
CNC CONTROL BOX DESIGN, PRINTABLE IN 4 INTERLOCKING PARTS:
Please donate $1 to my paypal account if you use (parts of) my original designs so you can enjoy my hobby even more !
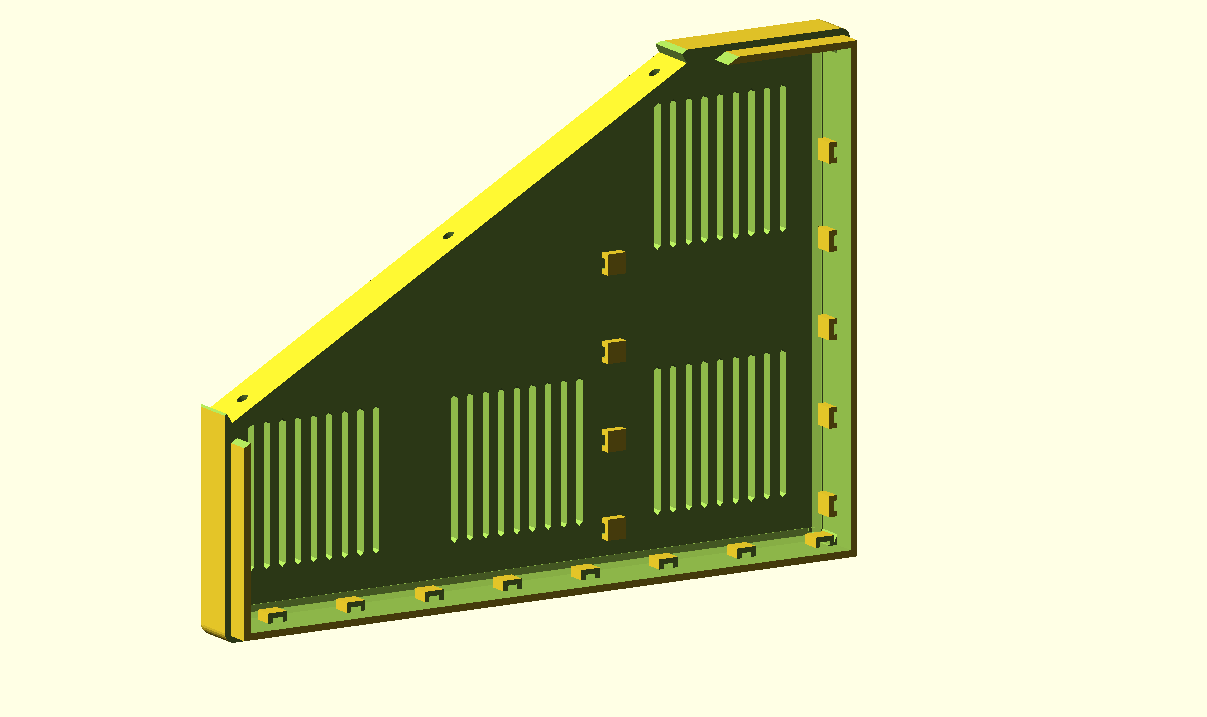
FREE DOWNLOAD CNC_FLYCDY_controller_box_left_part_V15b_20250609
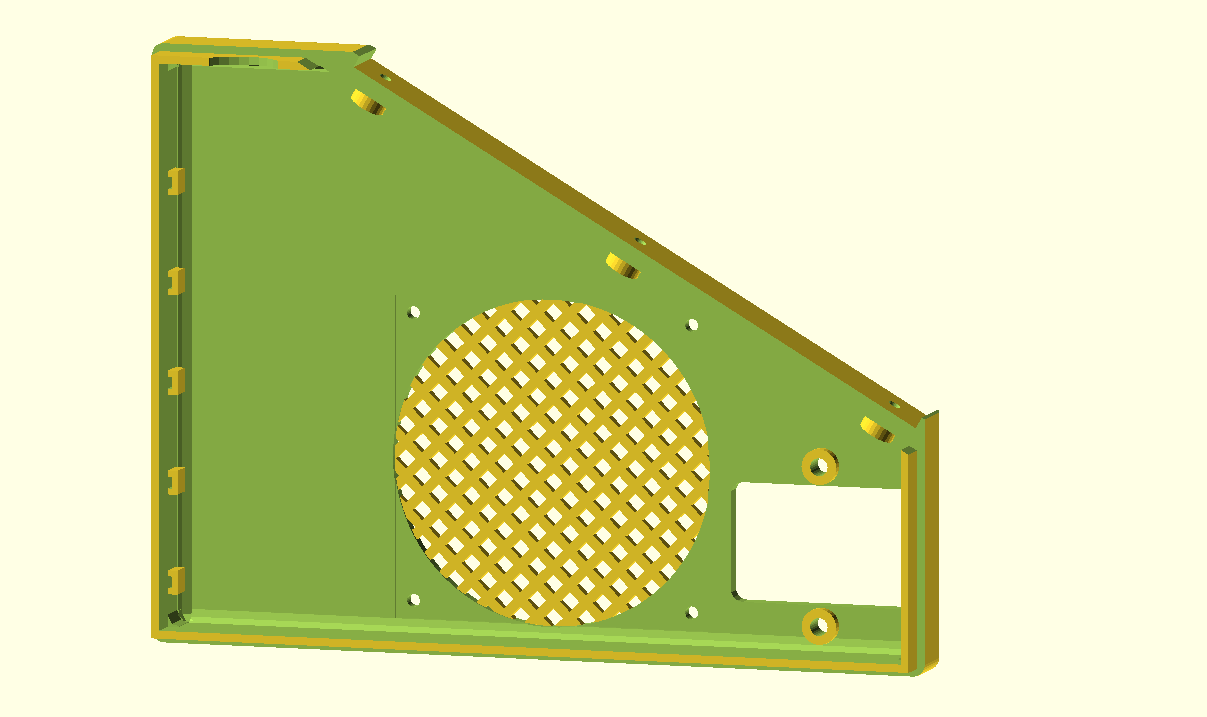
FREE DOWNLOAD CNC_FLYCDY_controller_box_right_part_V15b_20250609
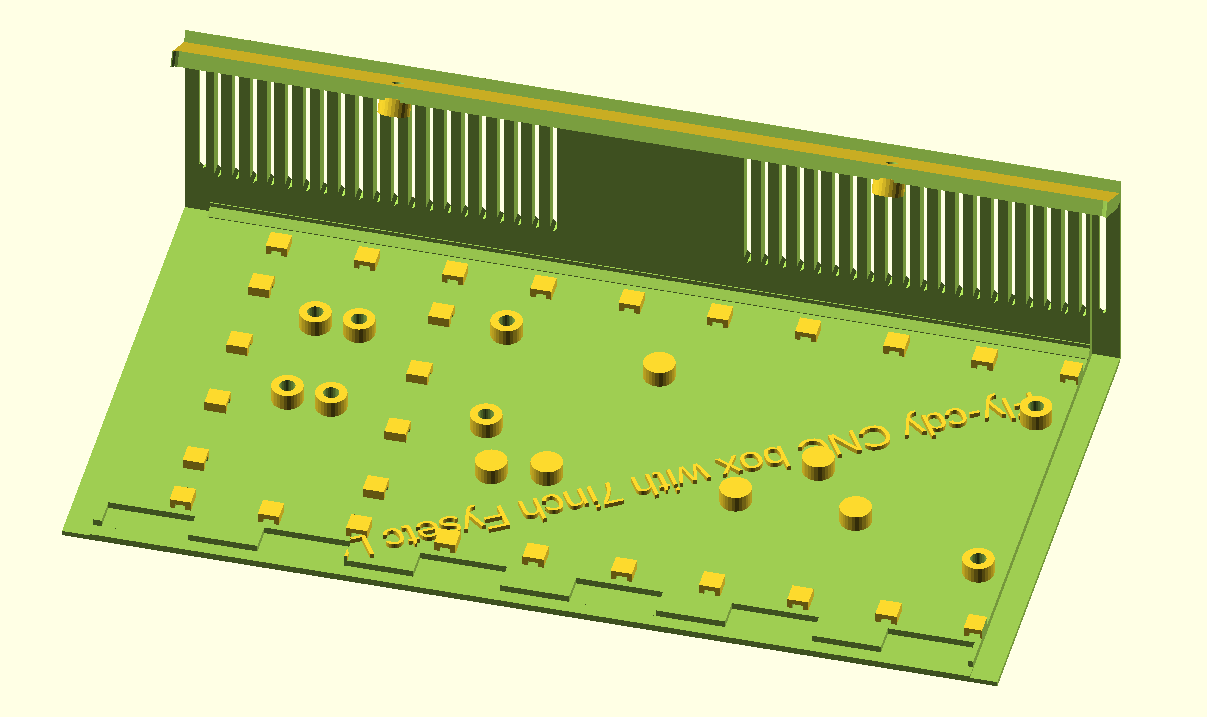
FREE DOWNLOAD CNC_FLYCDY_controller_box_bottom_and_front_V15b_20250609
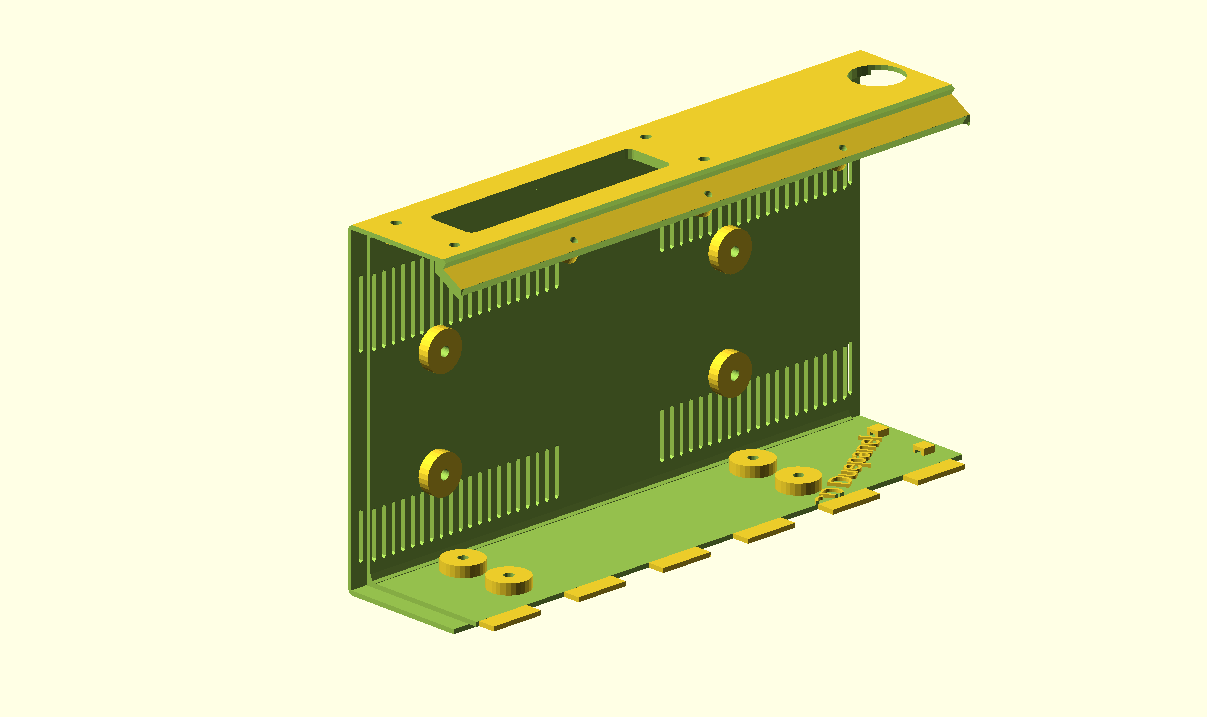
FREE DOWNLOAD CNC_FLYCDY_controller_box_rear_and_top_V15b_20250609
HOW TO PRINT
I always print tools and toolcases in ABS at 260-270 degrees and 40% infill. The front is printed with 100% infill. Use minimal support for these parts but always use maximal adhesion!
Also, set Cura to a shrinkage correction of 100.7%, due to ABS black shrinkage of 2.2 mm on the long side of the box. (The xSize should be 295 and this was measured 292.9 after being printed as full box)
For constructing the box from 4 individually printed parts, first connect the bottom parts without glue. Then, attach both the sides and screw in the front panel. Then, where needed file or sand off ledges so it all fits properly. Then, remount it all and let the glue find its way between the connecting overlapping ledges that connect the parts.
Be aware to print the 2 side parts and the rear part with the rasters down on the printer’s bottom plate.
Print the front part with the bottom down.
All parts will print best with support 85% AND adhesion outside only ON.
Print support with 85% angle support everywhere at 5%, so the M3threaded bussupports will be printed well.
PRINT ORIENTATION EXAMPLE (Cura, VORON 2.4-600)
Please be aware that the 4-part design is developed with printing in mind, so the horizontal printing orientation as shown above is the only way to avoid overhangs in the interlocking ledges. This also goes for individual printing of each part.