Conversion of a 1955 Traction Avant 11BN from 3- to 4 gears
-By marrying a 1964 Citroën ID gearbox with a Traction differential-
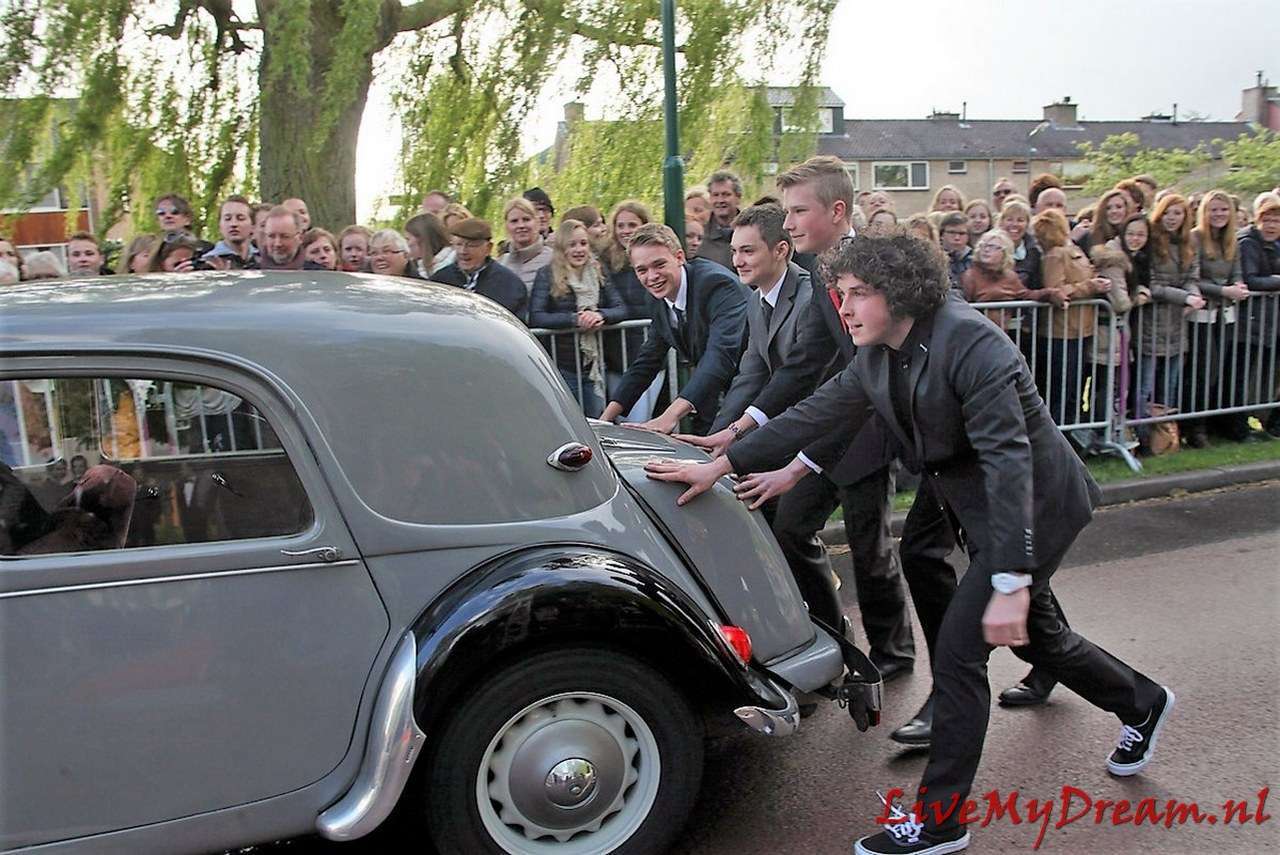
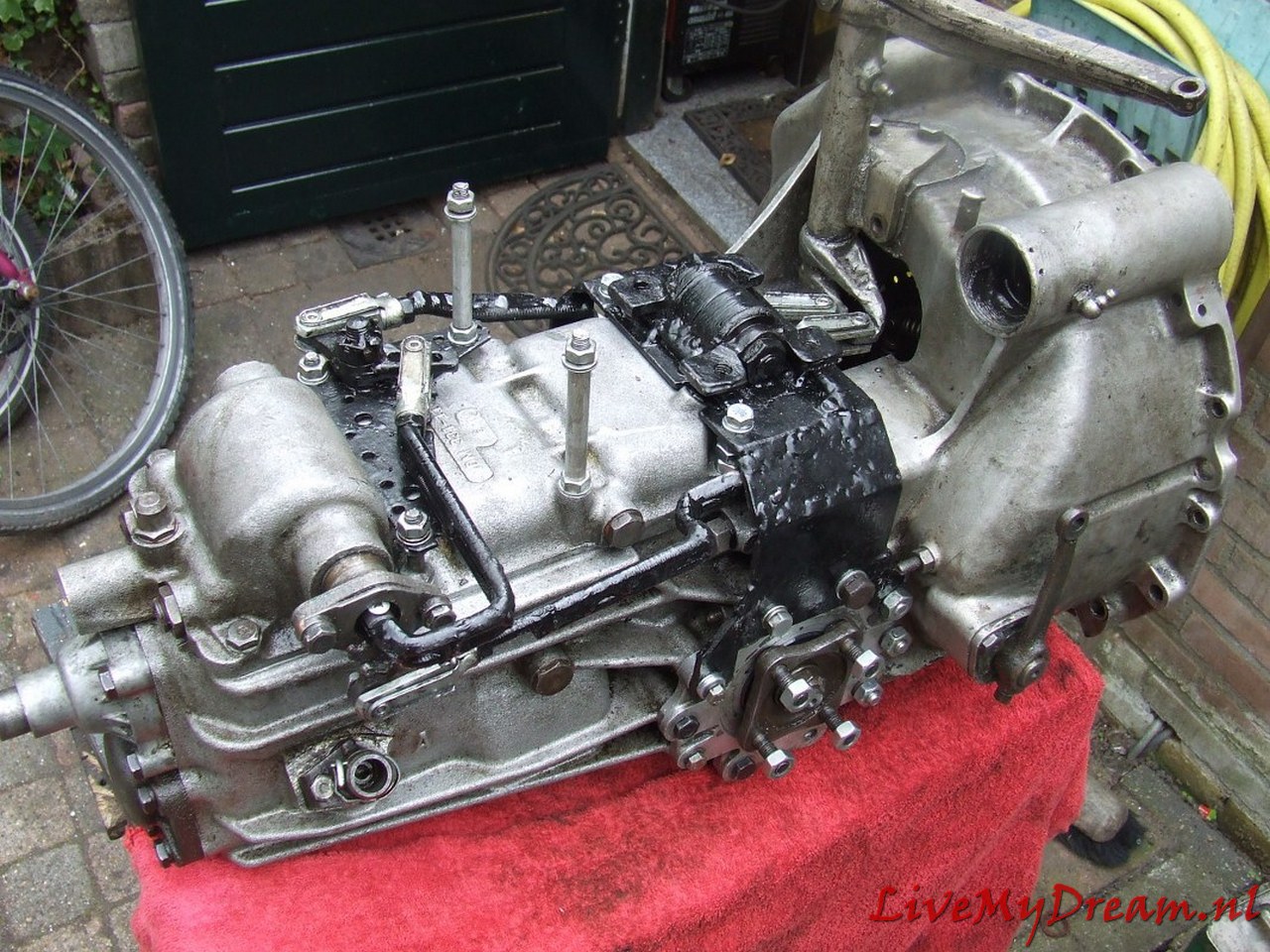
Above you can see the rough end result with which I have now (2022) already been able to travel a few thousand kilometers.
In the end it has been a valuable project.
Driving the TA is perfect, shifting up and down is smooth and the car behaves very well.
An important advantage of the new gearbox is that the engine makes far fewer revolutions when driving at cruising speed.
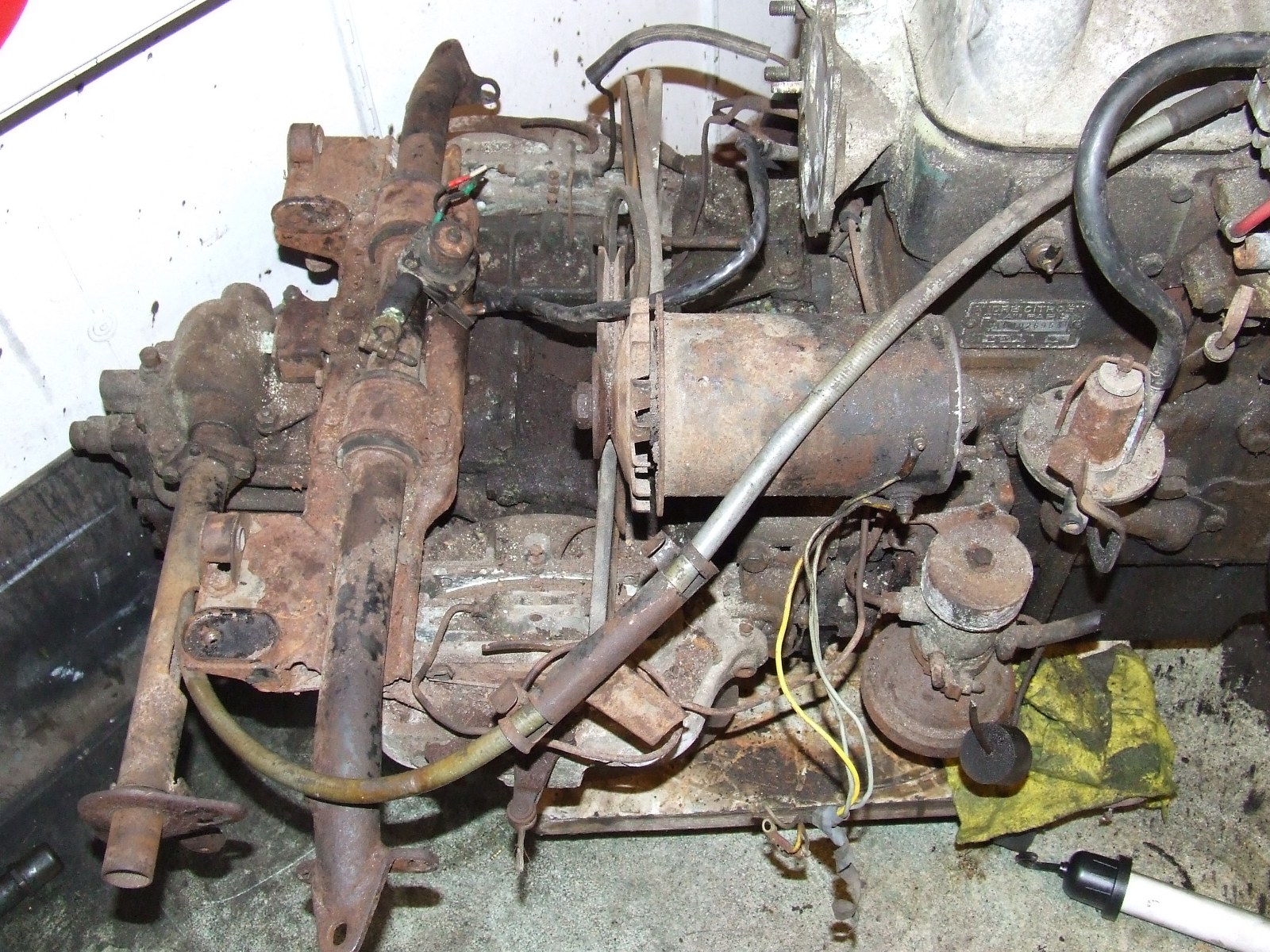
Above you see the overview of the donor long-stroke ID19 engine with the 4-speed gearbox.
At the time of purchase everything was still attached: brakes, suspension, shift sleeve, HD regulator, fuel pump, alternator and so on!
The water pump had already been removed by someone else.
The donor car had serious side damage and was declared total loss.
It was a pity but I was lucky with it.
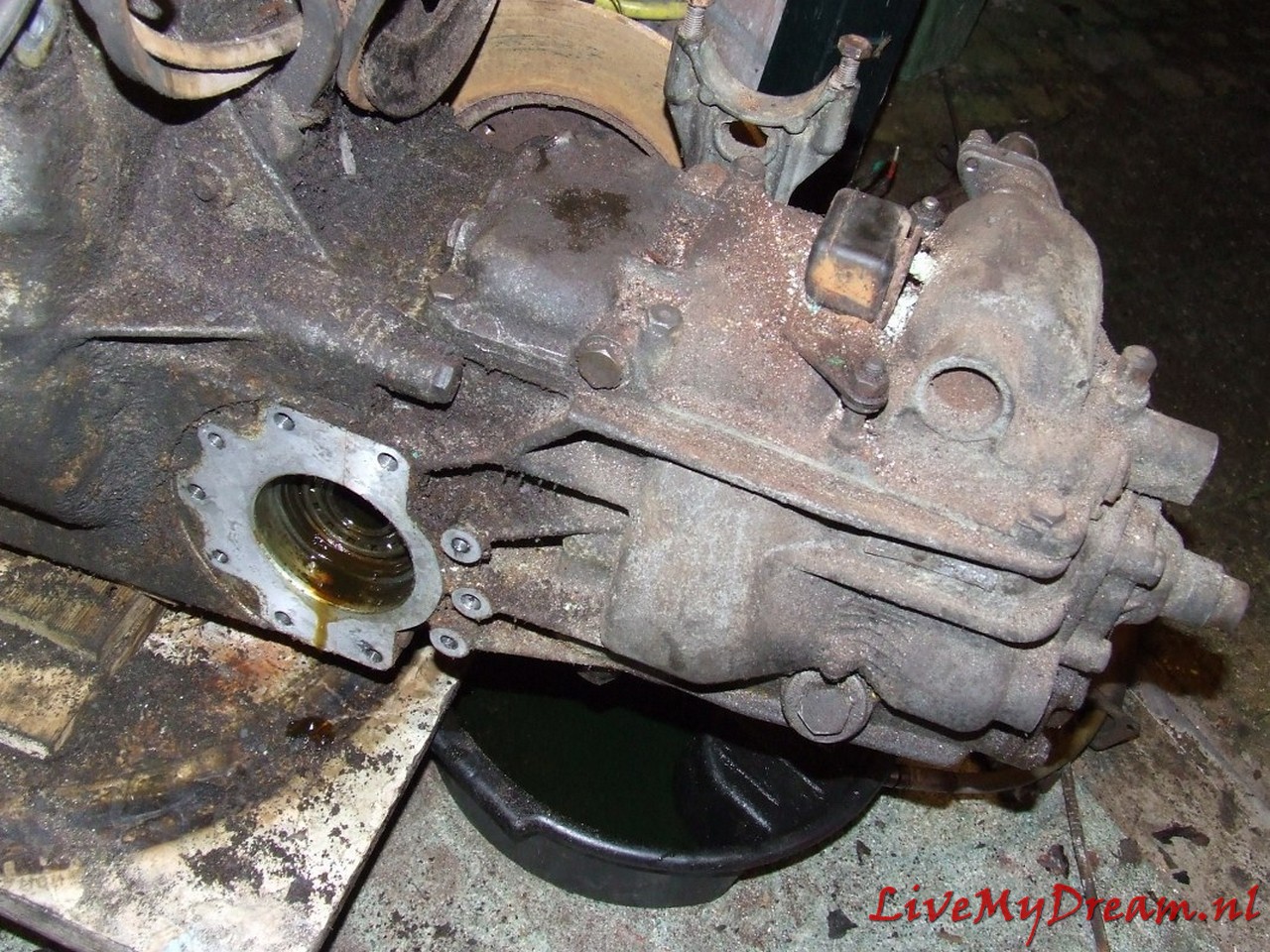
The approach
The long flanges of the 4-speed gearbox have to be turned off on the lathe. From the ends of the flanges (gearbox side), bushings are turned which will sit in the turned off flanges.
This is necessary because the bearings and seals are not available in outside sizes that will fit into the inside of the shortened flanges without fail.
New bearings and new oil seals will be enclosed in the bushings in the turned-down flanges.
The shaft chucks will be turned down by about 1mm to a commercially available inner size for a bearing and seal. (35mm axle thickness)
The flanges are turned out by 3mm to allow the axle jaws to mount properly on the TA internal body shafts.
A stainless steel bushing is turned to allow the outgoing internal TA shaft to rotate tightly in the ID crown gear.
In other conversions, this bushing is usually not installed, but the lateral pressure on the end of this shaft without a fitting bushing becomes, in my opinion, too great to be able to drive it very long without wear.
The bushing has an oil groove on the rotating inner side.
This bushing is needed on 1 side of the donor ID crown wheel and is tightly crimped into the crown wheel.
The ID shaft rotates tightly in the ID crown wheel and is slightly thicker than the TA shaft.
The difference in thickness is corrected by the stainless steel fitting bushing.
The satellite wheels, internal bucket axles and differential housing of the TA are reused.
The satellite wheel (which of course fits the pignon gear of the ID box) comes from the donor ID box. Of course, after the conversion you have to determine the preload on the Timken bearings again and make new spacer rings to fit the whole with the correct preload in the ‘clock’ properly.
Measure the play of the crown wheel according to the workshop manual, and so on.
This solution is robust and will not break or wear excessively.
Controlling the gears was also an important issue for me, because the Traction Avant has a different standard gear change sequence and the known ‘conversions’ to 4-speed all have an extra button or lever to operate the reverse of the gearbox. I chose to convert everything so that a regular H-fork 4-speed + reverse operation is created: · via the TA’s original shift rods – by converting the selector/levier in the cab – by doing a conversion on the gearbox with new shift rods ‘outside out’ from the control levers at the bottom of the shift tower to the original 4-banger controls.
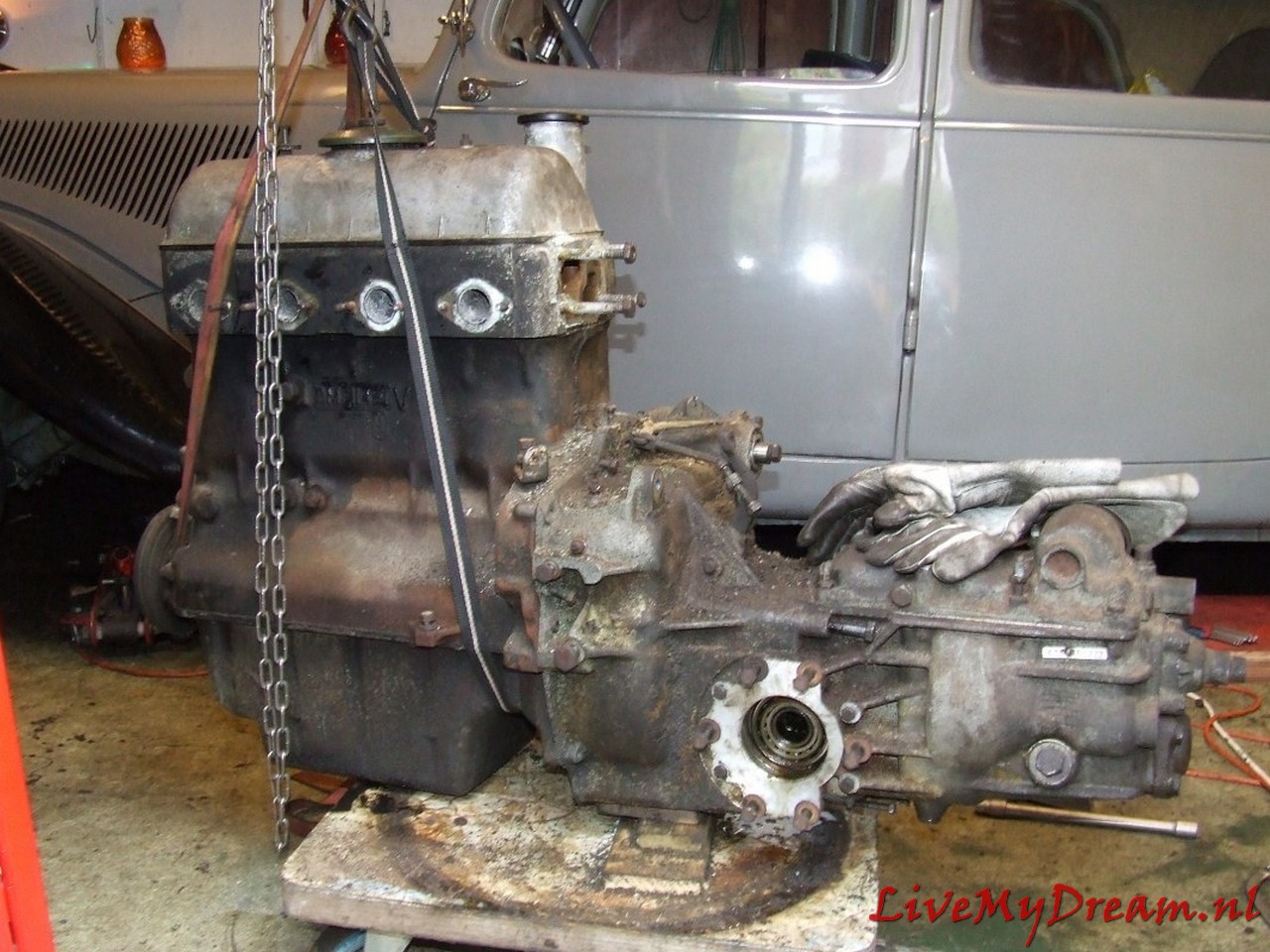
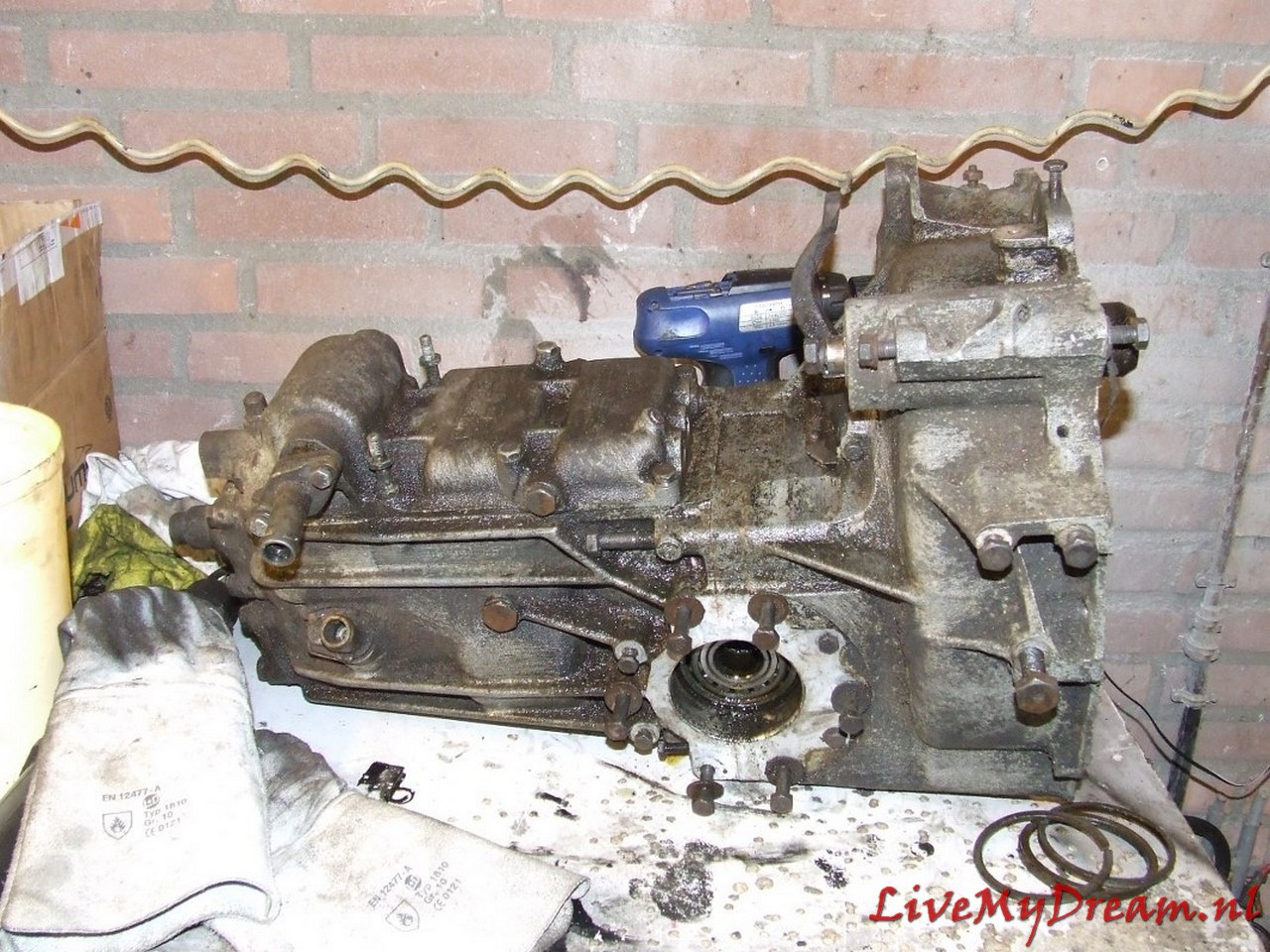
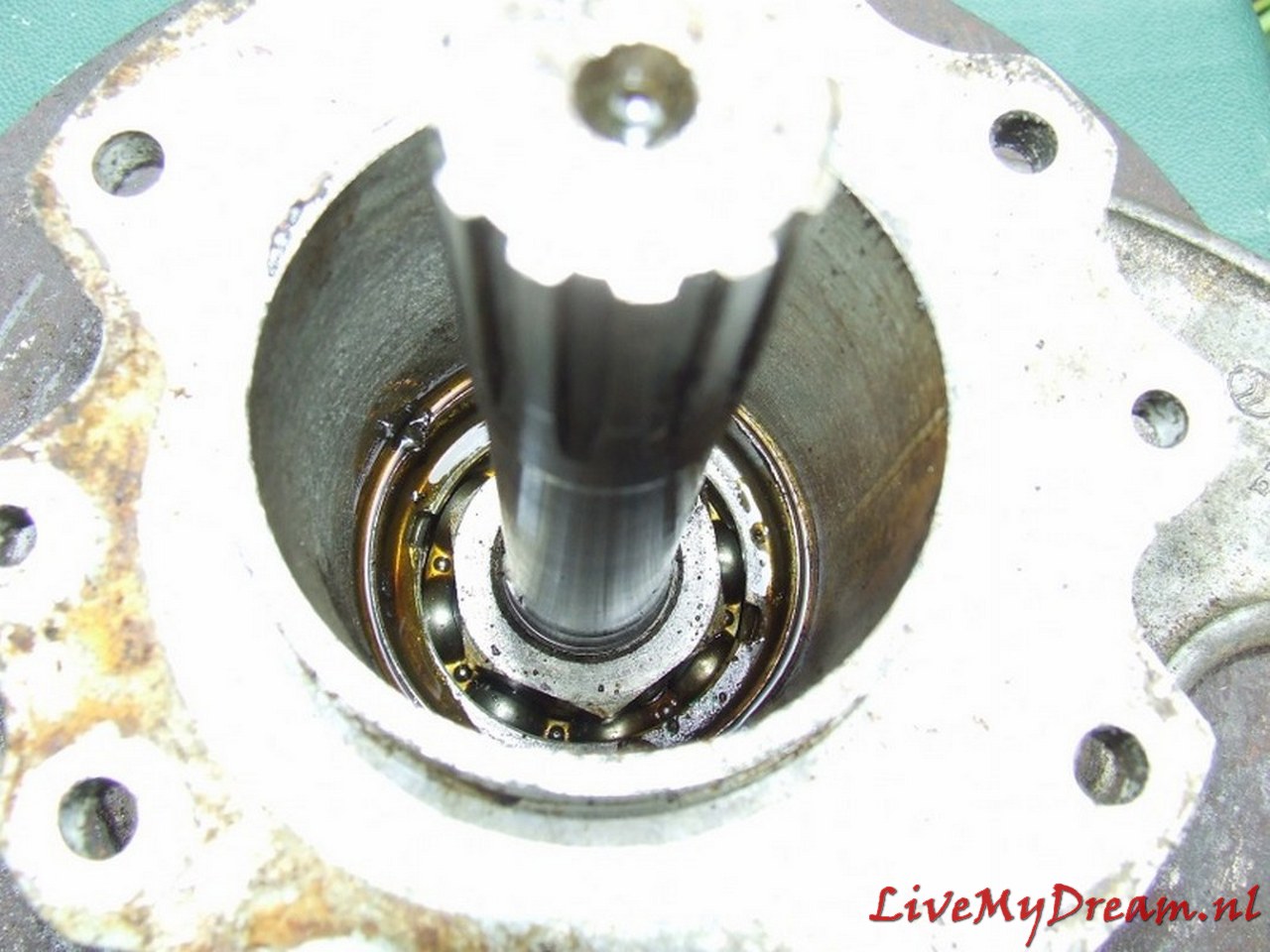
Axles removed and further work on turning the flanges
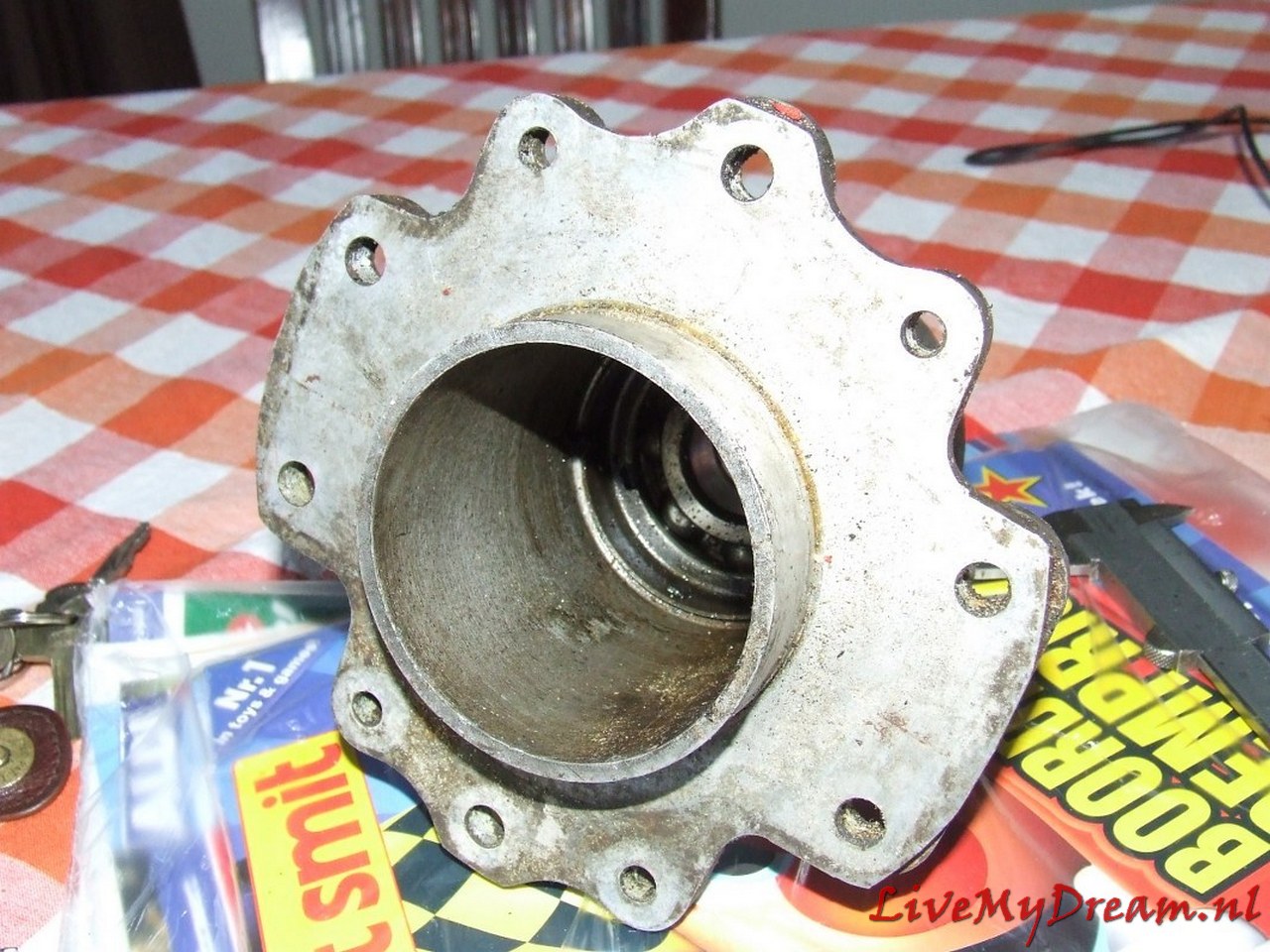
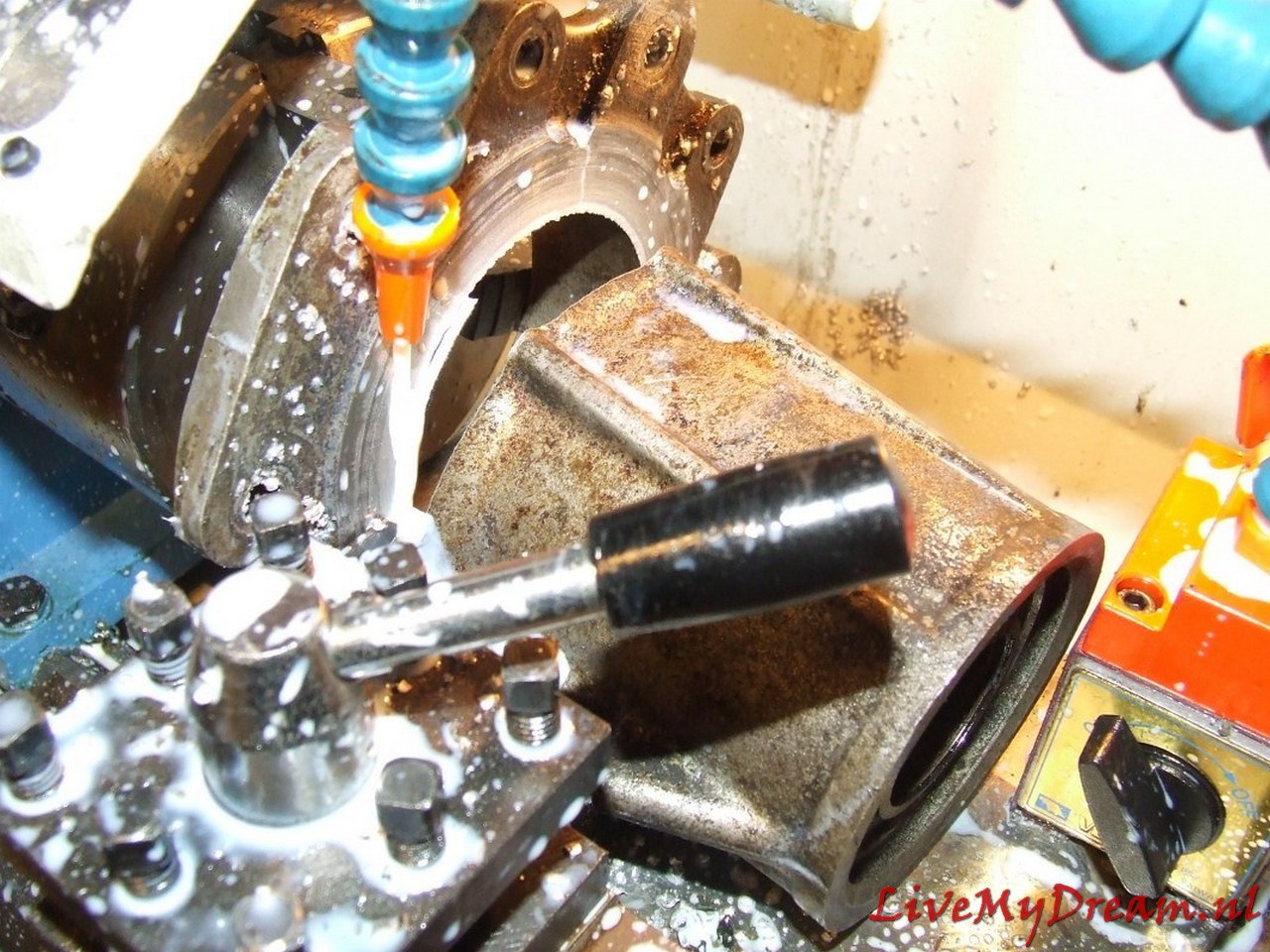
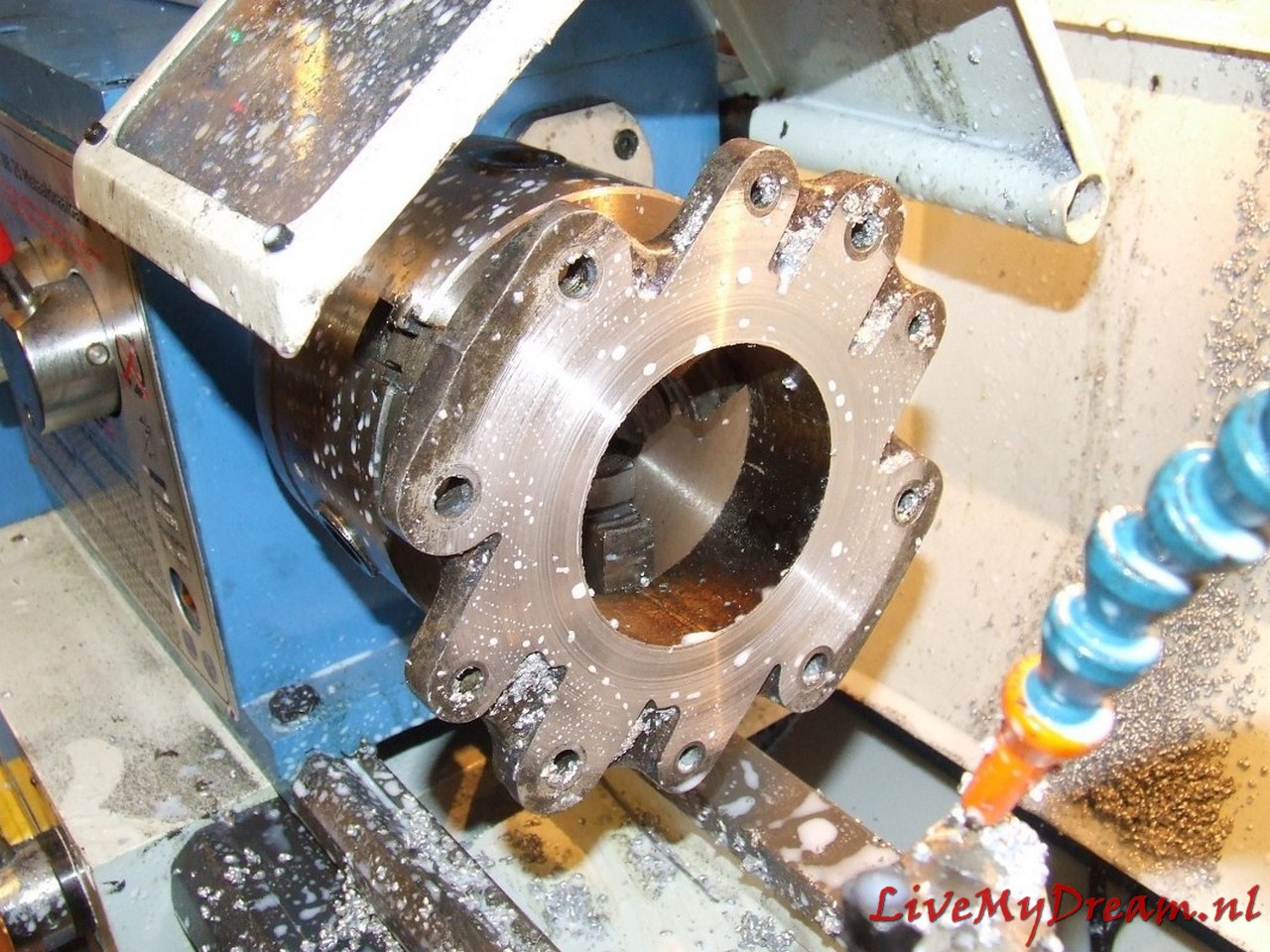
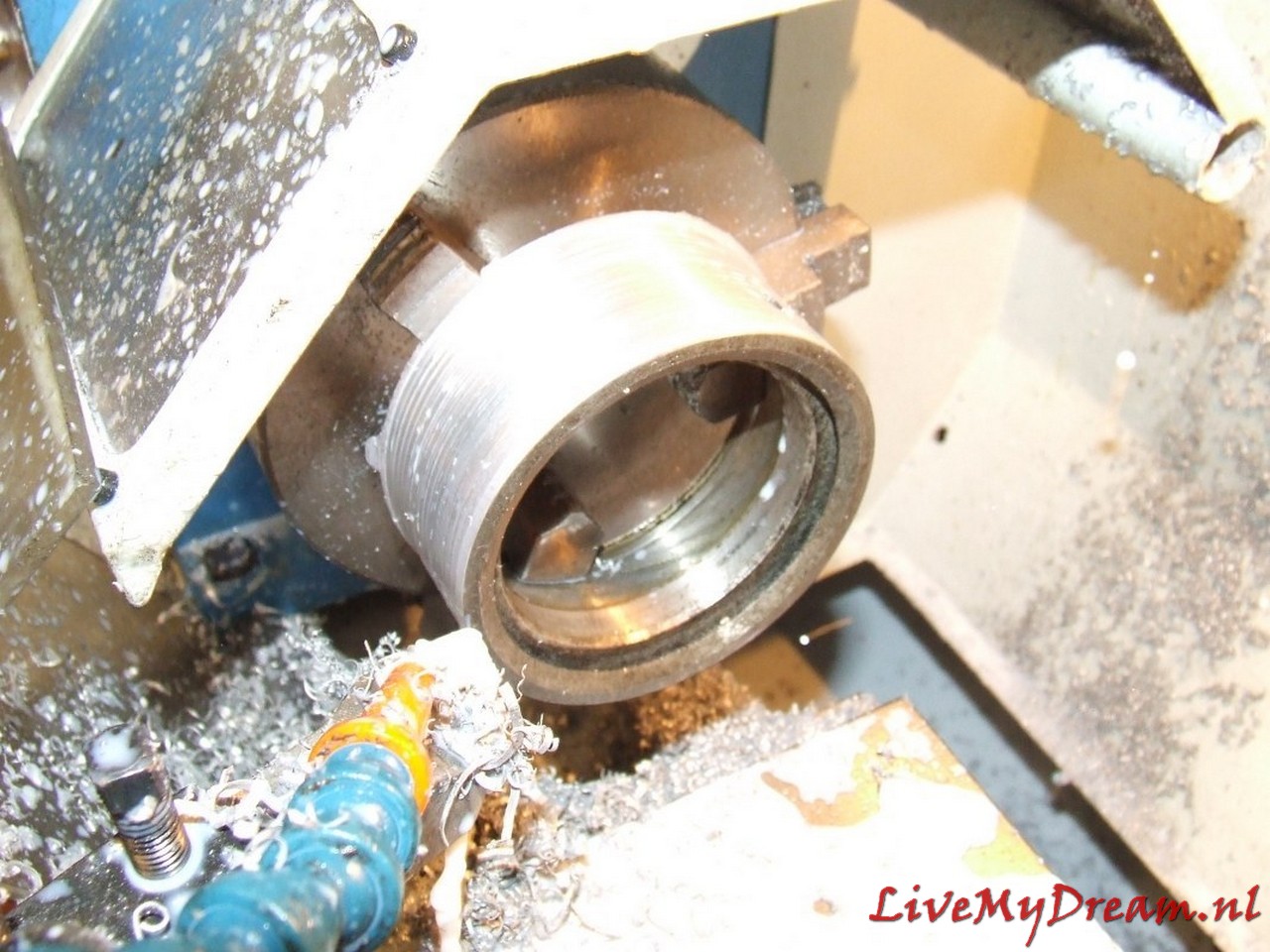
Above is shown how I am turning the bushings for the flanges, here the new bearing and the new oil seal can be mounted.
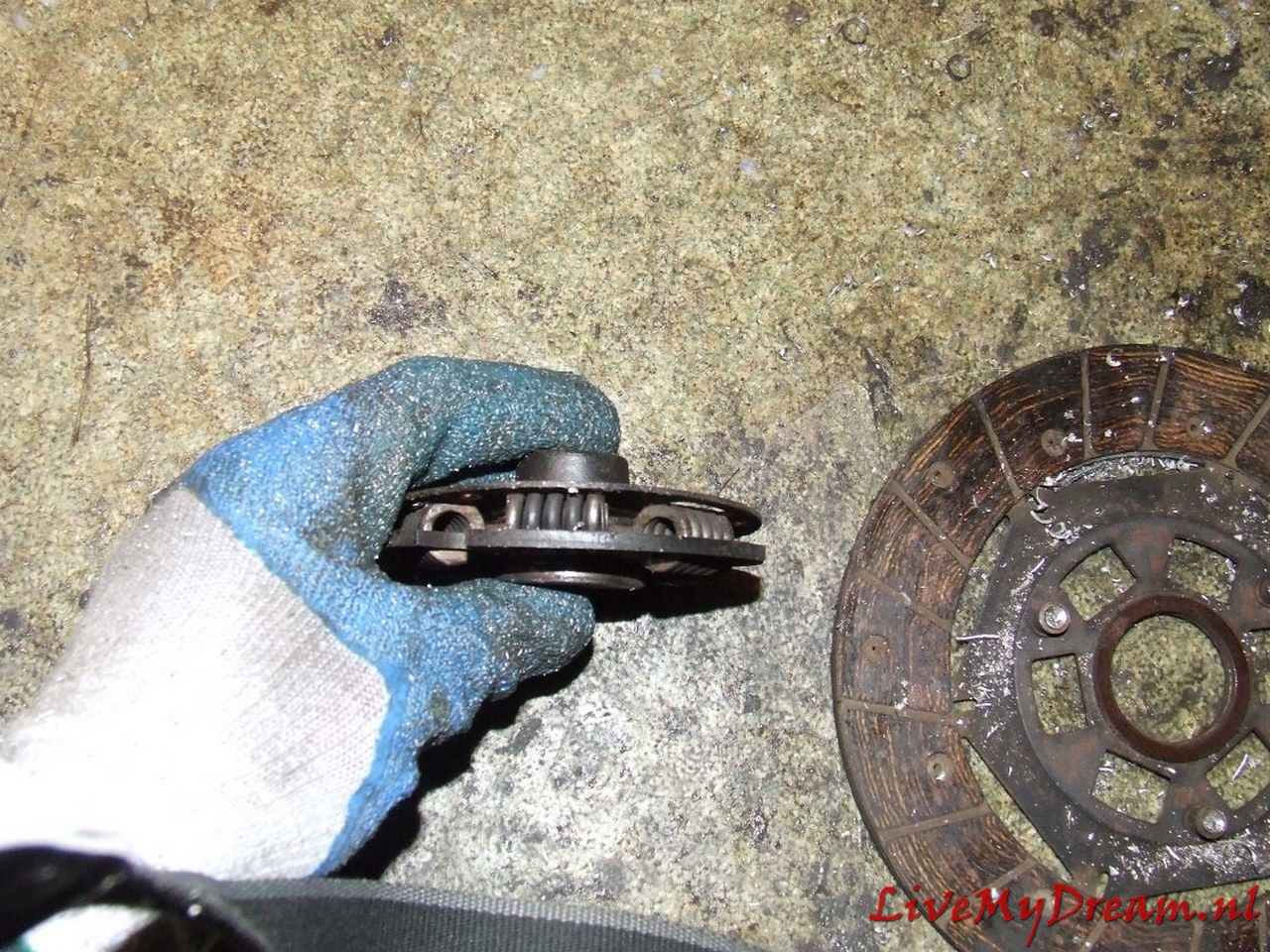
Here the center has been removed from an old ID-19 clutch plate to serve as an extension of another fitting plate.
For convenience I have used a new TA plate for this purpose, an ID plate can in principle also be used but then the keyways must be in perfect alignment so that the plate can continue to slide freely over the primary shaft.
This action is necessary because the primary shaft of the 4-banger is shorter than the shaft of the 3-banger and the keyway of the shaft is just not far enough into the keyway of a standard clutch plate to be able to transfer the force to the plate without damage.
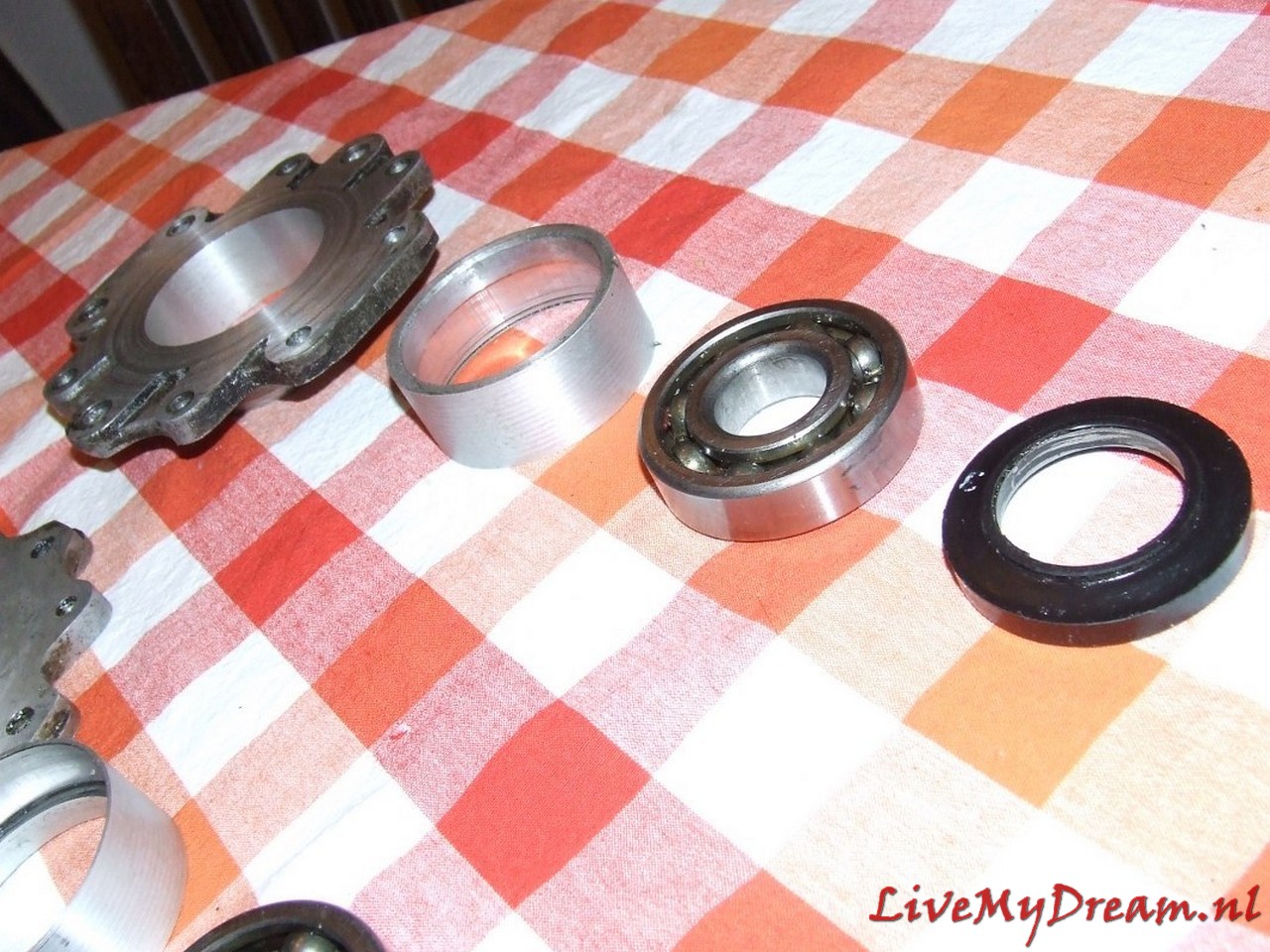
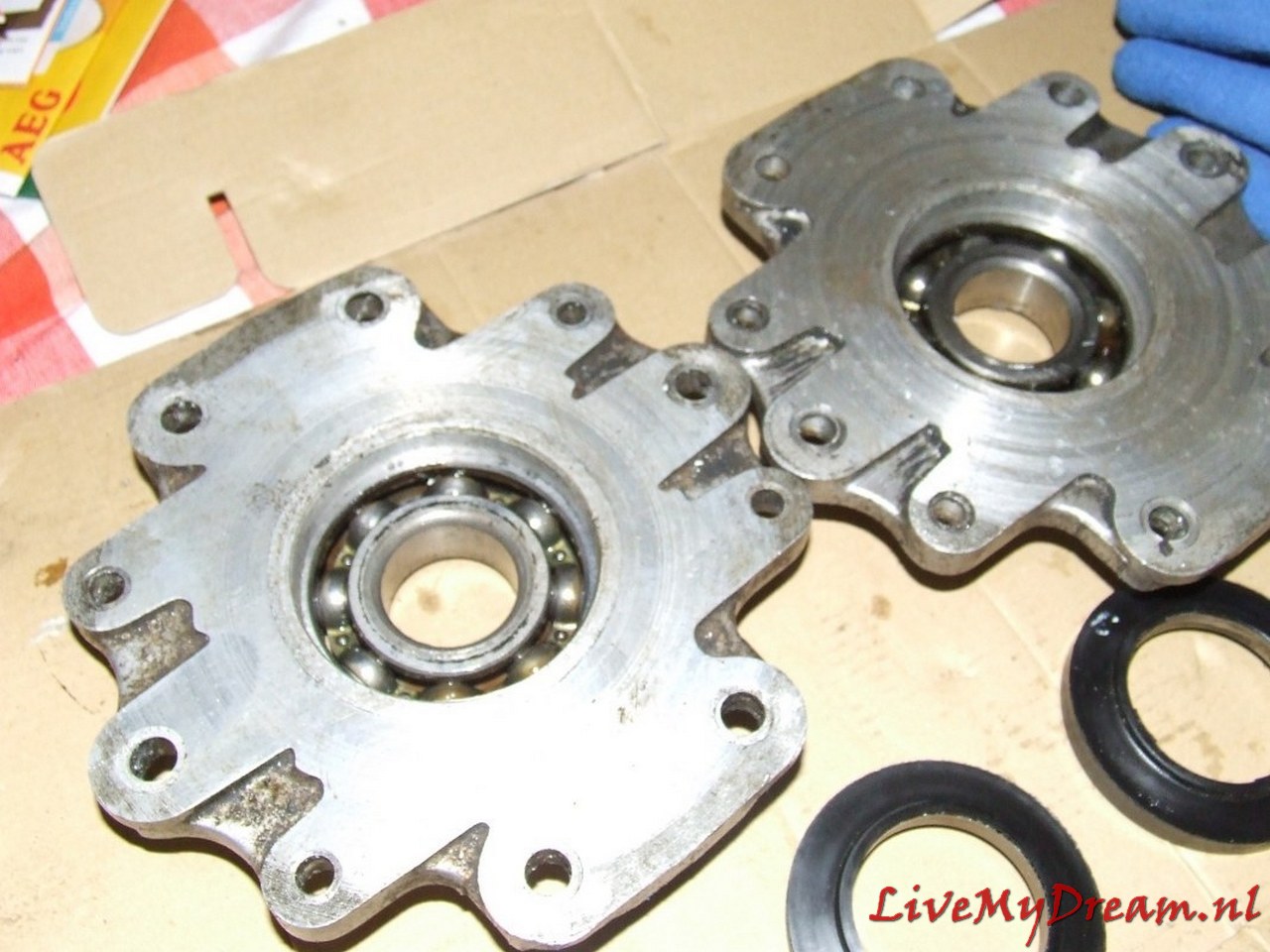
On the picture above you may not be able to see it very well, but the bushings are locked to the flanges with stainless steel screws/rivets so they can’t move or rotate.
Then the flange is turned off at the outside to make room for the convex protruding parts of the 10mm threaded ends of the axle clamps. this also all just fits.
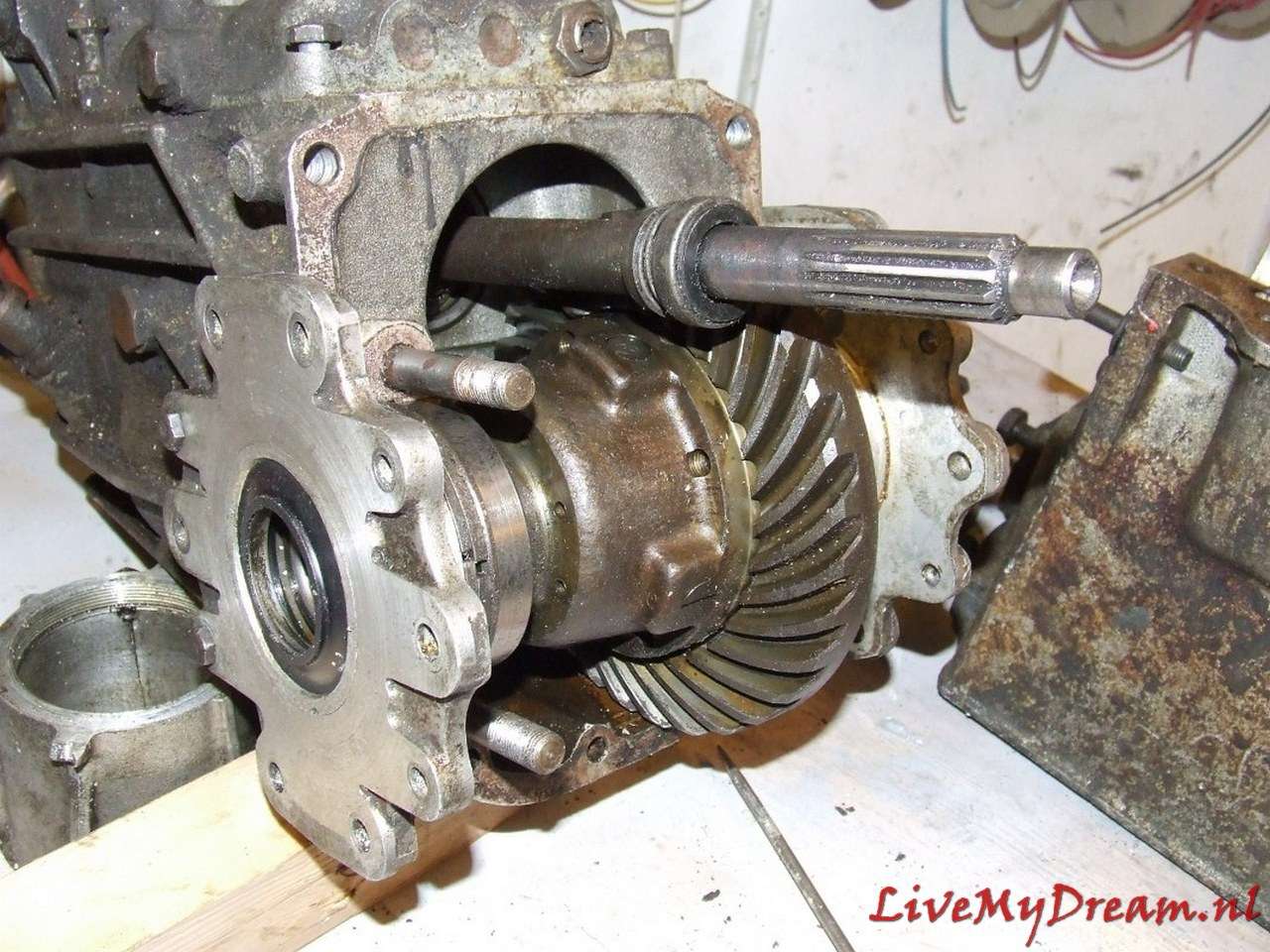
Above you can see that the flange was not yet turned out….
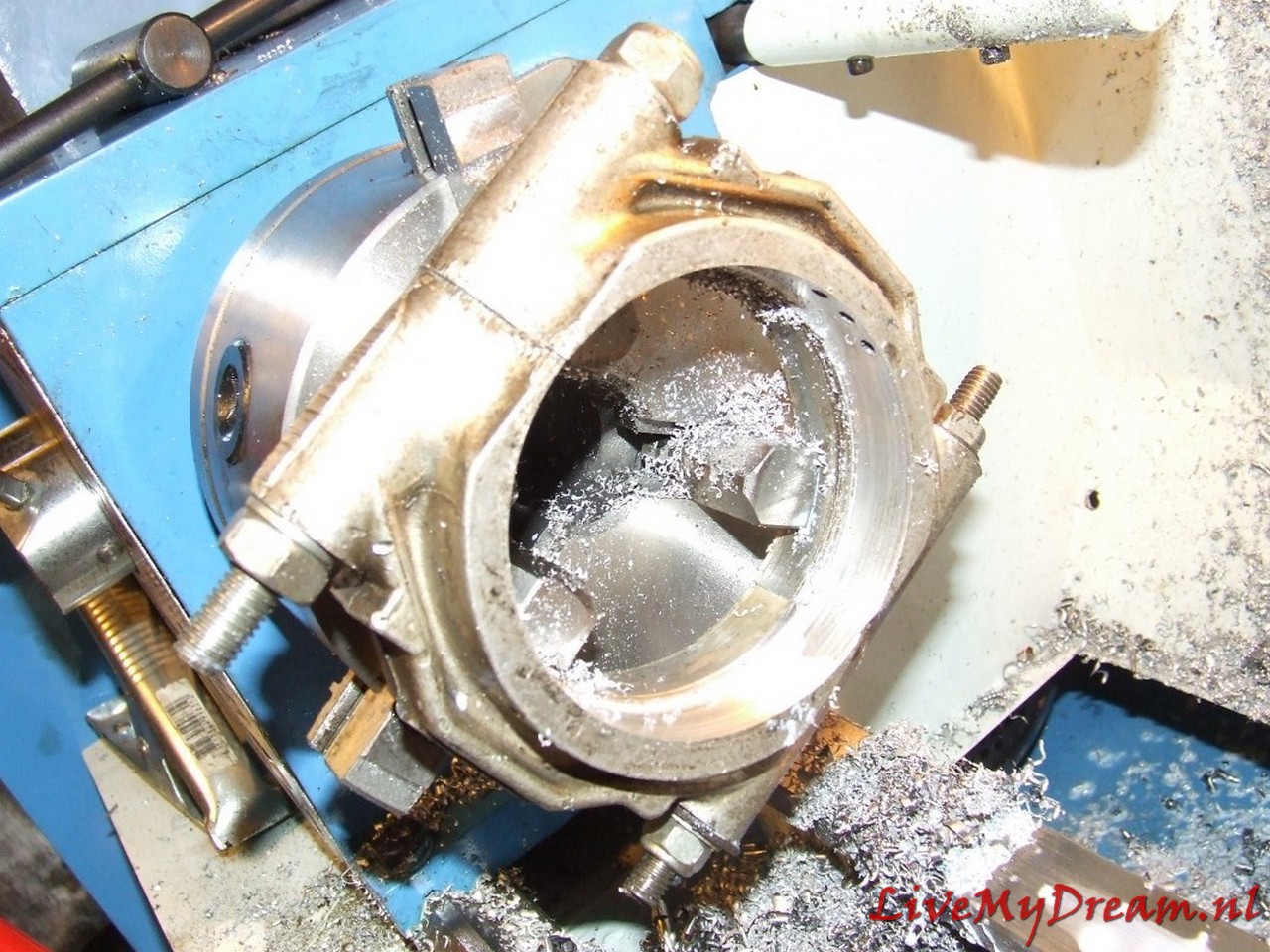
To make the bearing caps fit, they were very carefully turned out to the size of the Timken bearings in counter arrangement in the lathe.
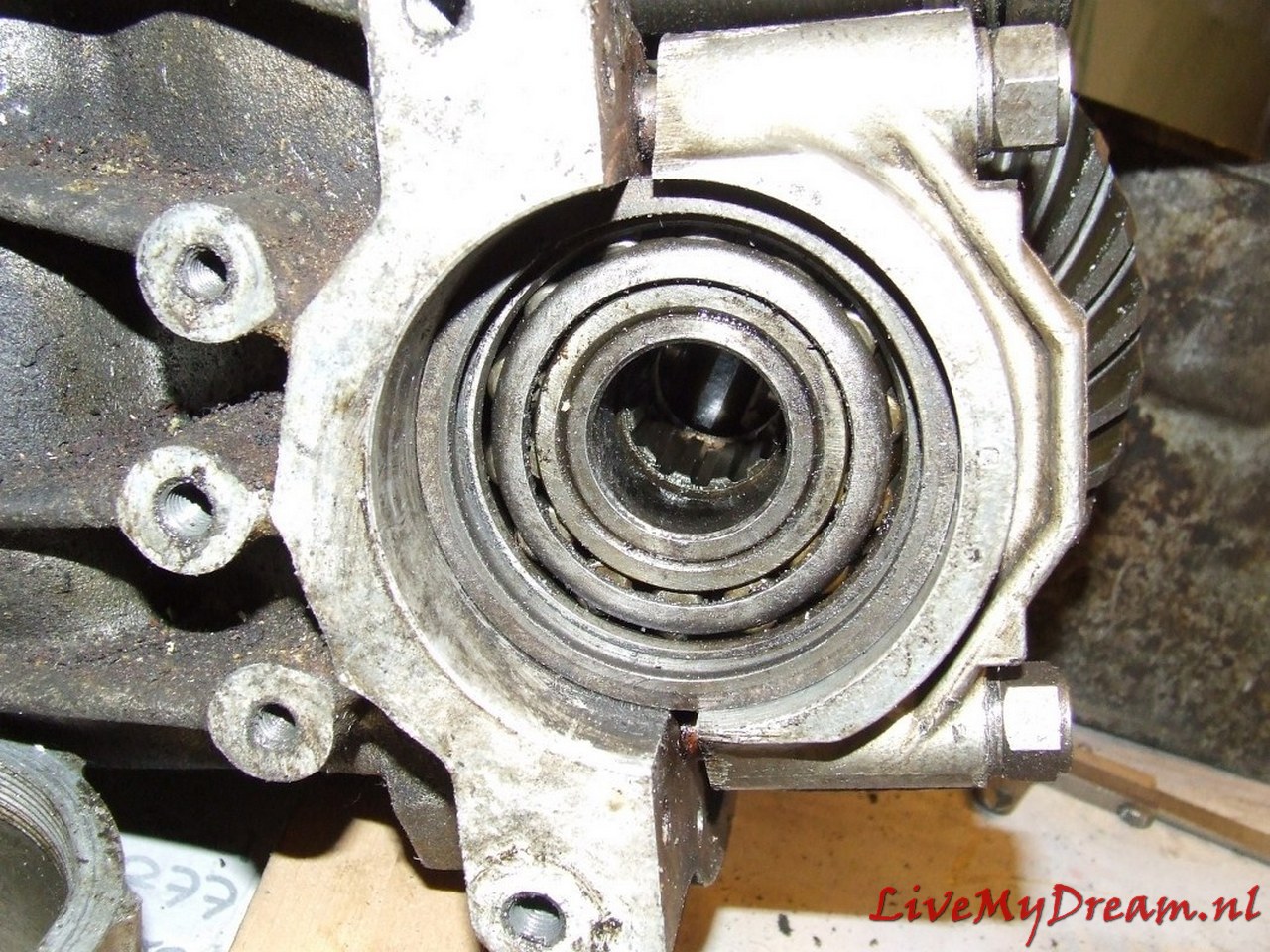
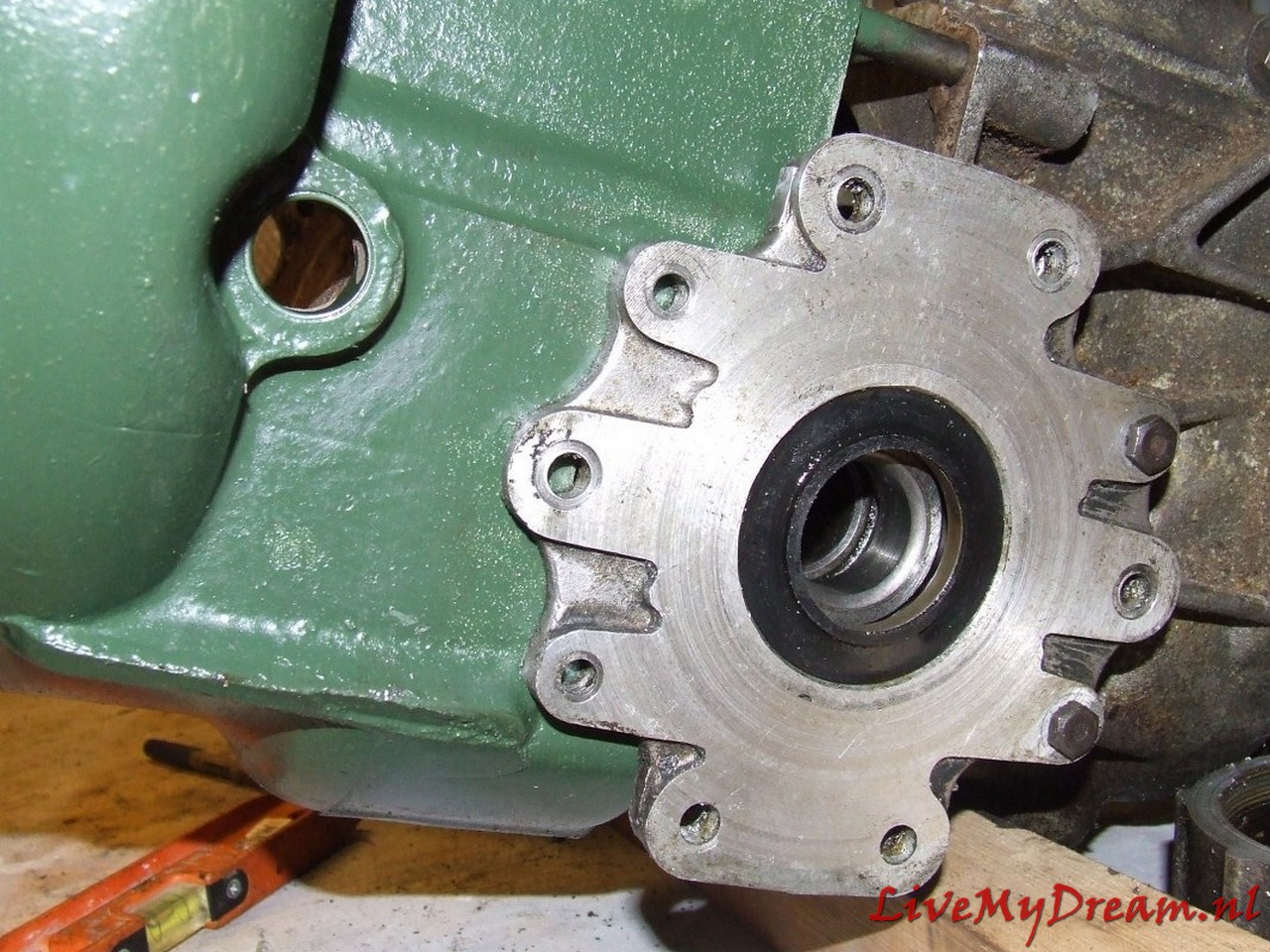
Above you see a turned-off flange with bushing, oil seal and bearing, mounted between gearbox and clutch housing
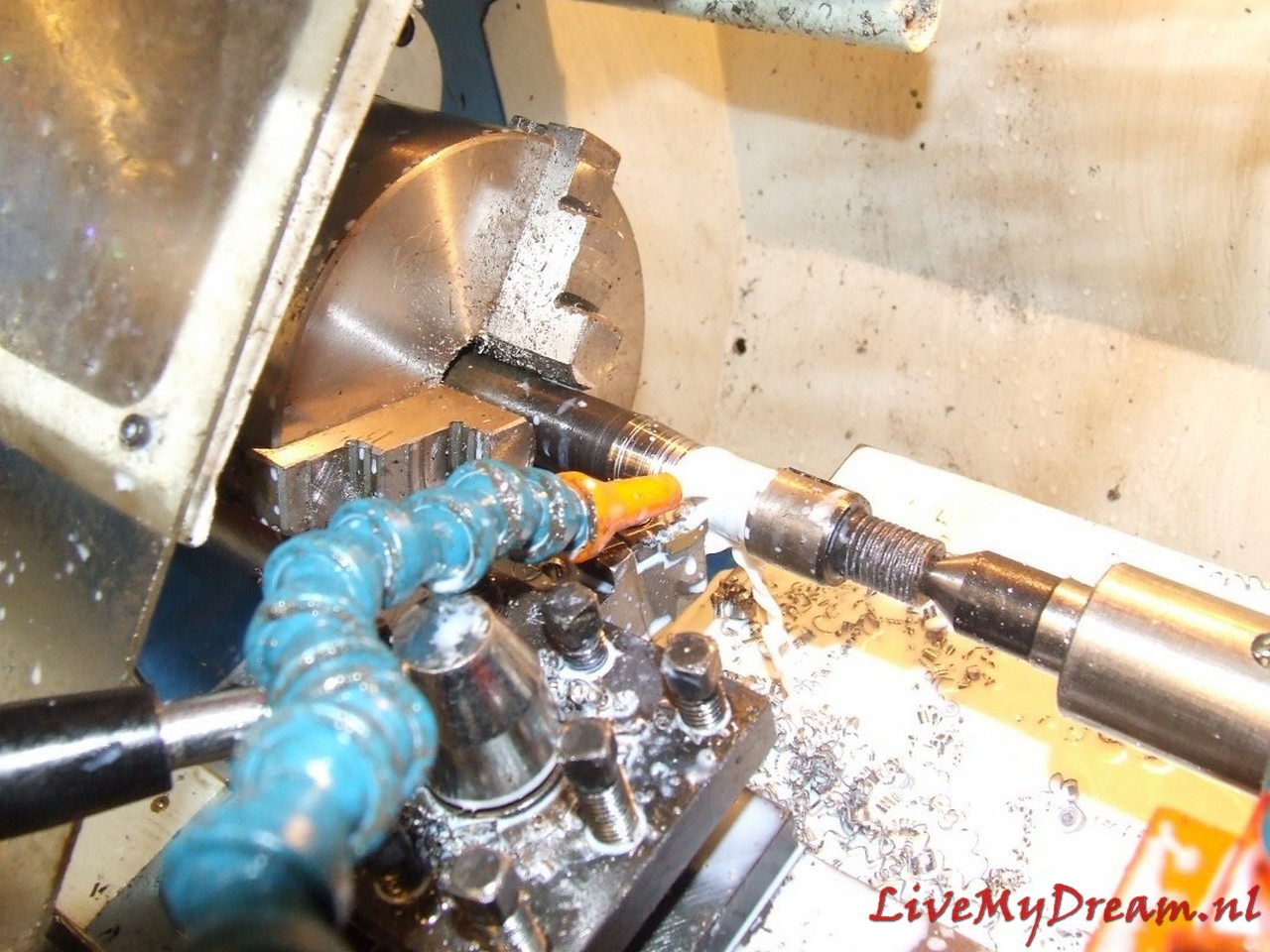
Next job: Extending the drive shaft to the pulley of the ID motor.
The lengthening of this shaft was necessary because I installed a long stroke ID engine at the same time as assembling the 4-speed gearbox.
The drive of this driveshaft on the crankshaft is slightly thicker than on the Traction engine larger and is slightly deeper recessed in the ID engine .
See photo below where the already prepared TA shaft is on top and the ID shaft is lower.
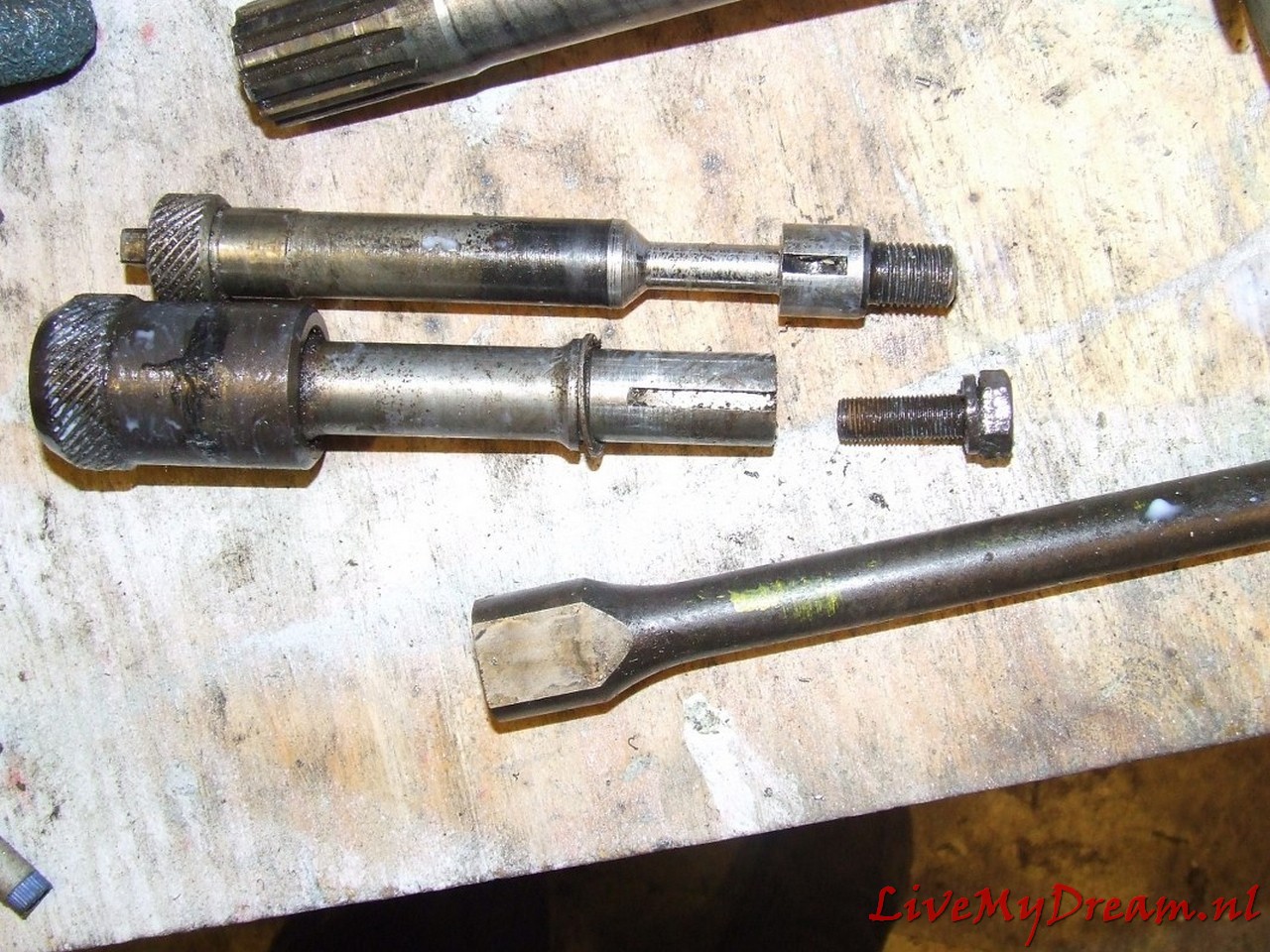
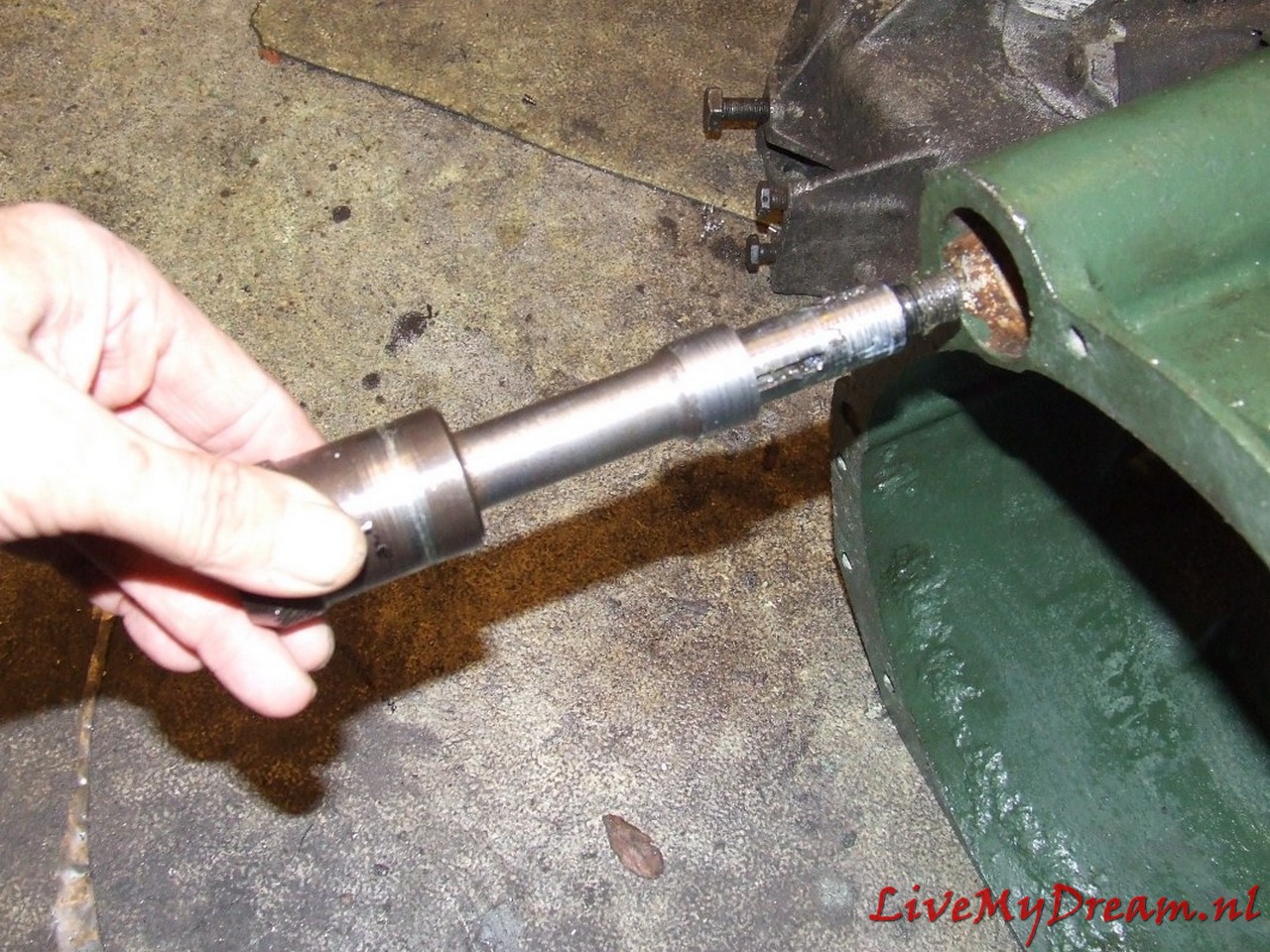
Above: Extended custom pulley shaft ready for assembly
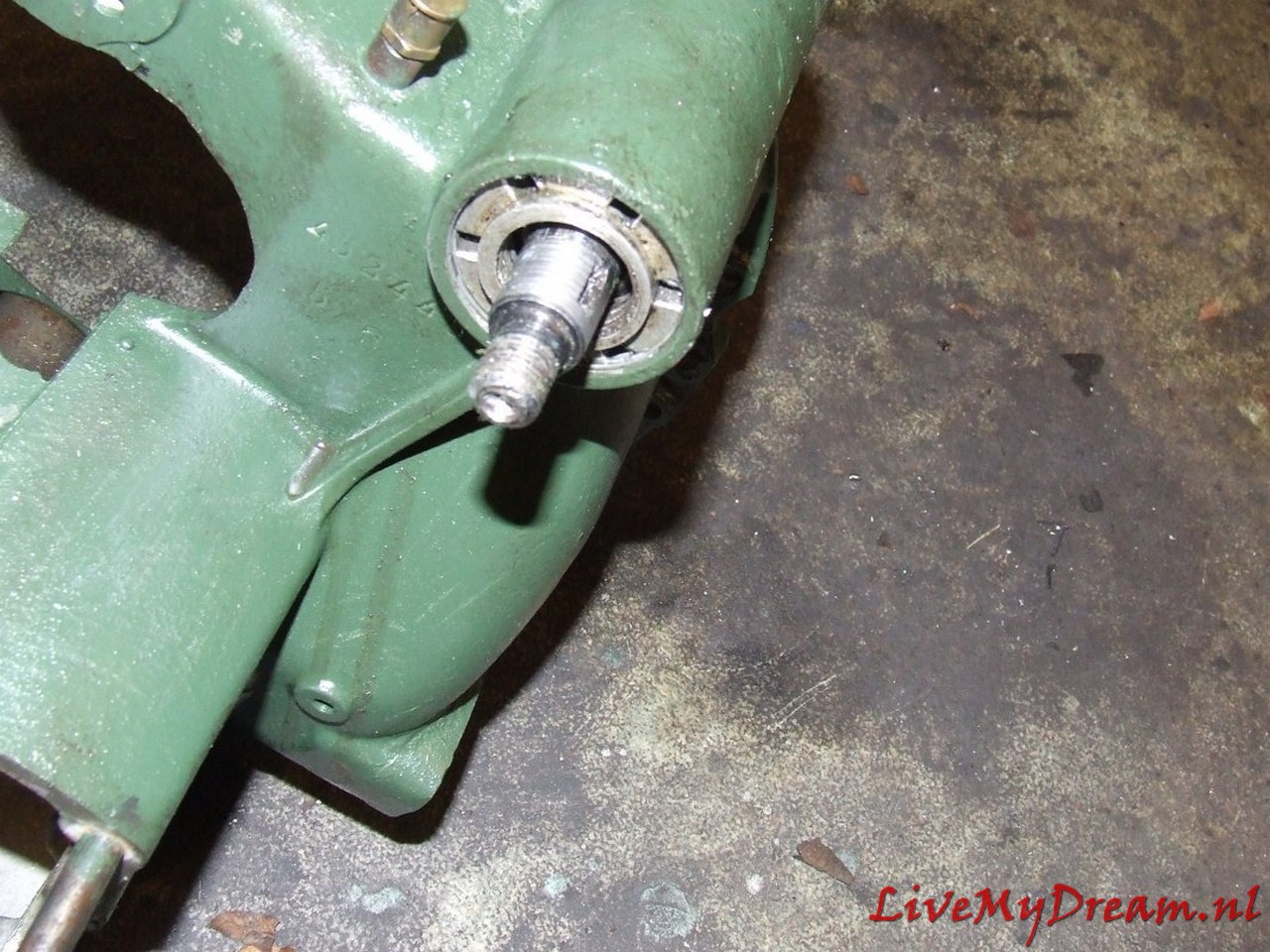
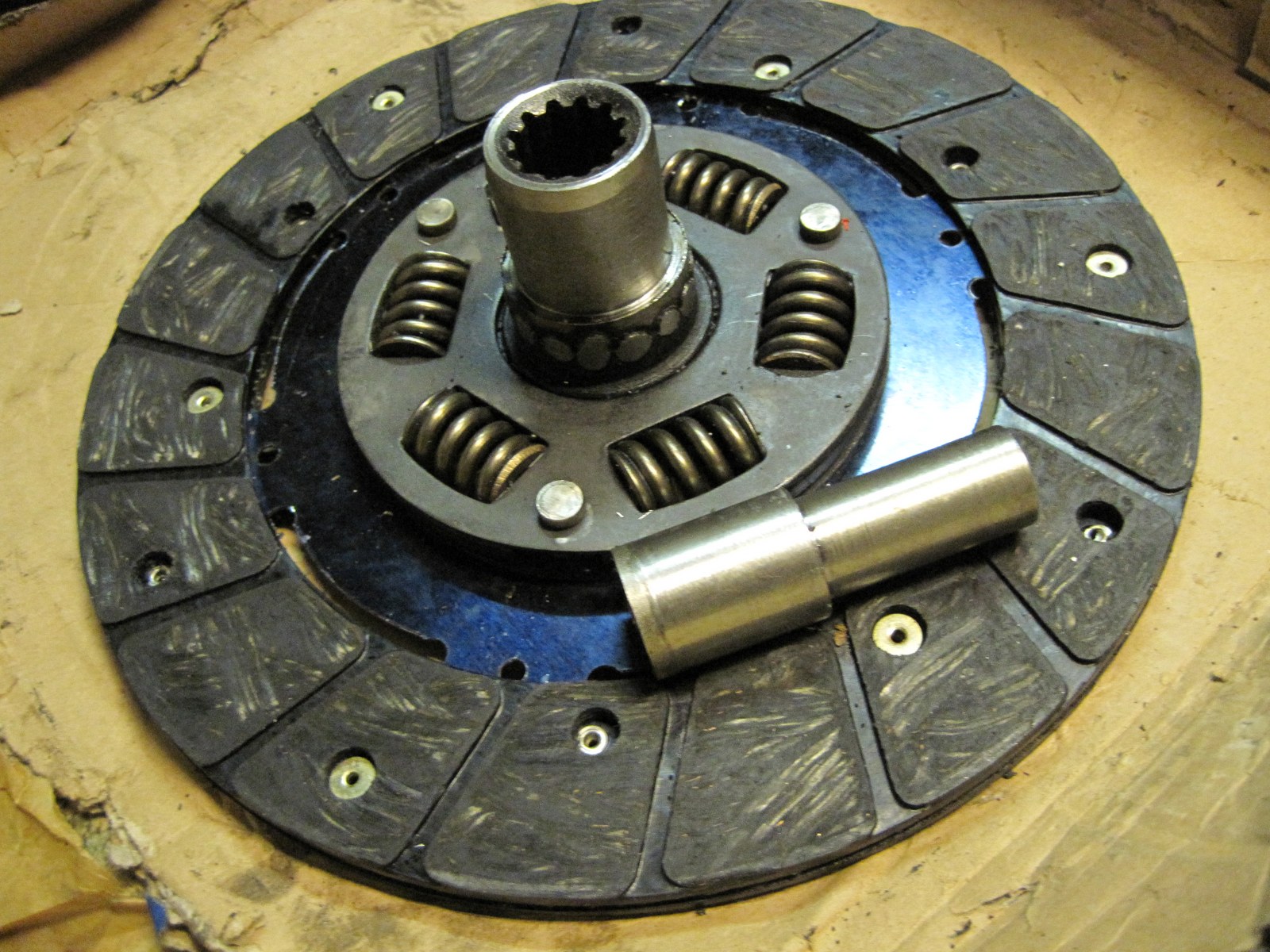
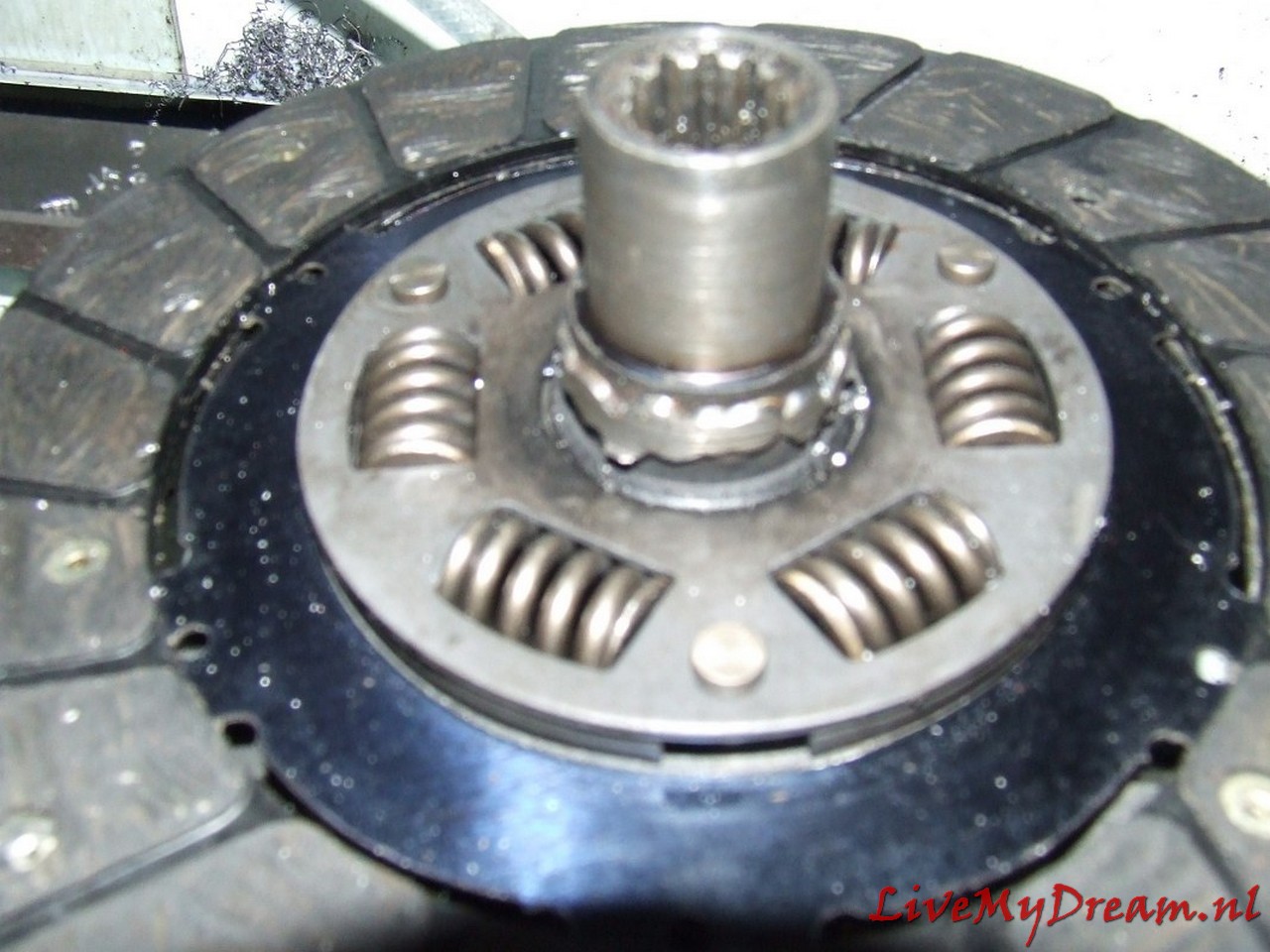
Above you can see the center of the ID clutch pin with ID keyway from a scrapped clutch plate mounted on a new TA clutch plate.
The welding was done with the specially made fitting bushing from ID to TA size tightly pressed into both keyways, this bushing is only removed after letting it cool down completely slowly.
To ensure good adhesion, the welding was first done in CO2 and later grinded out in 3 places, the fitting bushing reinserted and welded again using MIG.
After that I had the welding work checked for swings of the new keyway in relation to the clutch plate.
Fortunately that was well within the norm.
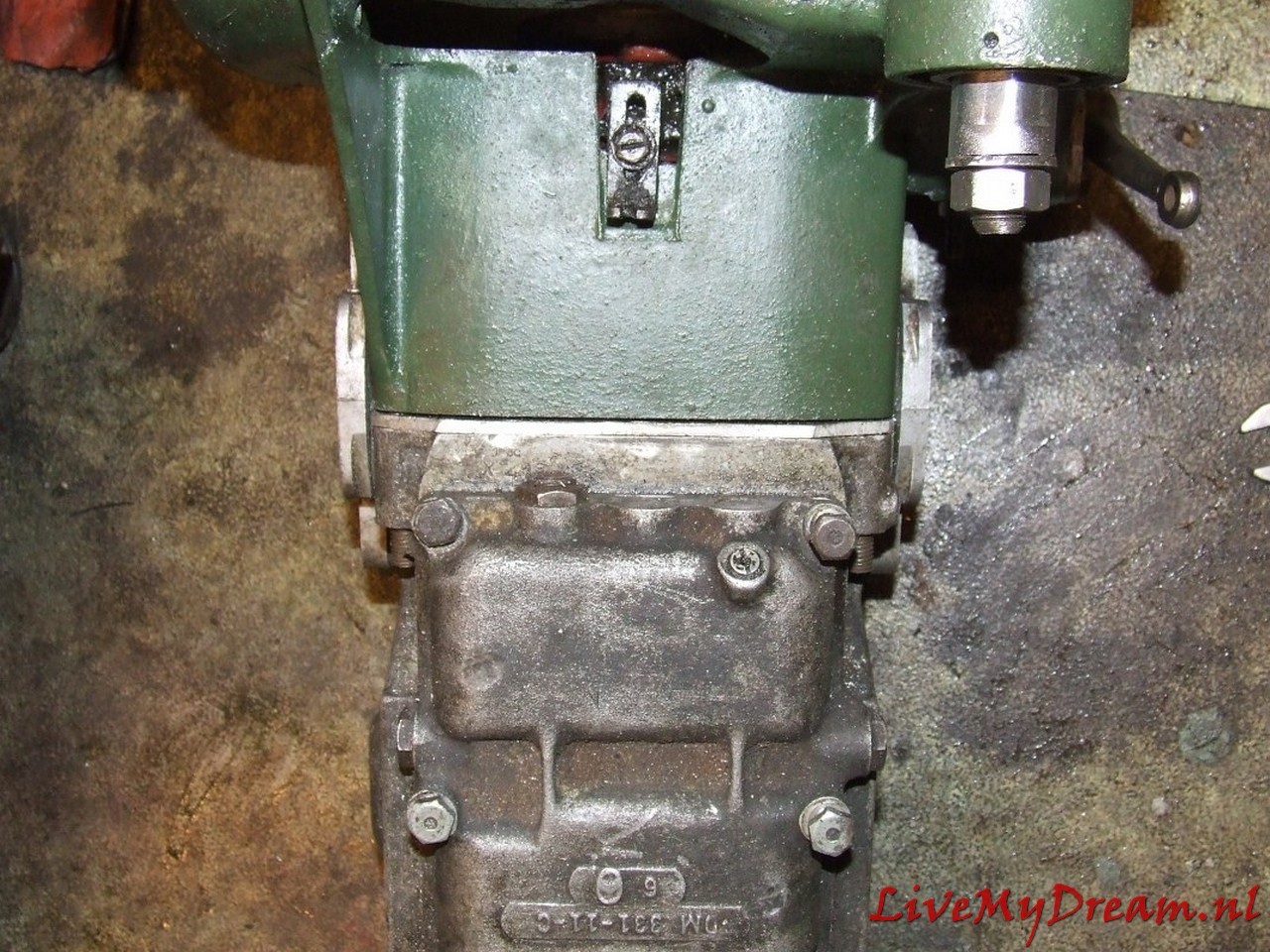
Above the required fitting/shim plate of 4mm thick aluminum is shown as used to make the 100% fit of the TA clutch housing to the ID box.
The main advantage of this solution is that the satellite housing is also free from the inside of the clutch housing and you don’t have to worry about the differential running into the clutch housing.
The reason for this required adjustment is due to the fact that the position (in the longitudinal direction) of the drive shafts on the TA compared to the ID has just shifted by 4mm.
The semi-circular recesses where the flanges on the ID box fit in and where the original oil seals on the TA box fit in are not the same on the ID side versus the side of the clutch housing.
On the TA the shape is exactly the same on both sides.
On the ID box, the hole for the flange is 4mm shallower on the gearbox side and 4mm deeper on the ID clutch housing side.
With a fitting plate between the ID box and the TA clutch housing the non-round shape due to the lack of 4mm is compensated so that the purely round shaped flanges fit exactly in the (again) round hole.
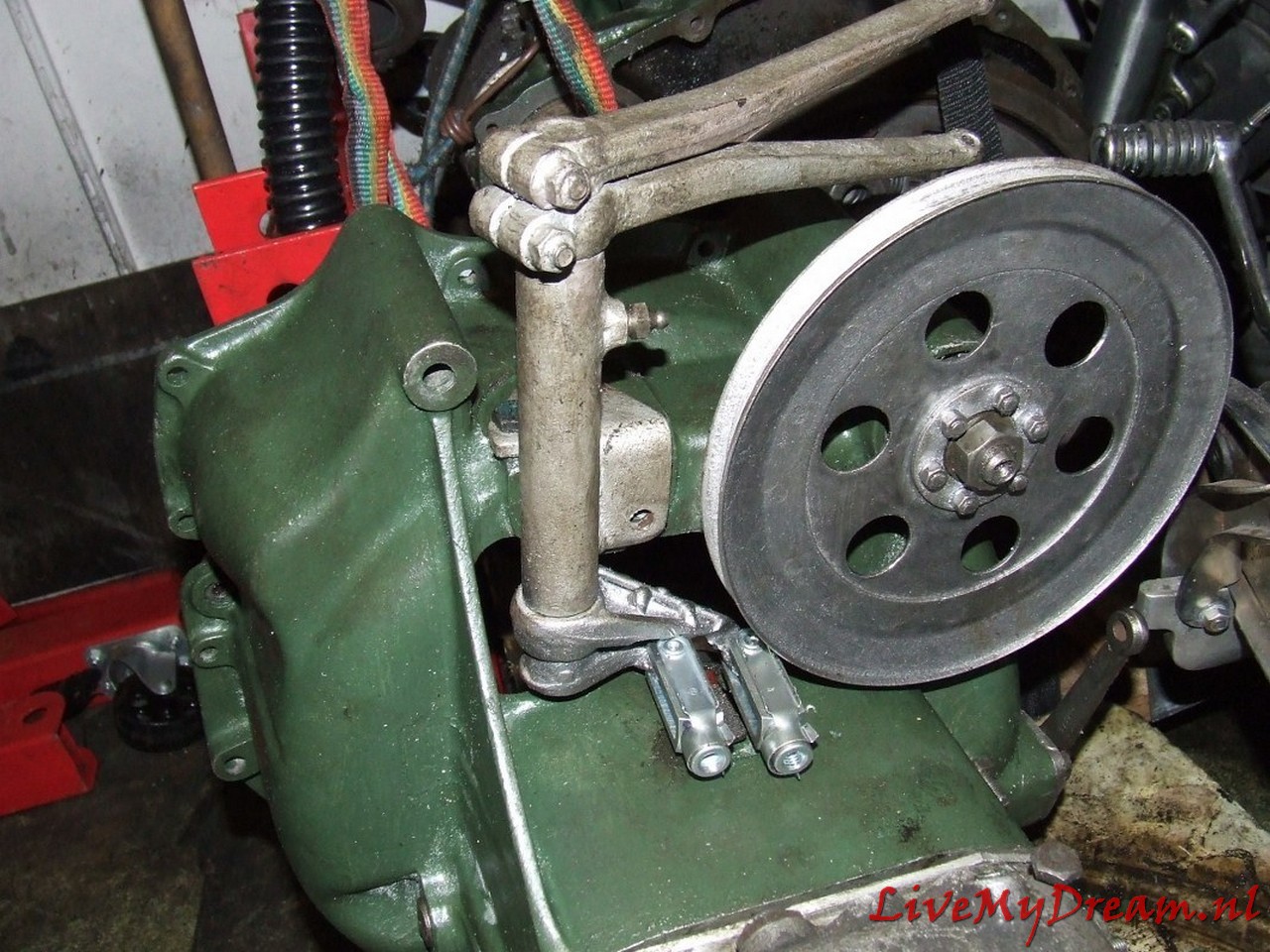
I had to completely modify the scoops of the gear controls at the bottom of the shift tower so that the newly developed rods can be operated for the ID box.
It took some thinking and trying but this solution works great!
As you can see in the picture, the ID pulley only just fits next to the right-hand scoop.
By using this pulley I immediately switched to a narrower V-belt.
That meant changing the water pump pulley, and mounting a 12 Volt alternator.
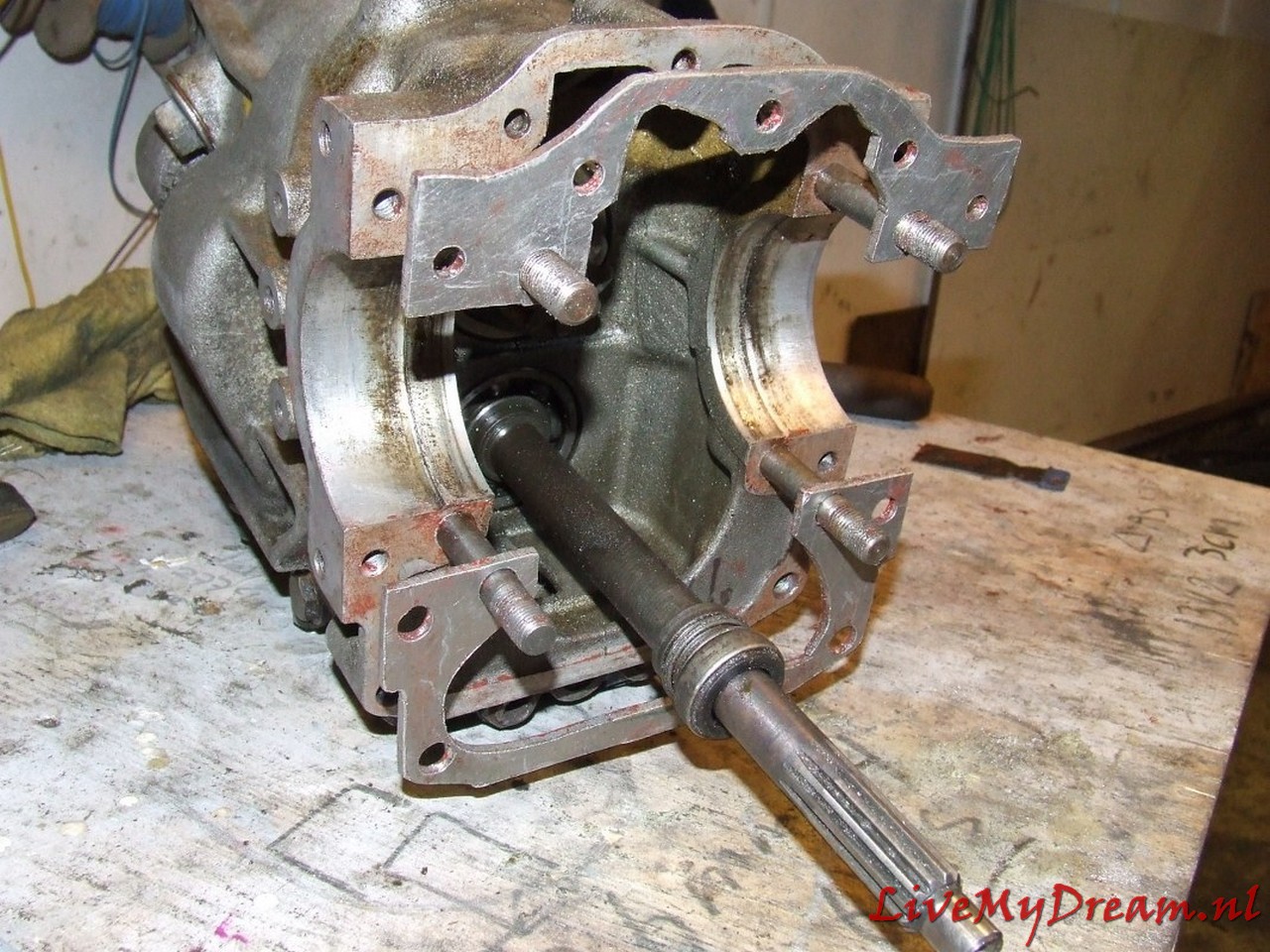
Above is the 4 mm gasket plate in detail.
During the assembly process I used thin paper gasket on both sides of the gasket plate.
That turned out to be the only way to get everything leak free.
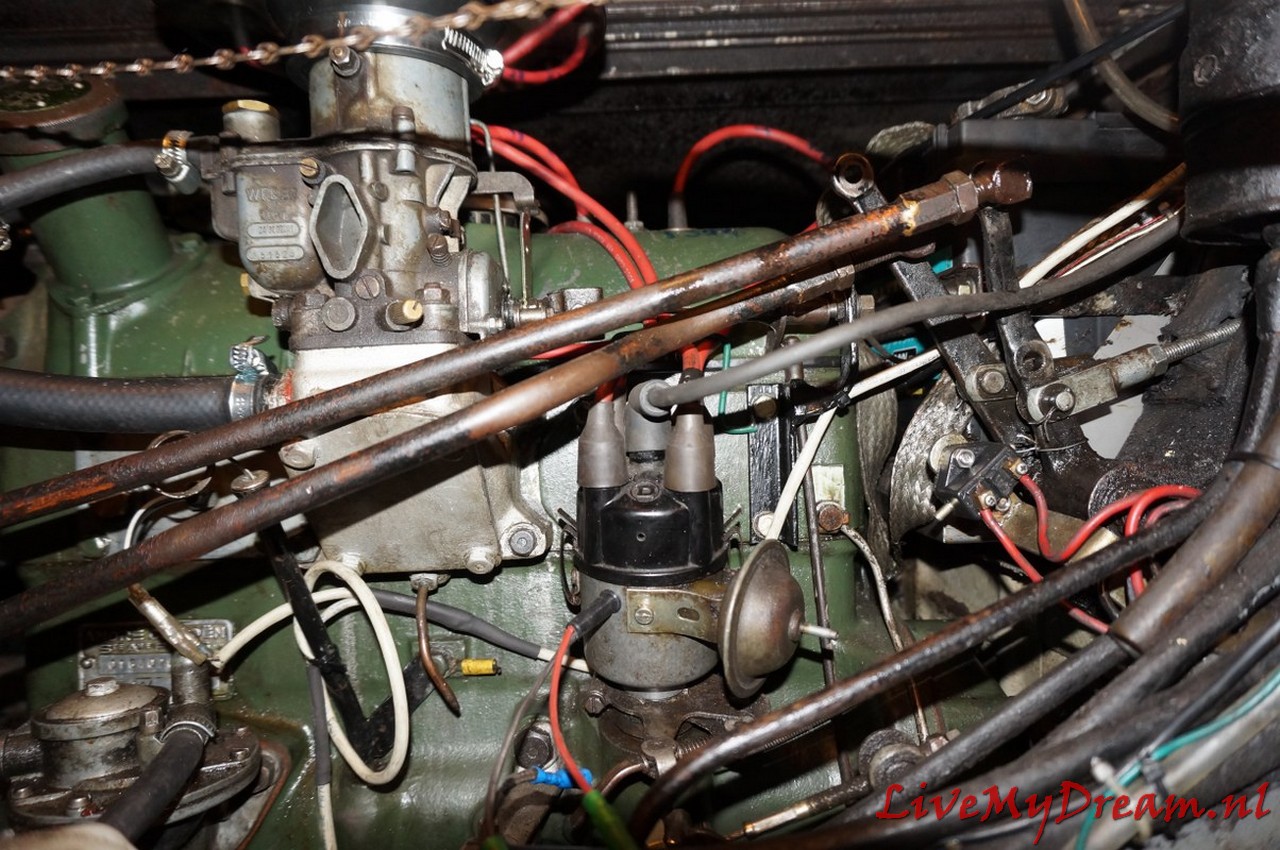
The switch rods between switch tower (left) and transmission levers (right) to the selector in detail:
Small additional challenge with me was that due to the installation of the ID engine and- associated cylinder head- the carburetor suddenly ran in the path of these switch rods.
Using a water pipe bender, I was able to keep the shift rods exactly clear of any fixed engine parts and it all just fit.
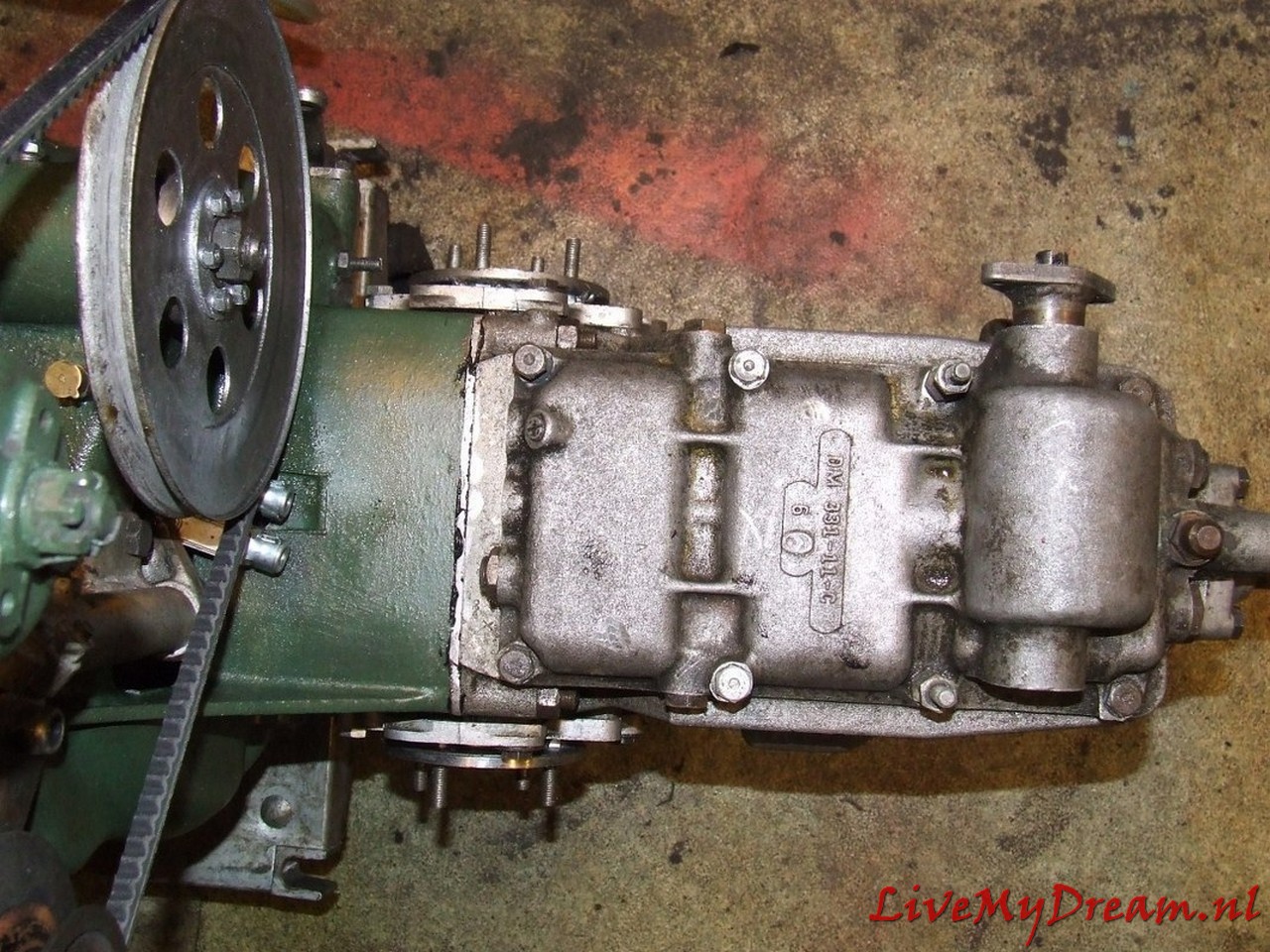
The gearbox without control rods mounted on the clutch housing.
If you look closely, you can see that here I still worked with the ID insert shafts, which I had shortened.
In the end, this solution did not work because the welded shafts kept breaking off at the weld.
In itself, this solution is possible, but then you would have to make (or have made) new shafts].
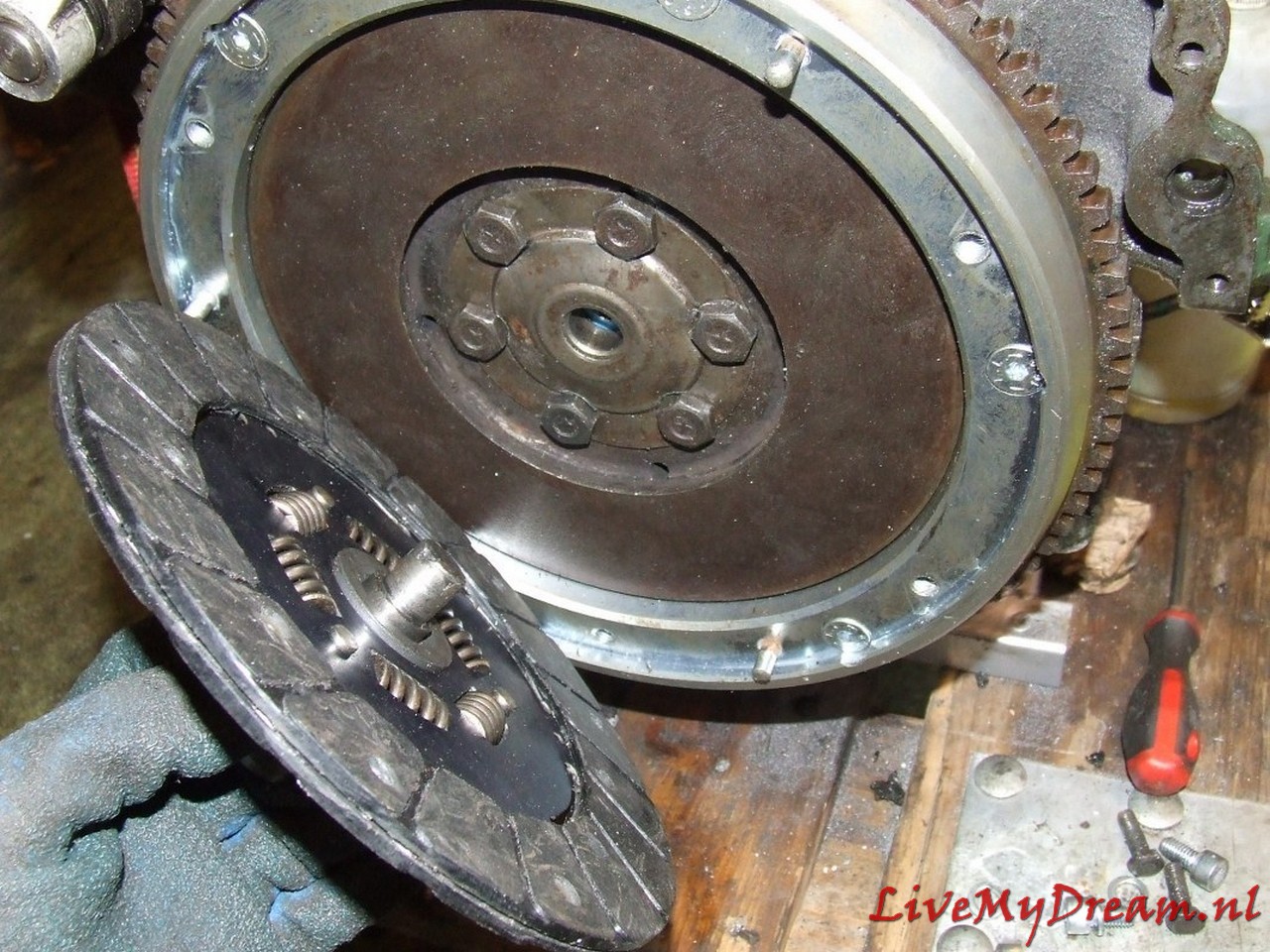
Above you can see the extension of the primary shaft by means of a bushing that comes on the primary shaft.
This bushing comes between the primary shaft and the top bearing of the crankshaft.
The goal is to keep the primary shaft from swinging.
The bushing in the photo was my prototype.
There are top bearings with different inner diameters in which the primary shaft fits and so here too practice was (again) my teacher.

Clutch plate in the (equally mounted) attachment ring of the newly installed diaphragm pressure group
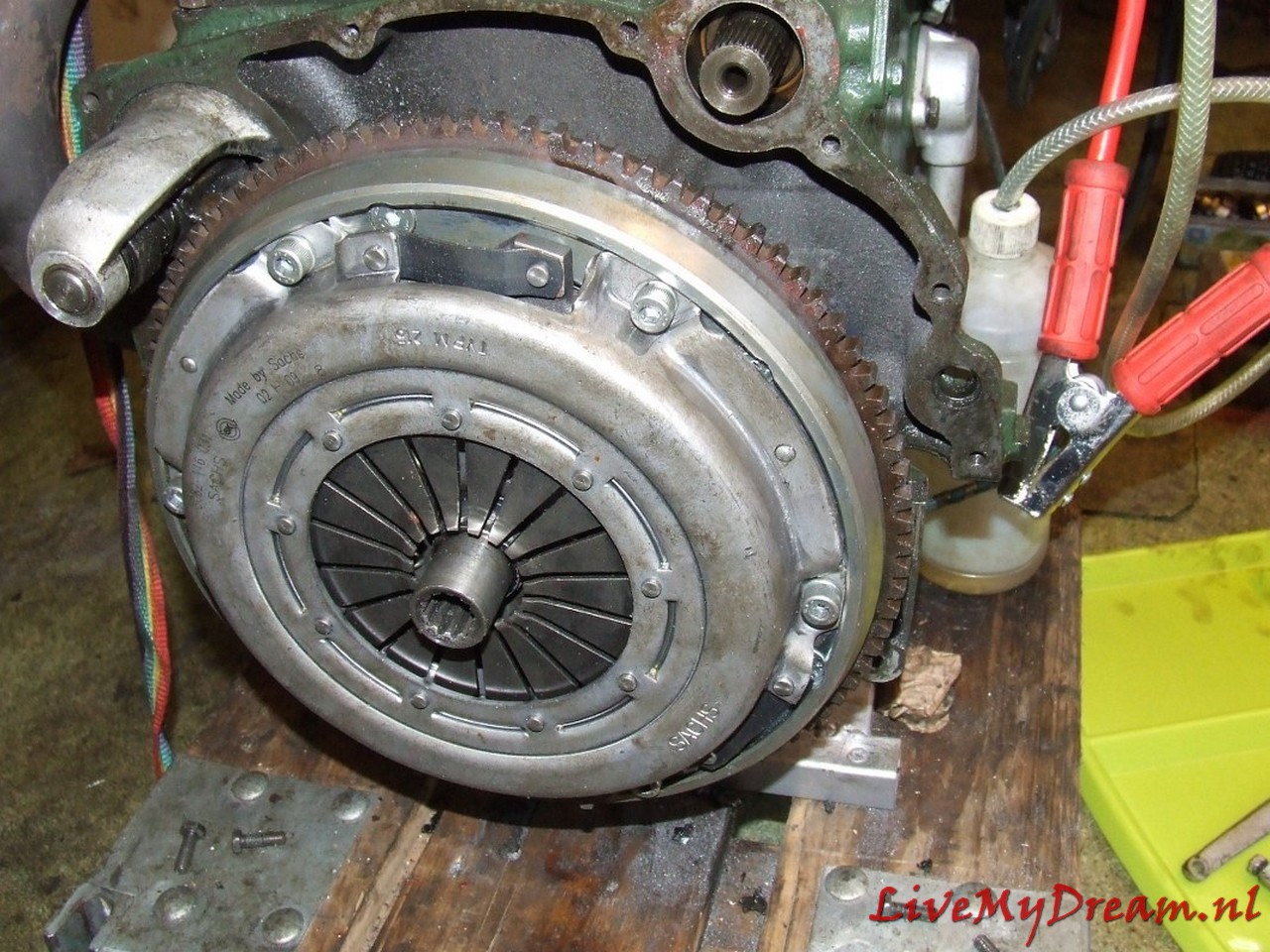
And the entire pressure plate with clutch plate mounted and the keyway of the clutch plate protruding outwards
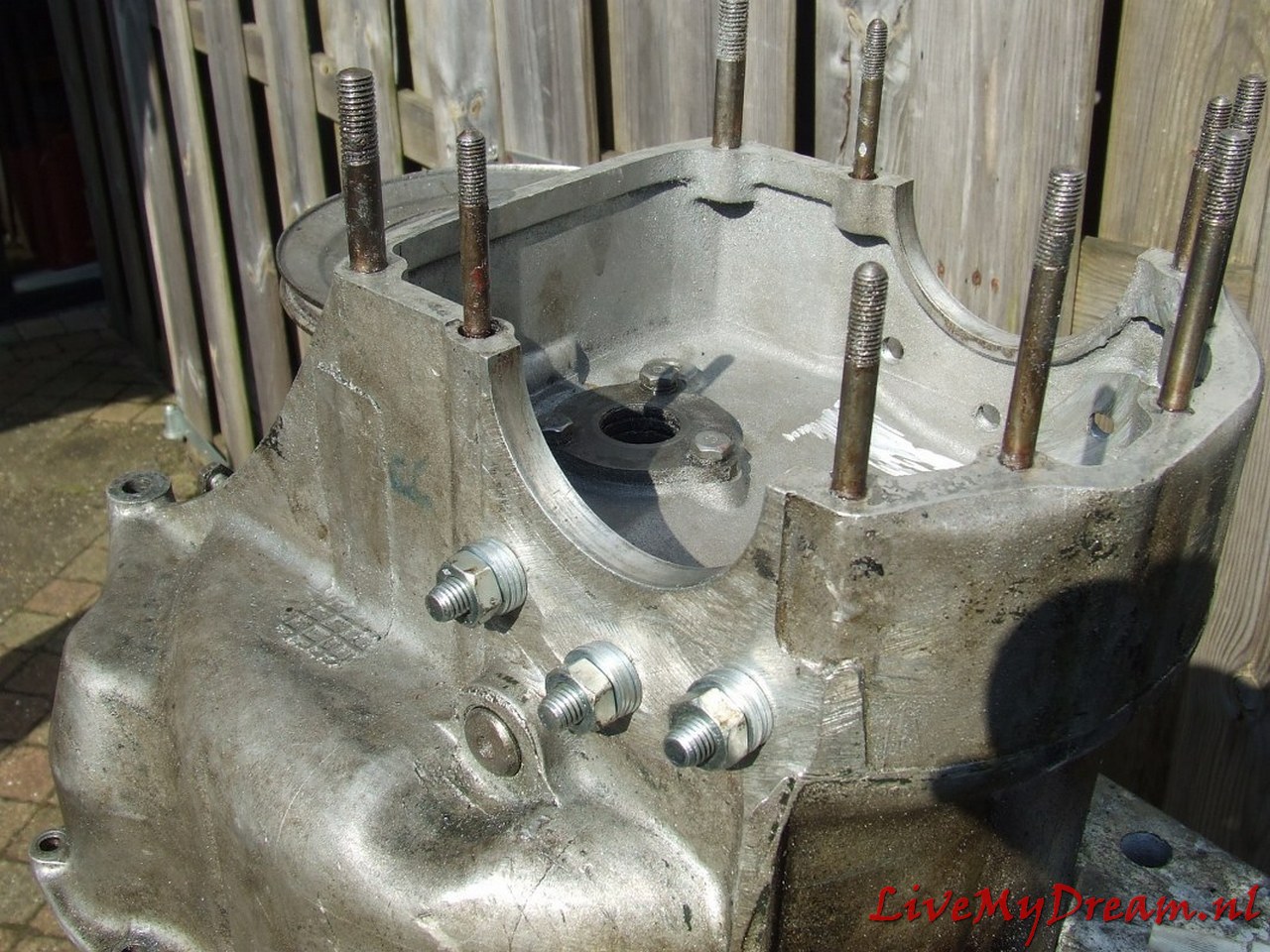
Clutch housing with M10 bolts for securing the flanges.
The M10 bolts are mounted through and through in the cheeks of the housing.
Previously I experimented with other solutions but with tapping, mounting bushings and the like I did not get it sufficiently oil-tight.
In the above manner with rings and gaskets it is perfectly tight!
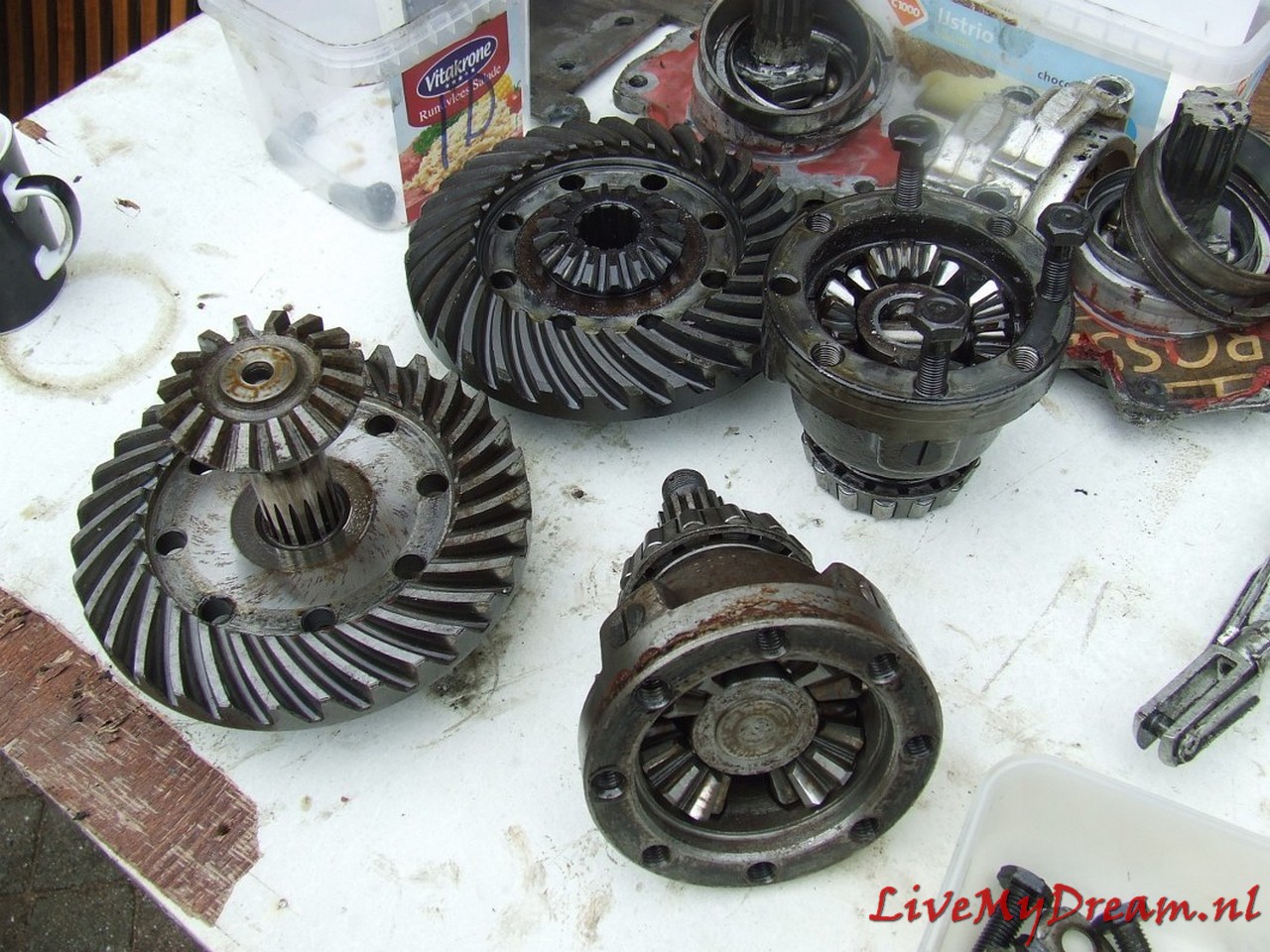
This was a bit of a job: Making 1 new one from the donor parts of 2 differentials.
In itself not difficult when you think of what will fit:
Pinion from ID is used, so the satellite gear from ID must be used.
The outgoing shafts from the TA are used so the satellite gears from the TA must be fitted.
The thinner output TA shaft is placed in the satellite gear of the ID so a fit bushing must be pressed into the ID satellite wheel so the TA shaft can rotate freely but tightly in it.
The Satellite housing of the TA is used (bowl-side where the gears are) with the fixed (TA) shaft attached.
In the picture above you see the bottom left satellite gear with freely rotating output shaft.
Bottom right you see the bowl part of the satellite housing with the satellite gears and fixed output shaft.
The original TA differential works with bucket-shafts with keyways on the outside on which the TA bucket-shafts can be mounted externally.
The advantage here is that this allows you to easily replace the large retaining rings of the TA box.
So in the photo above, the bottom differential is the TA differential.
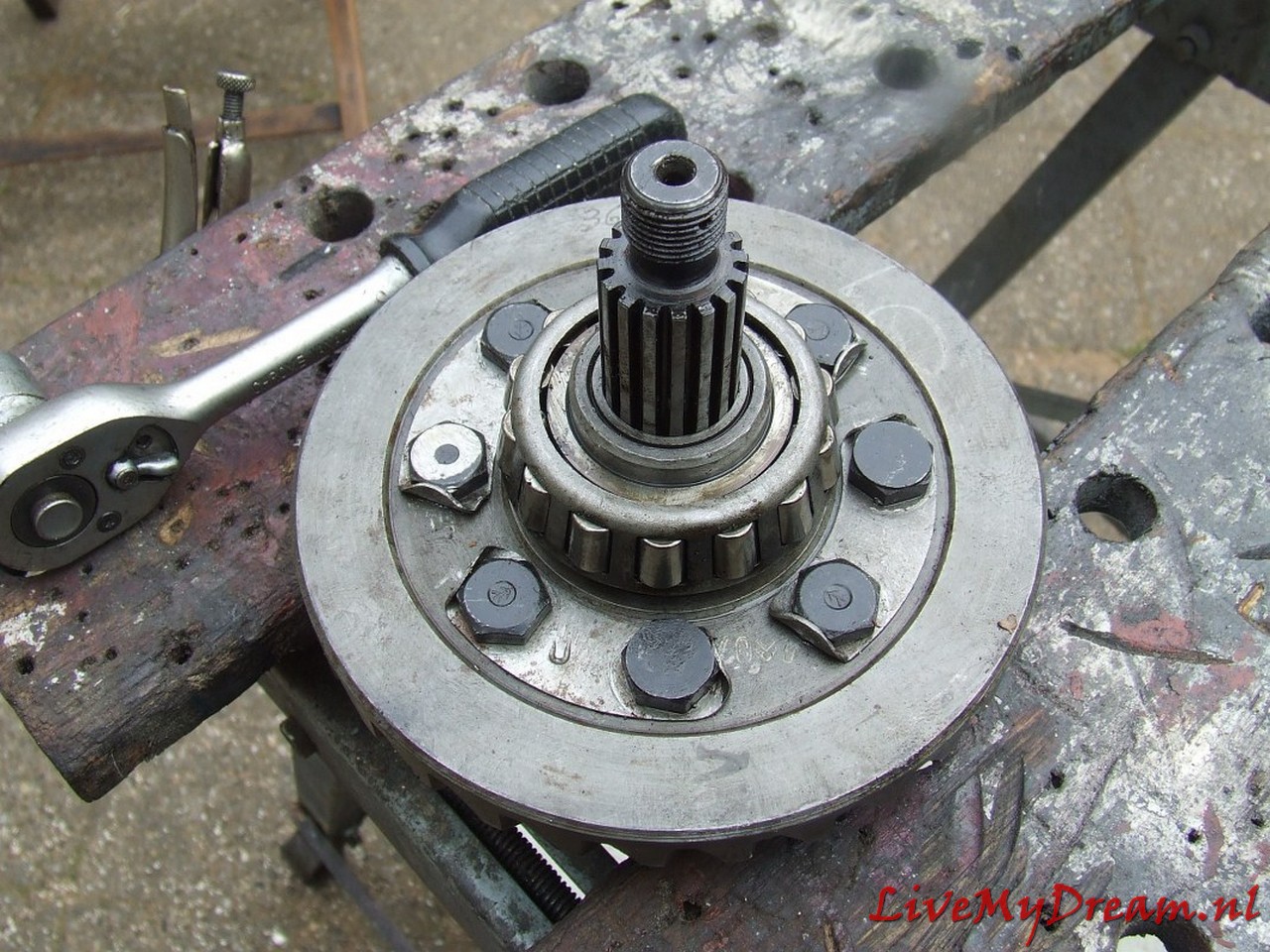
Above: Finished and assembled differential. You can see the fitting bushing sitting nicely
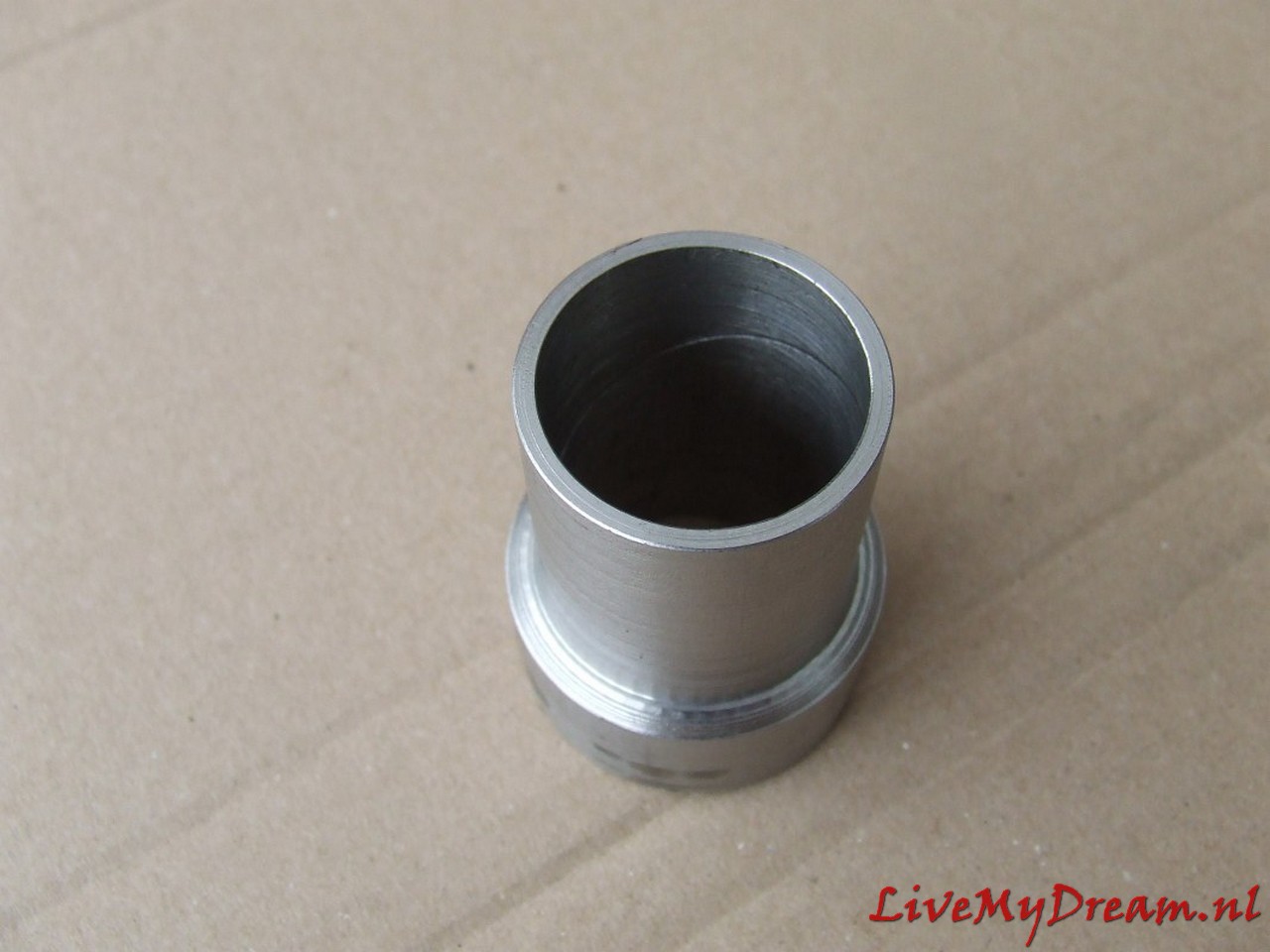
Above you can see the made fit bushing with oil groove on the free turning inside.
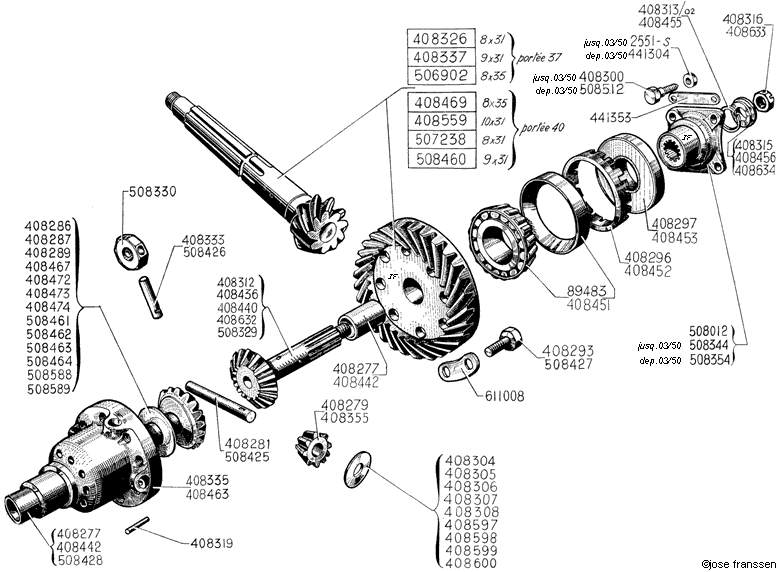
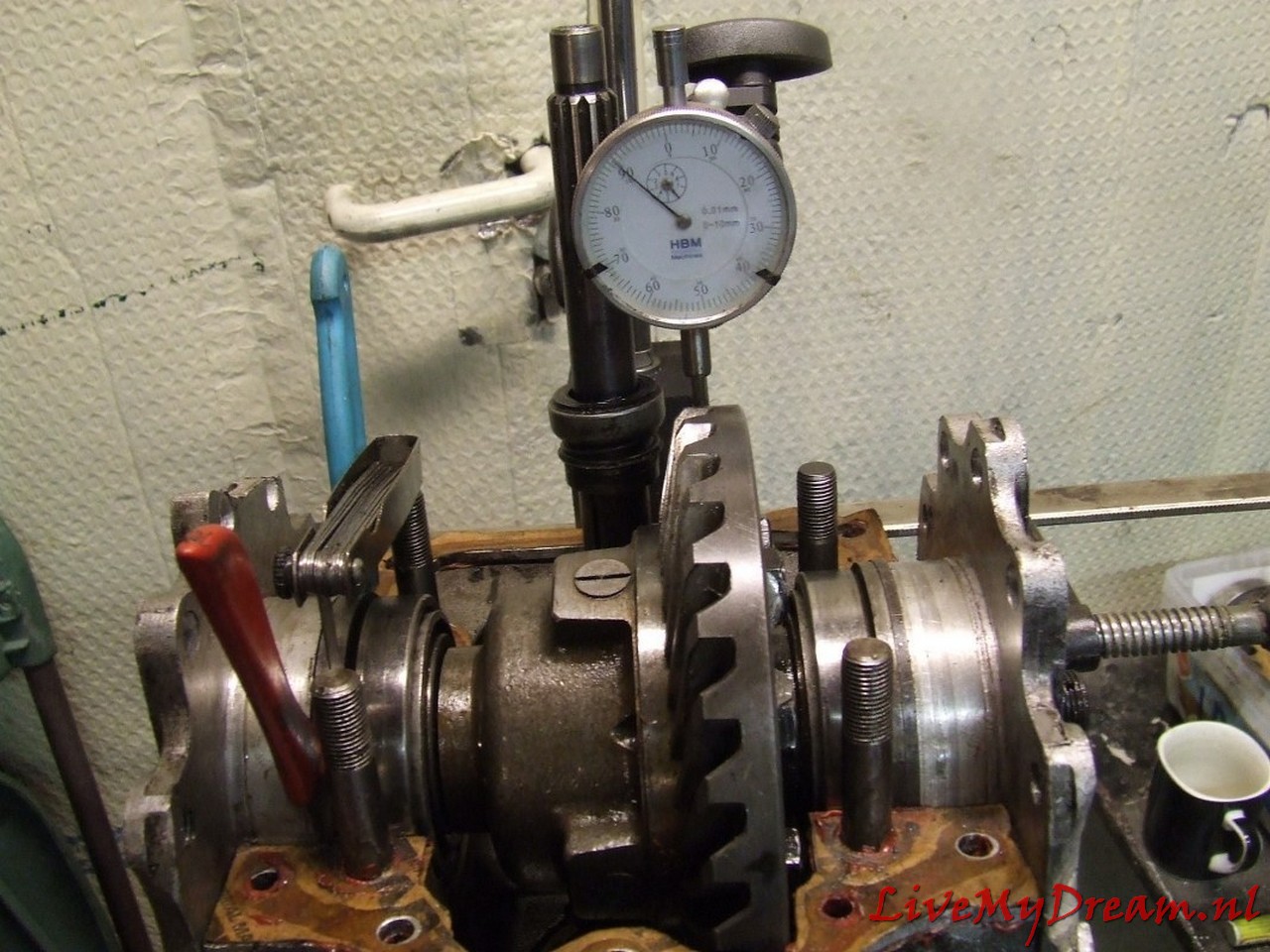
Timken bearings tighten but not too tight….

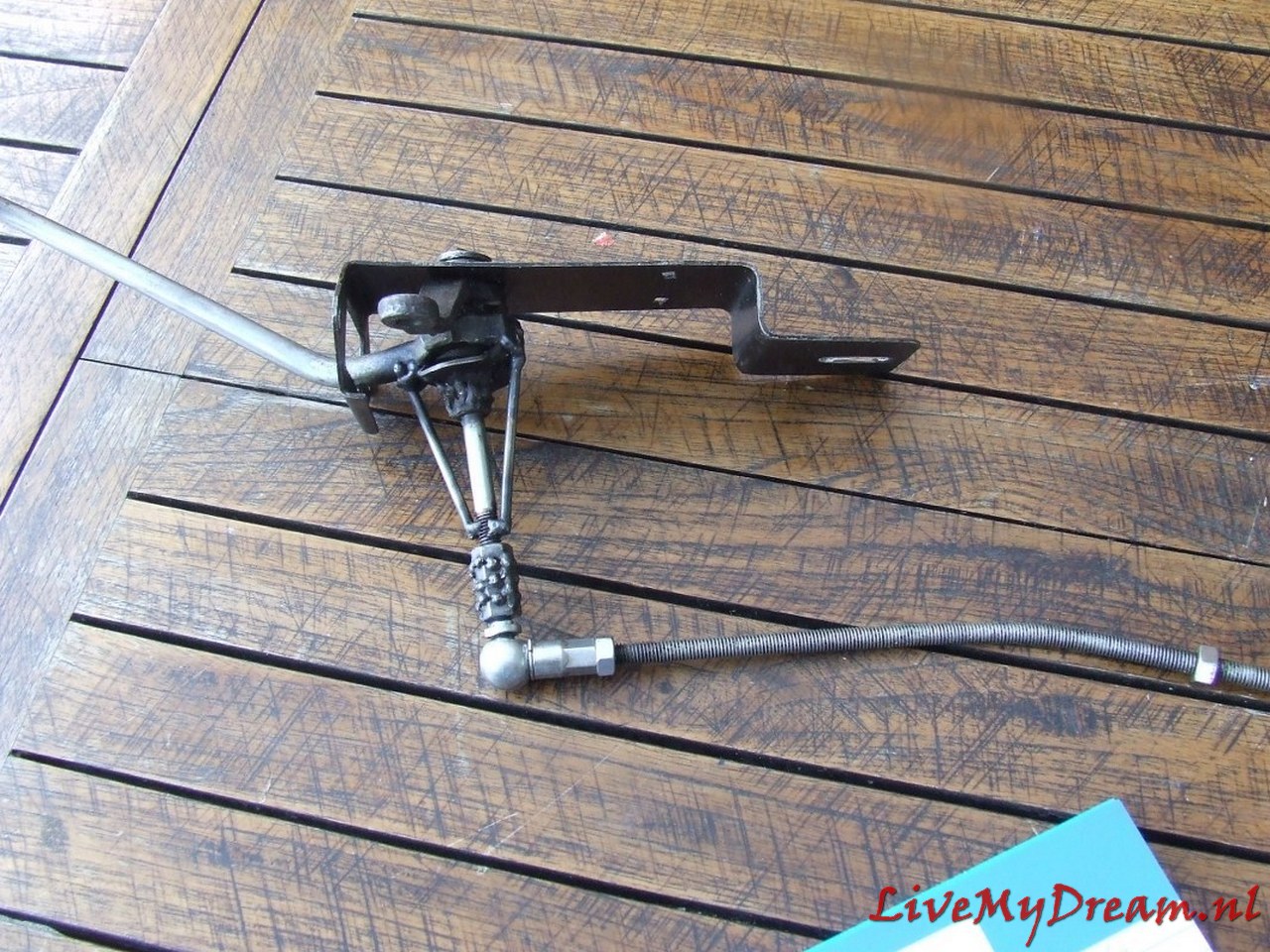
Converted switch selector/levier, in the experimental phase.
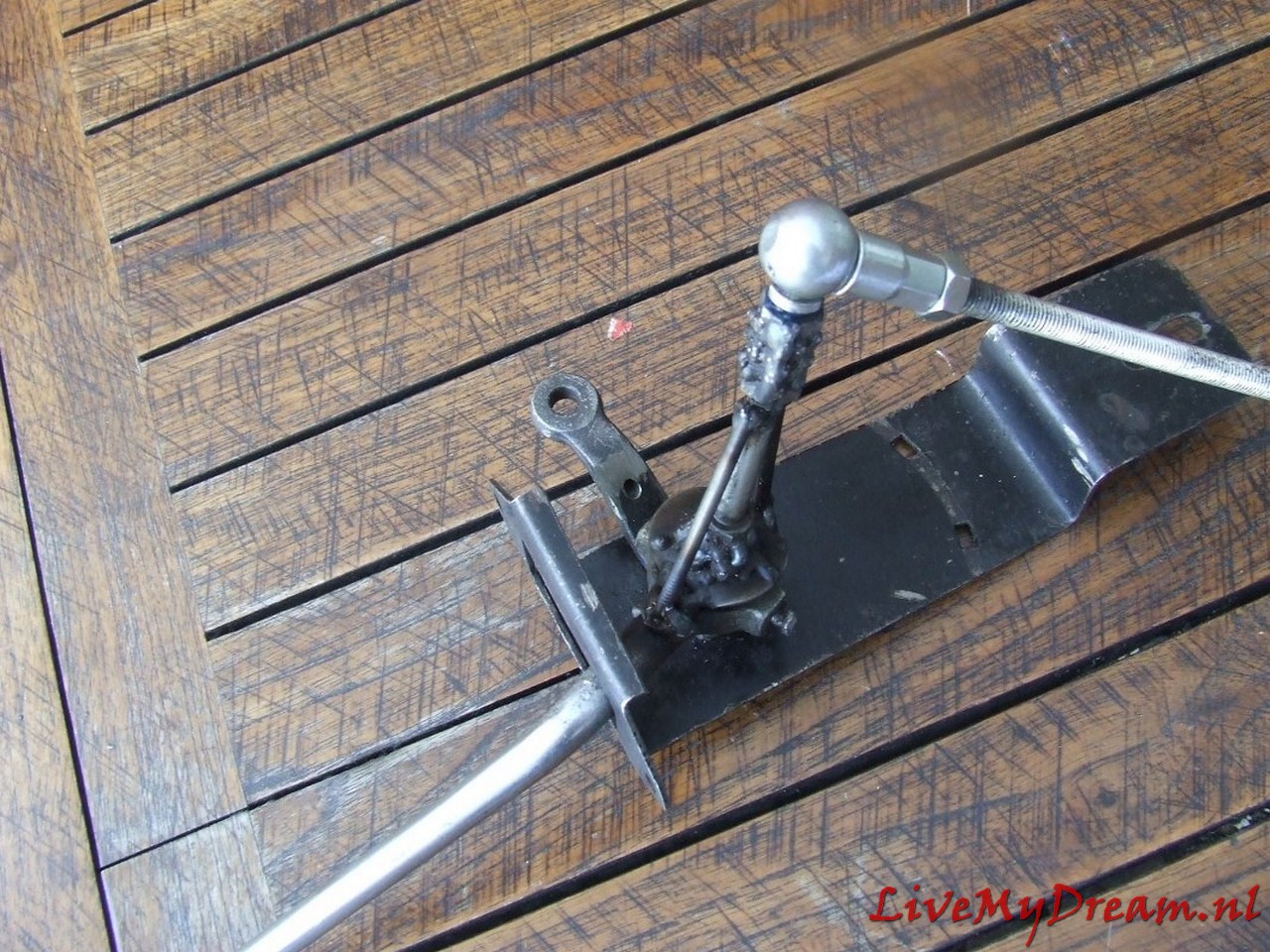
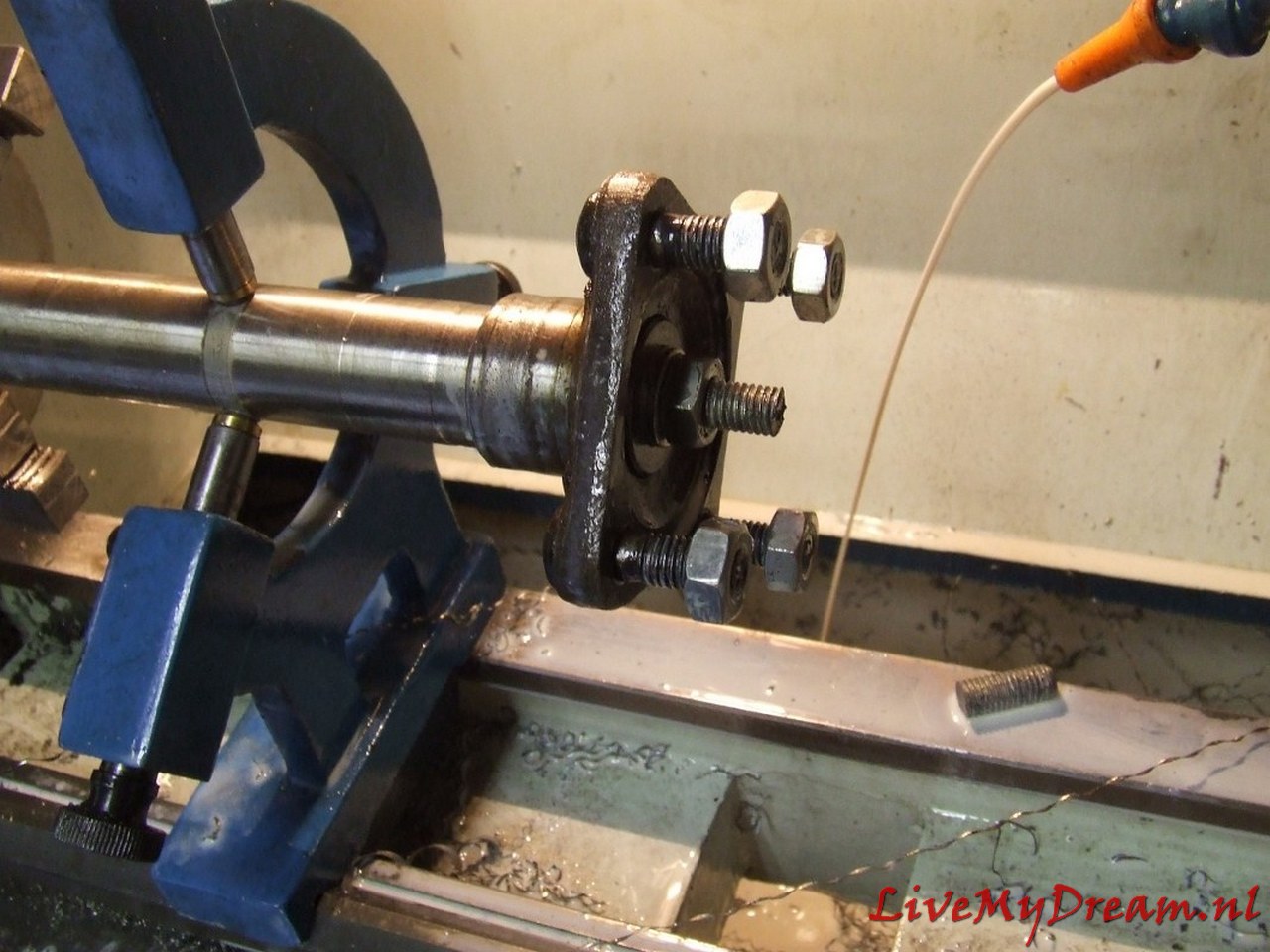
Turn shaft chuck to commercially available bearing size
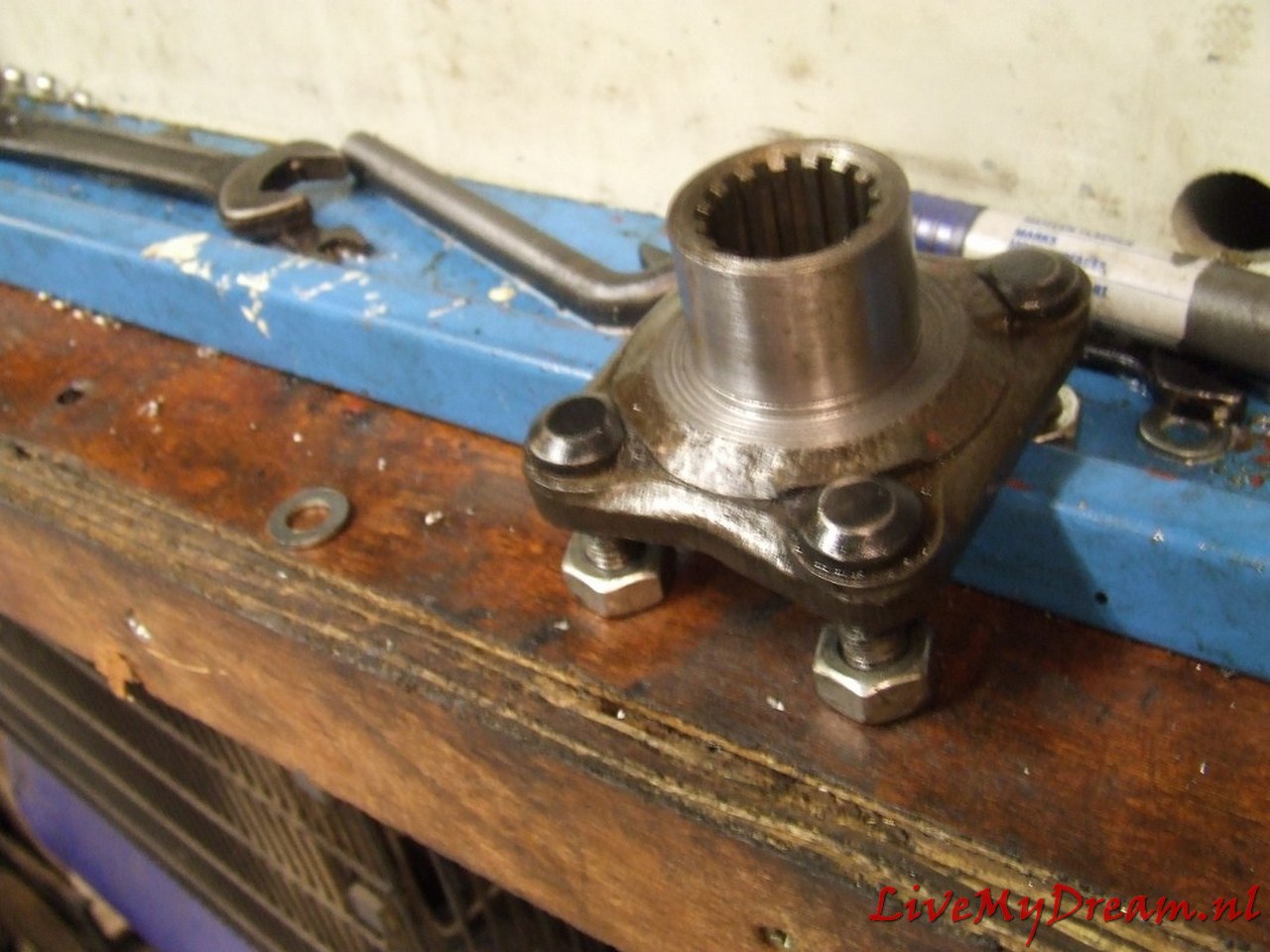
And the turned down result of the axle claw of the TA with inner splines.
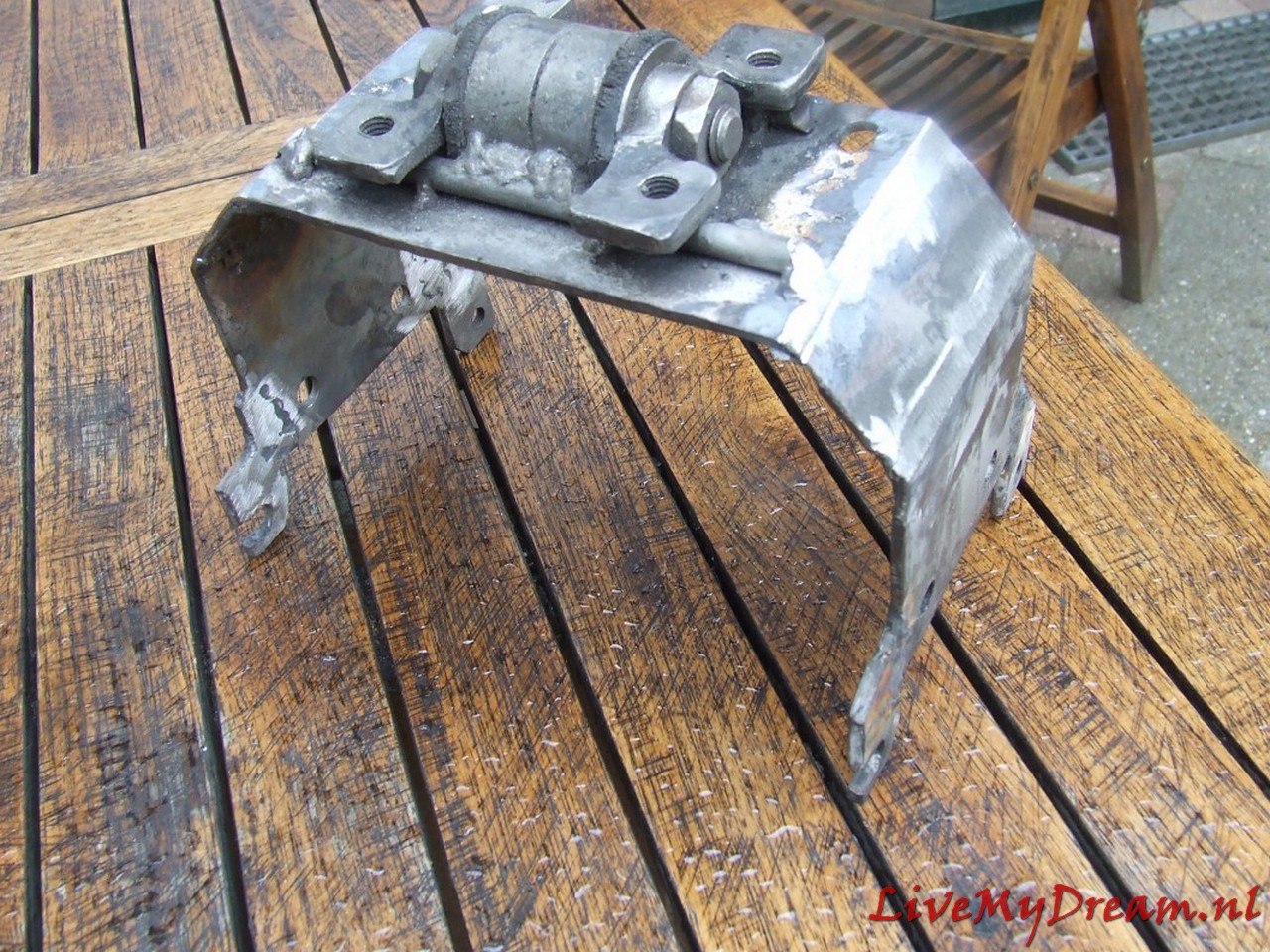
Mounting Bracket.
I chose a very robust setup, since the motor/box/drive shafts are all suspended from this point.
In addition, I chose to simply reassemble the cross pieces of the drive traverse to maintain sufficient strength.
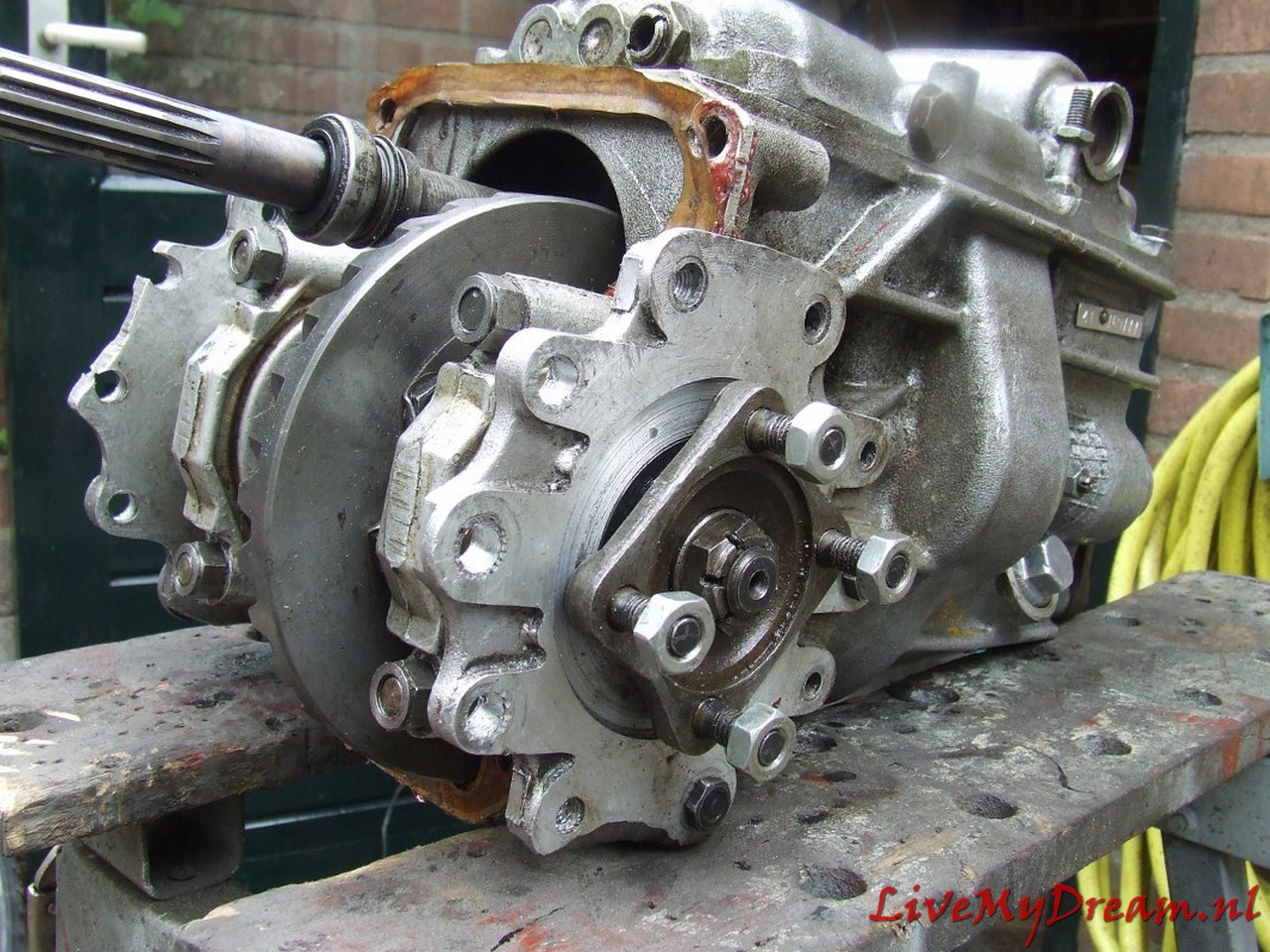
Please note above: On the underside of the flanges, I have ground away about 2 cm of material on both sides.
This is because these points protrude from the original TA body.
This means that they come up against the cradle just above the passage of the drive shafts.
So I had to remove some material. I can’t remember the number of times I have assembled and disassembled the gearbox, but at least it was so many times that I can now do it blindly and very quickly.
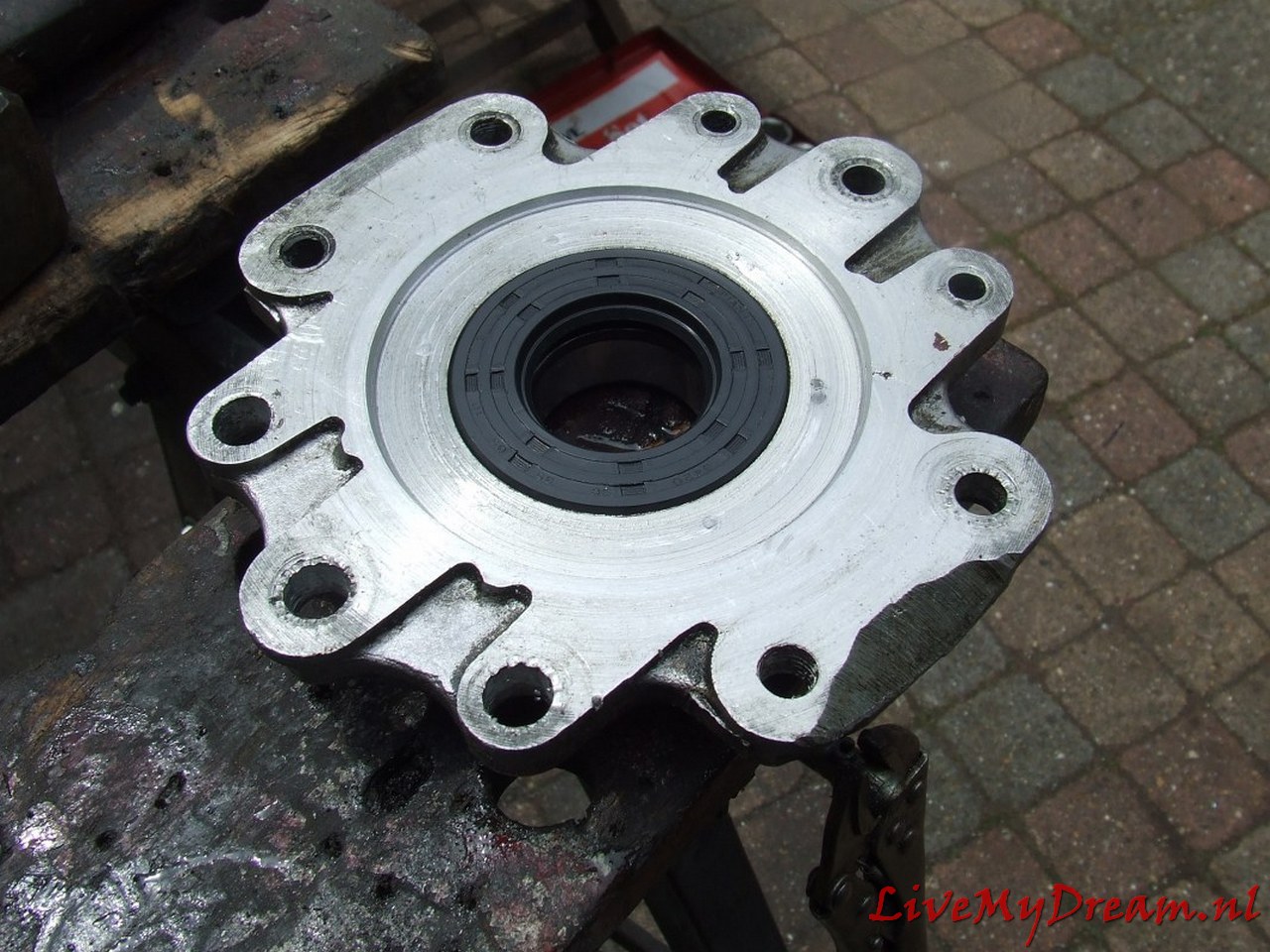
Above again the removed material: Handy to do BEFORE mounting!
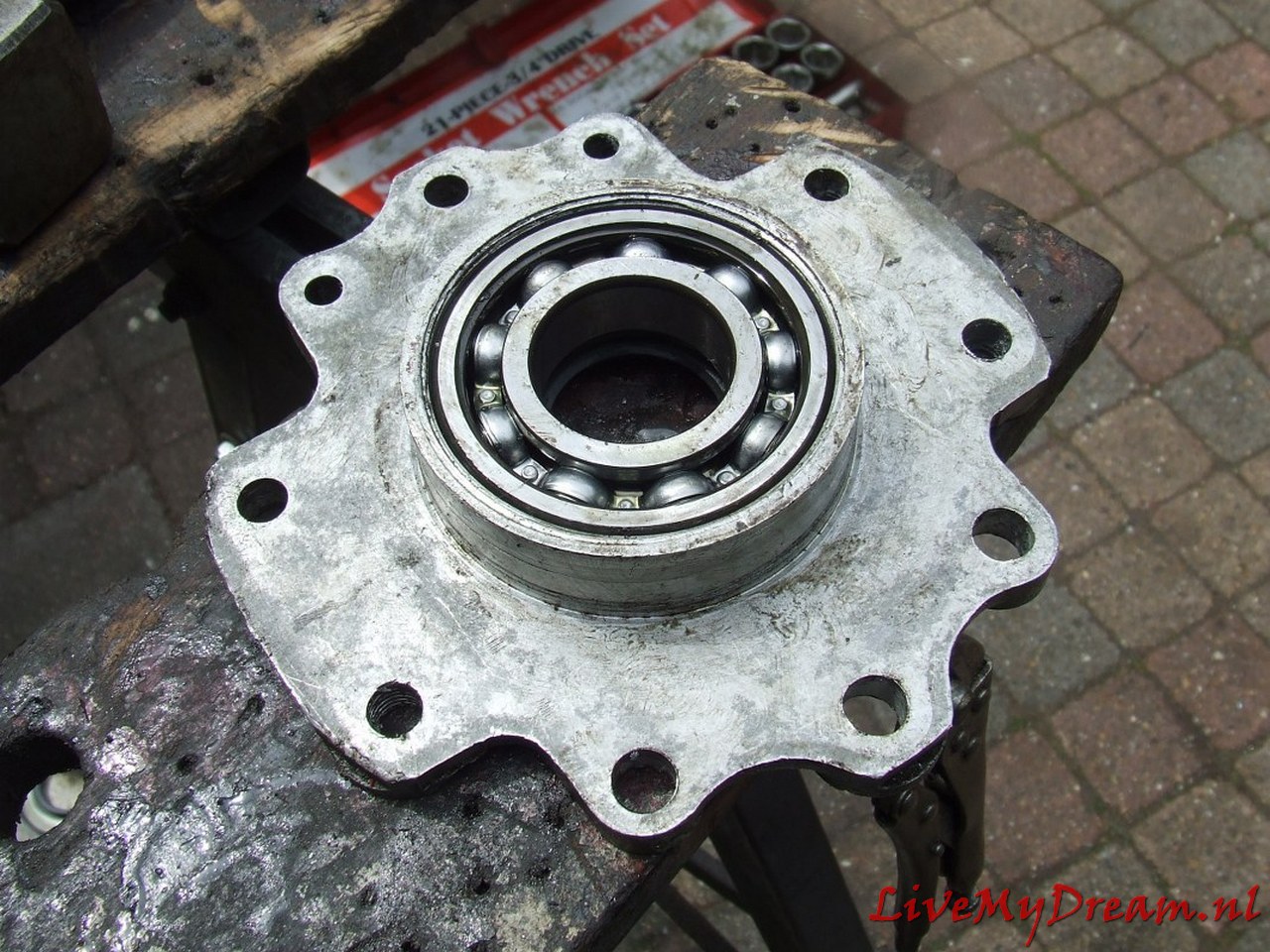
Bearing for the axle claws. I heated this part in the oven at 60 degrees before final assembly.
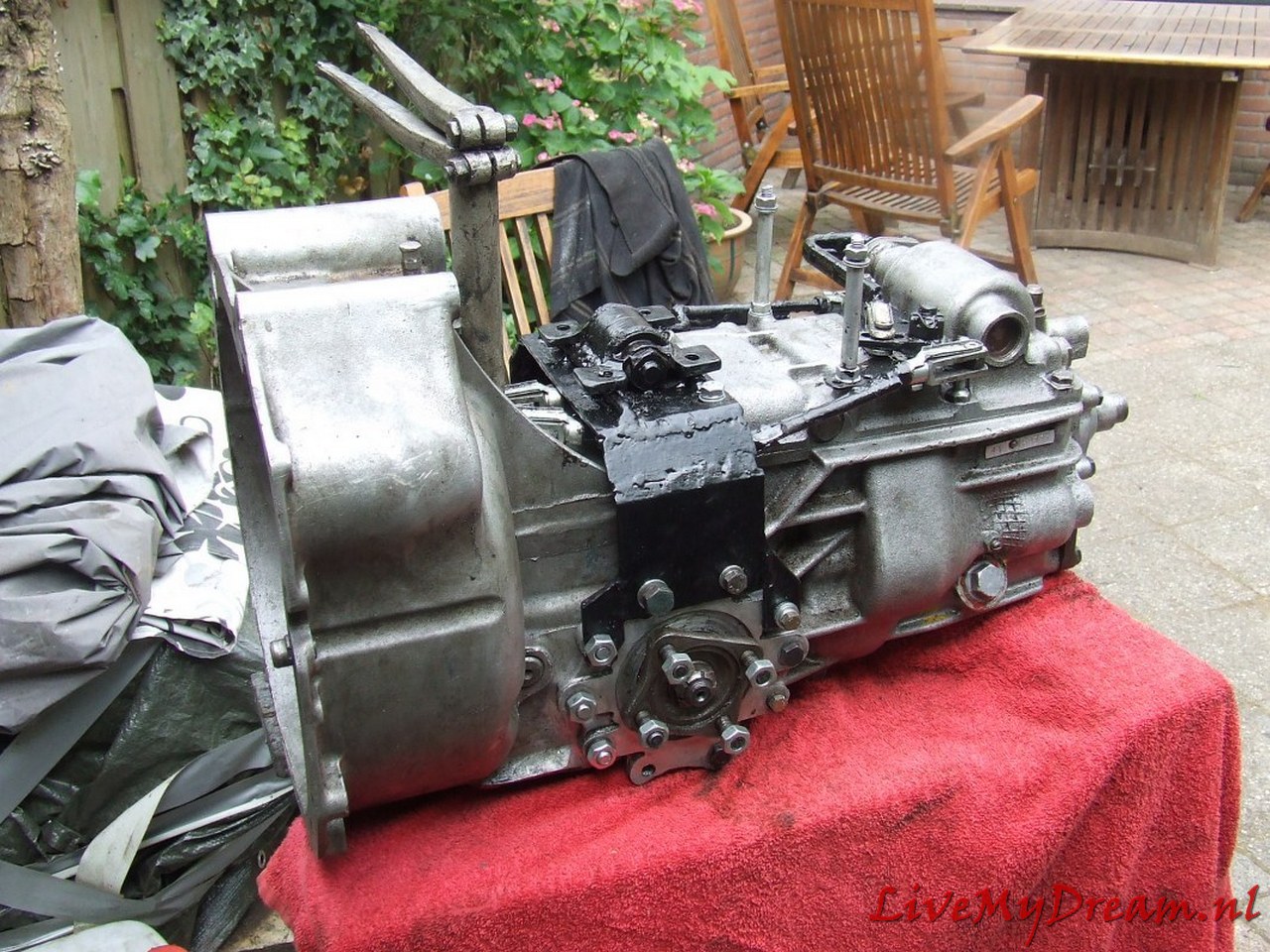
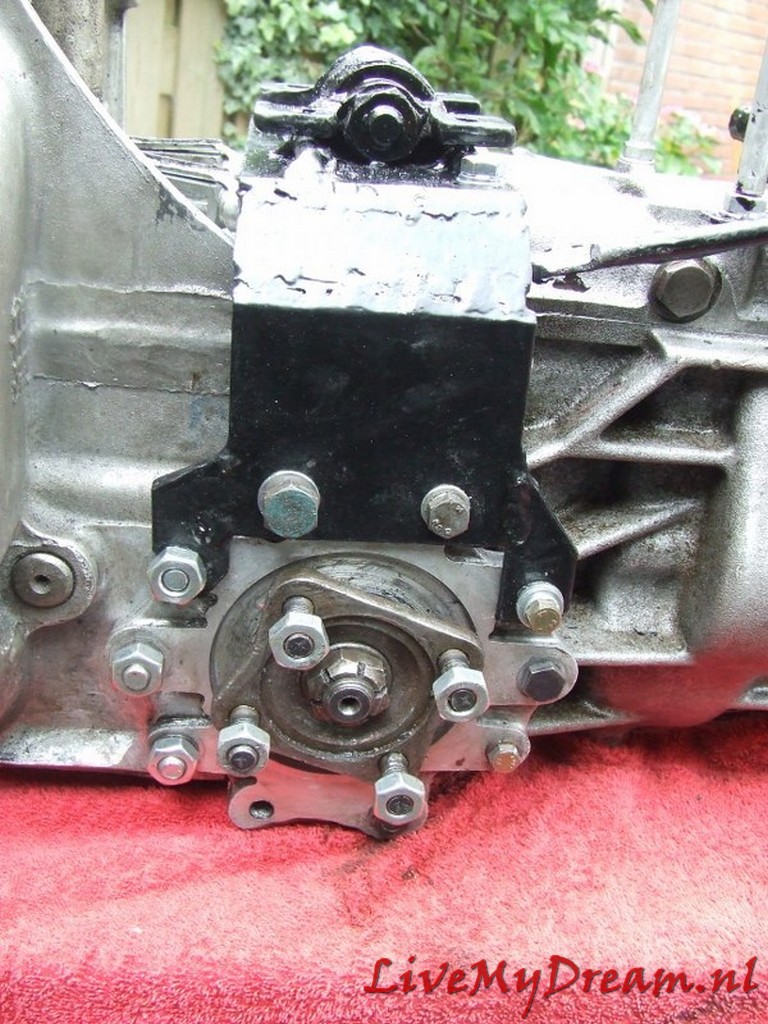
Ready.
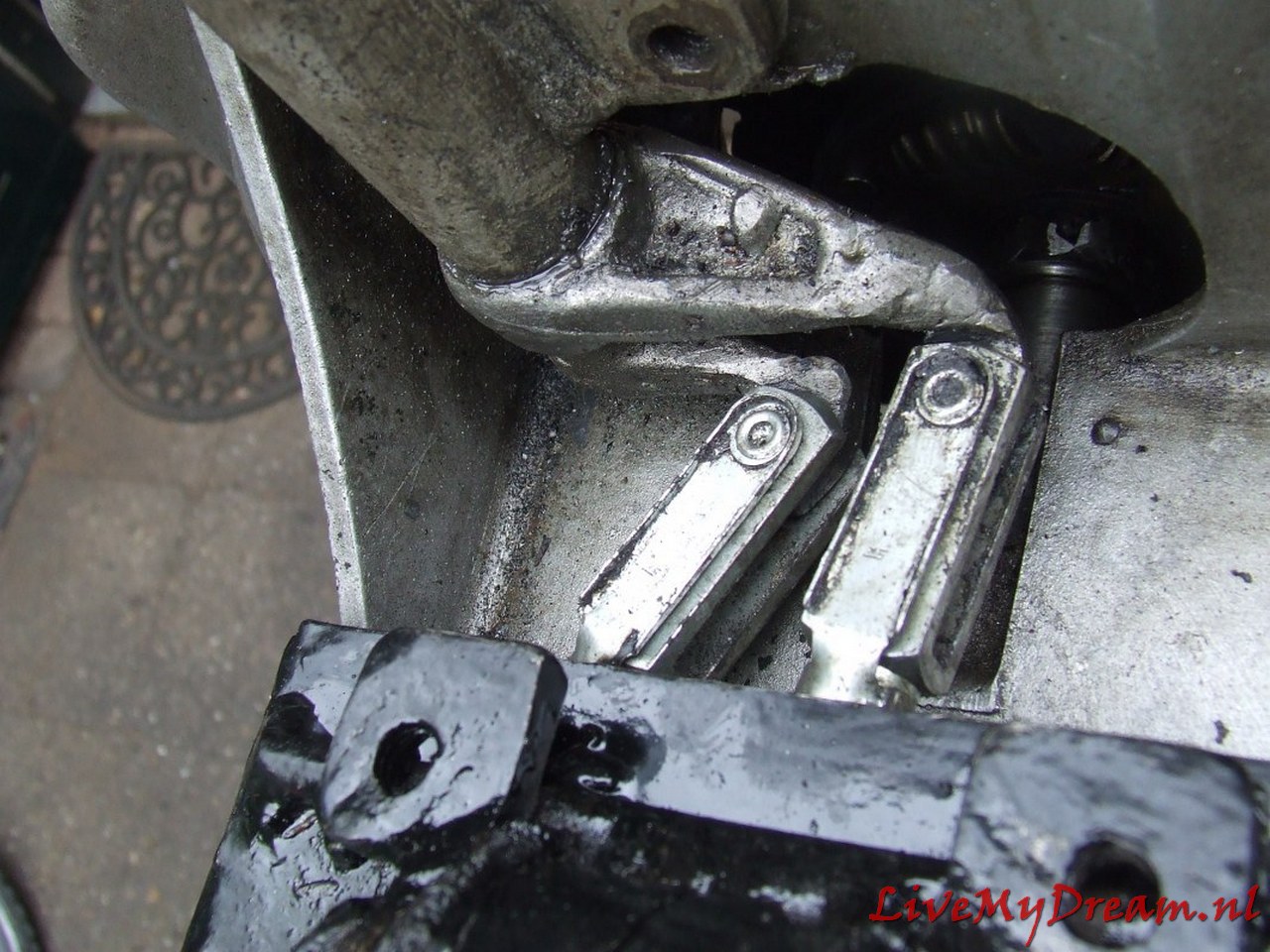
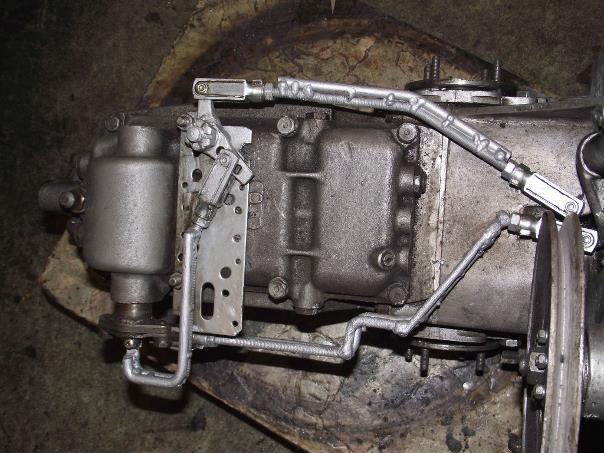
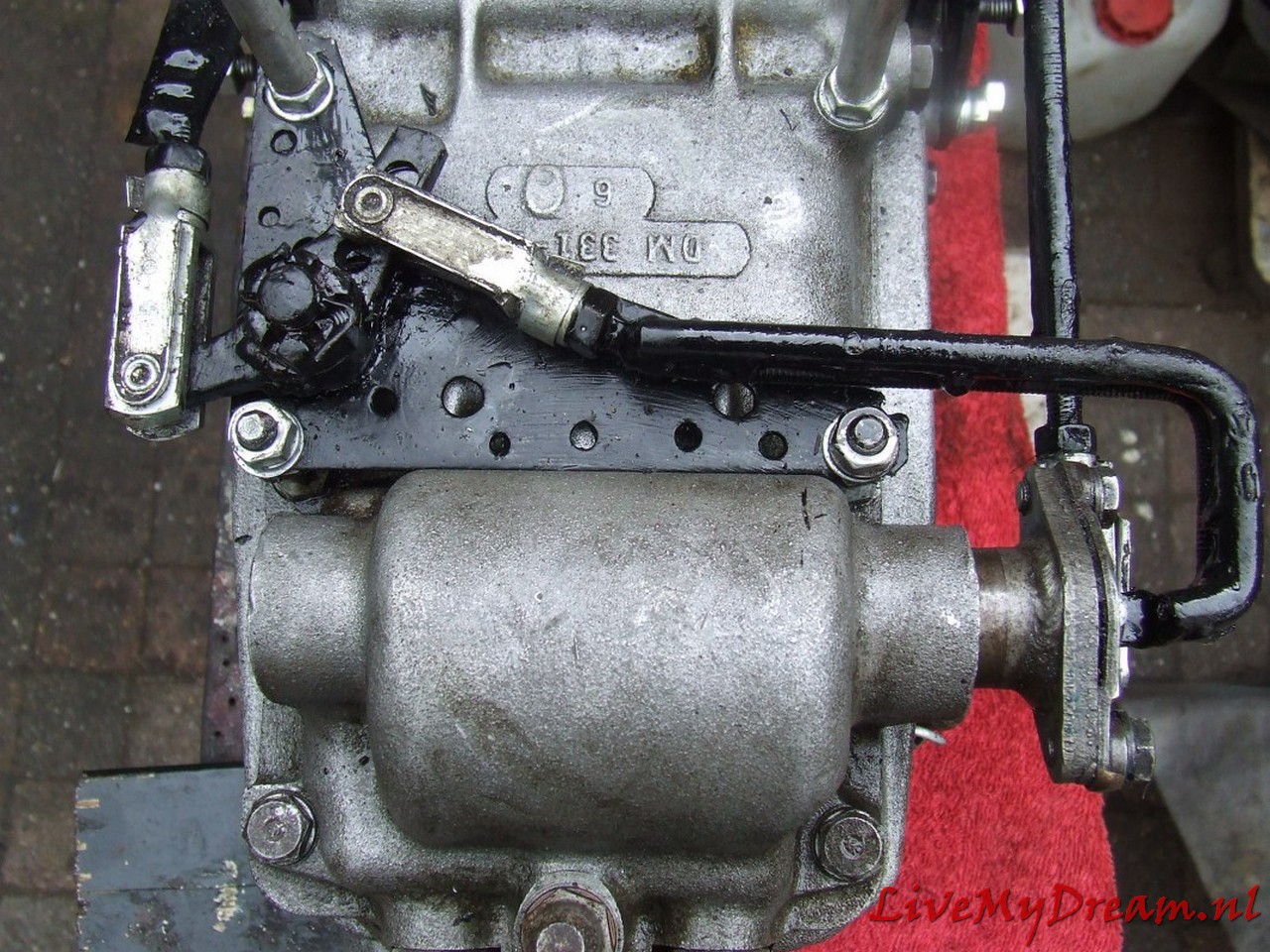
Shifting axles. Left the up/down movement of the shifter and right the left/right movement….
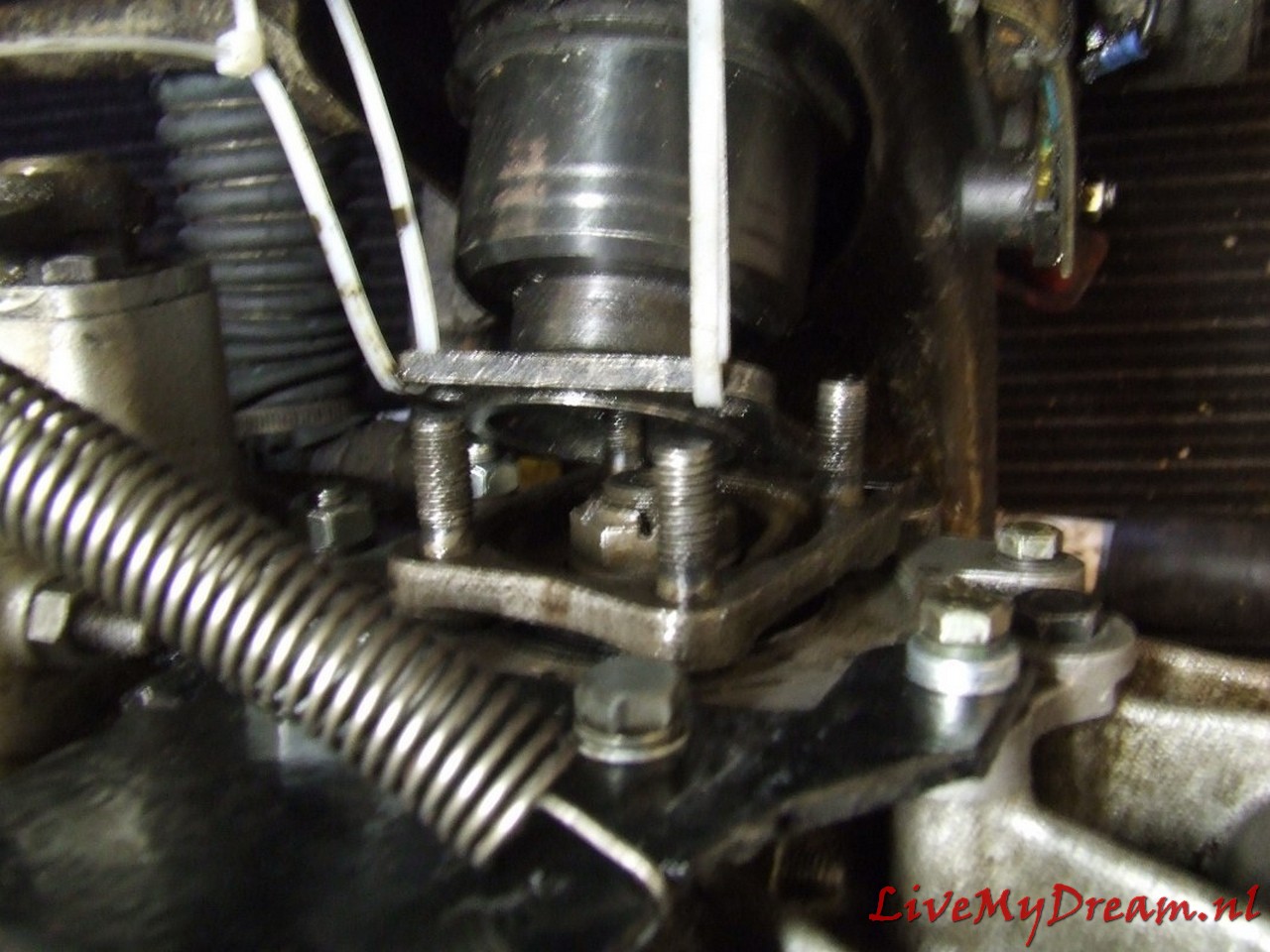
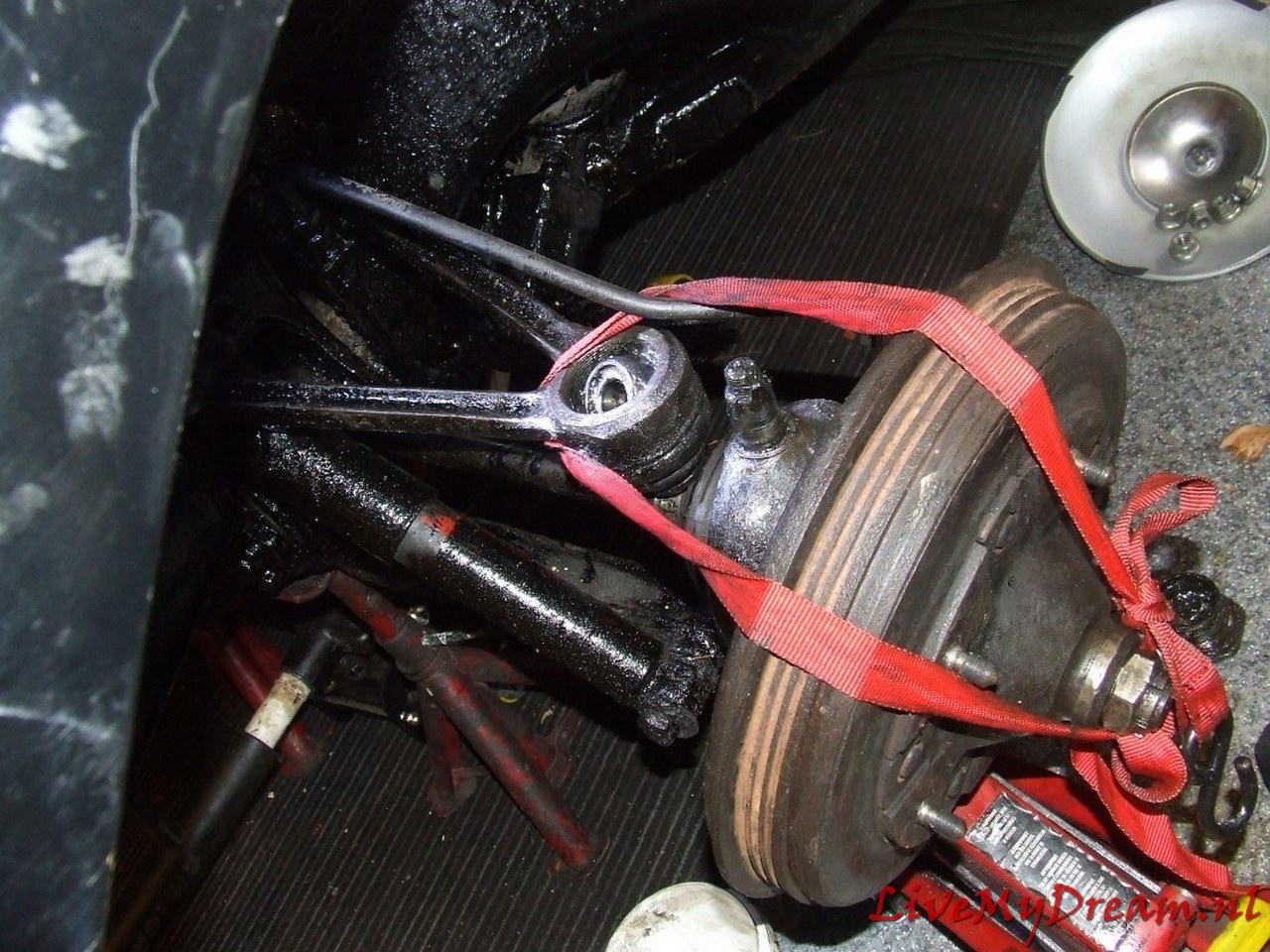
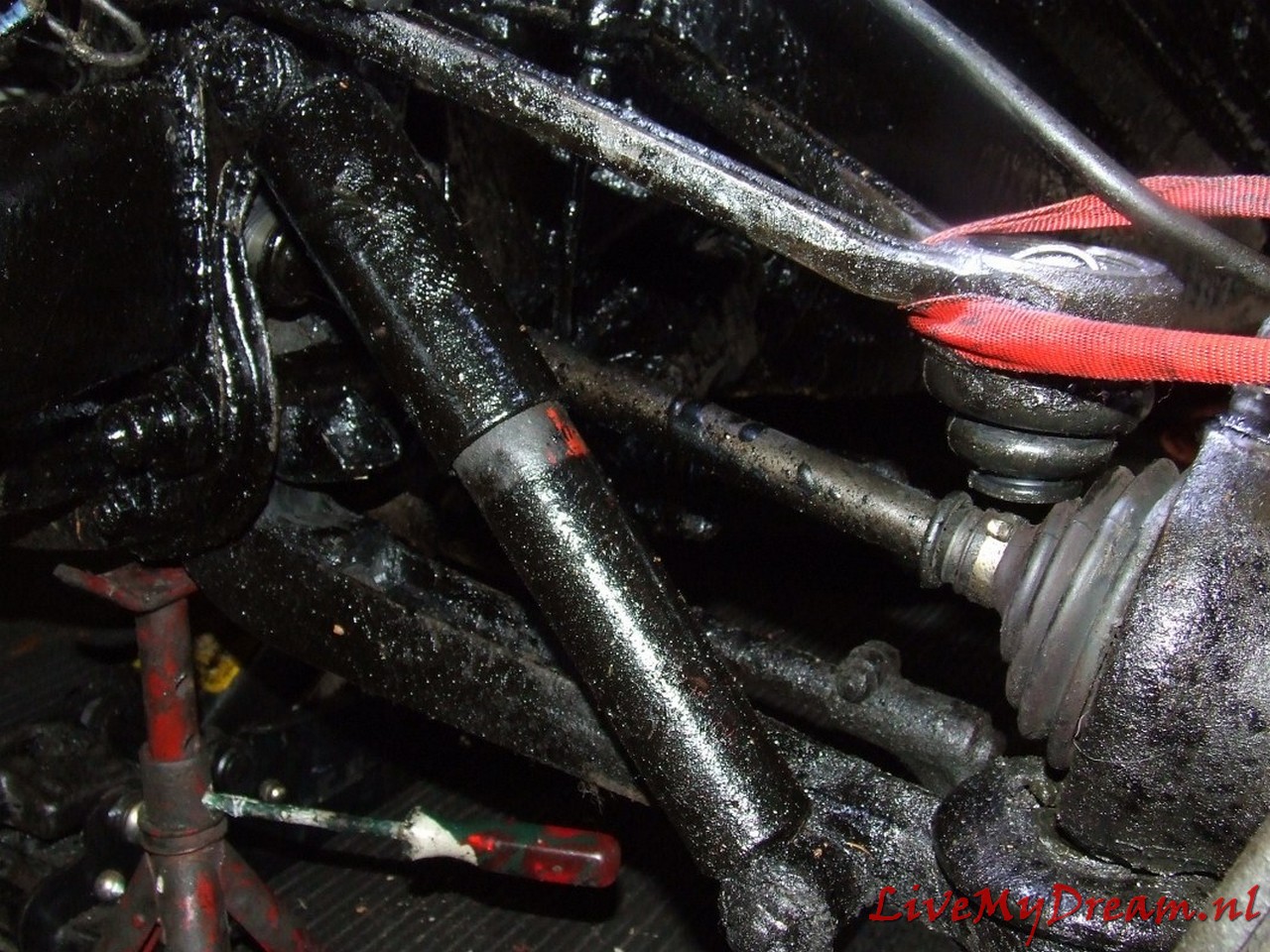
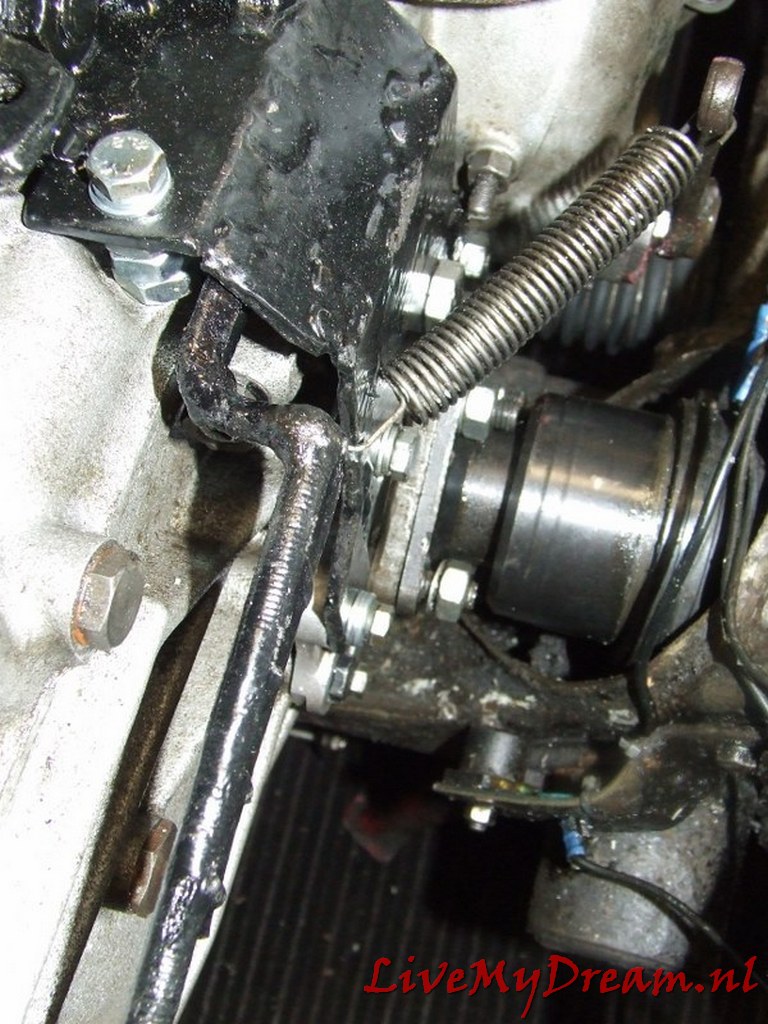
Picture was taken during assembly: nut still tightening and all.
At the bottom right you can see the sensor of the cruise control hanging away.
The magnet is placed under the nut, which is still loose, with a bracket so that the sensor can see it at every turn.
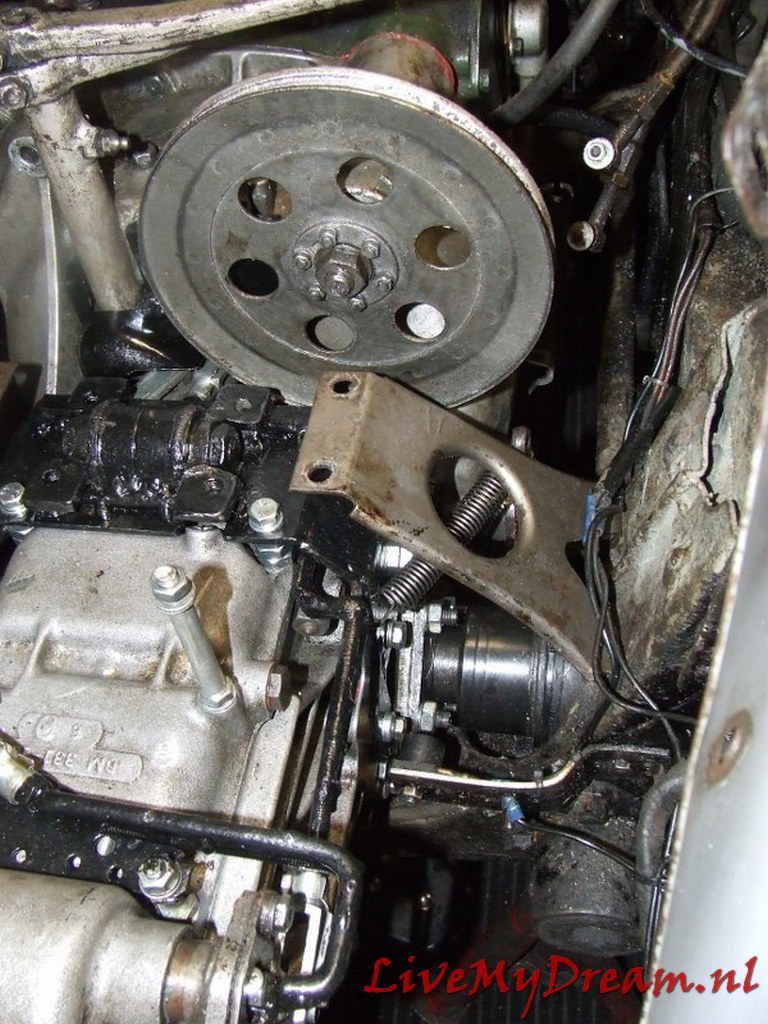
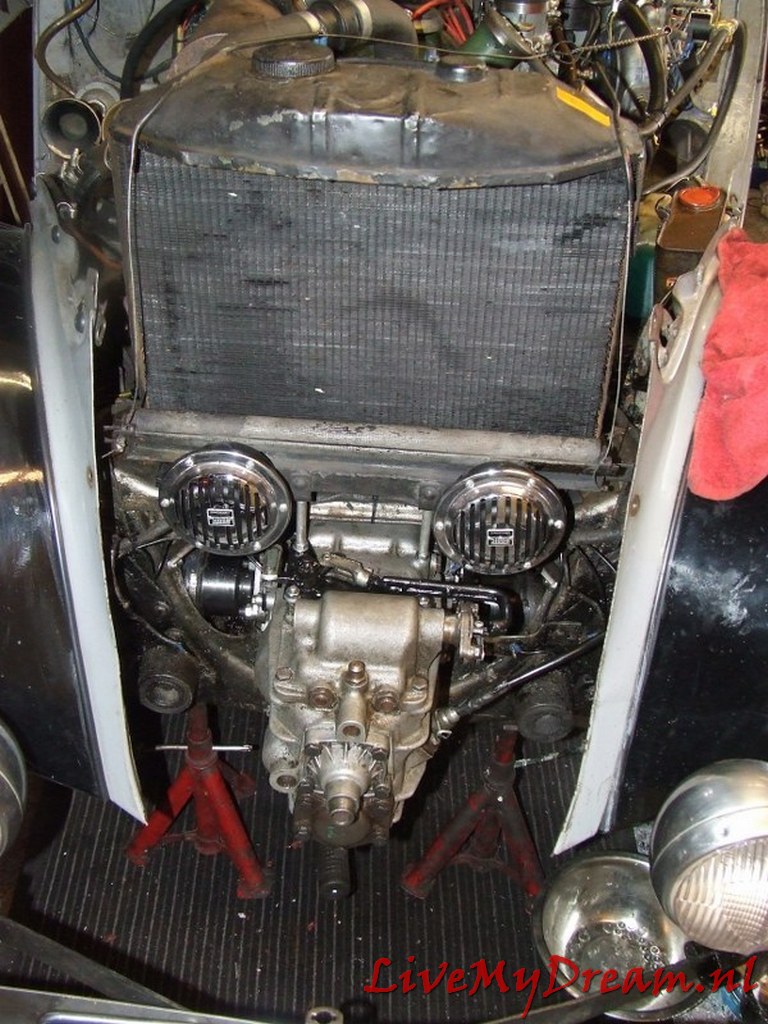
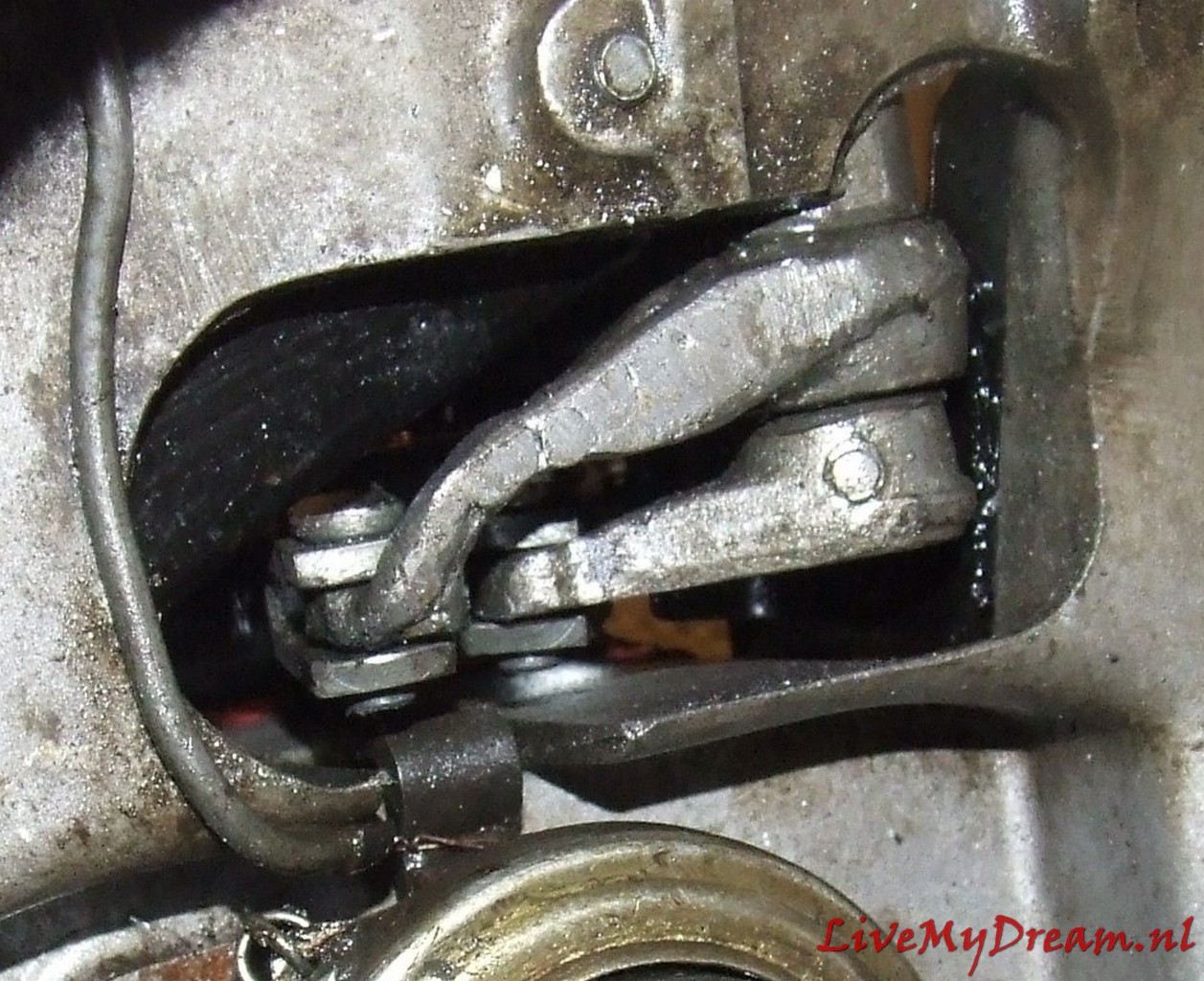
Above the modified spoons from the bottom of the switch tower.
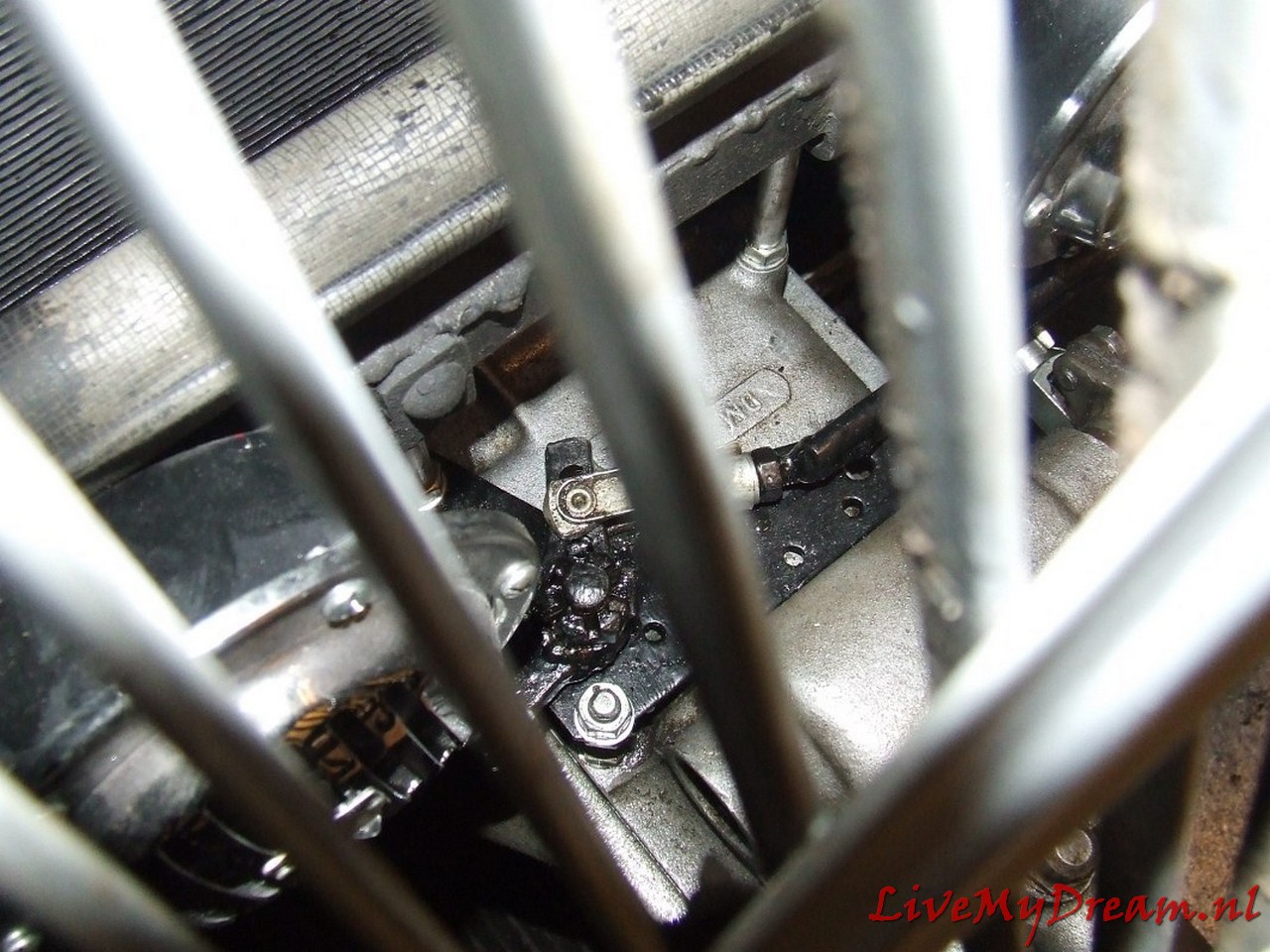
And the final result!
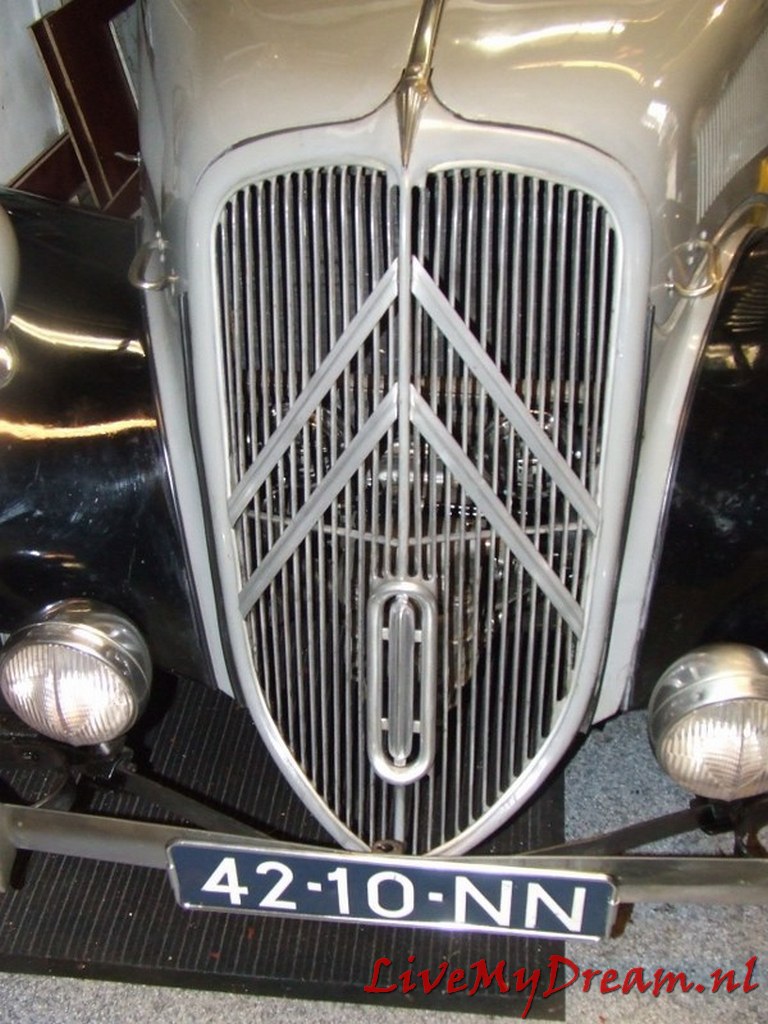